Since wholesale audio and video rental company Rentex launched a radio frequency identification solution to track assets moving into and out of its 10 facilities, the company reports it has gained efficiency and accuracy regarding its inventory counts. Rentex is automatically capturing the ID numbers of tagged equipment it ships out to and receives from its entertainment industry customers. The solution was provided by southern California software company Rental Tracker using UHF RFID tags from Vizinex.
The system was taken live in December 2020, and the company says it has since reduced the amount of time required for employees to pull, pack and ship goods by minutes per order, as well as the time required to conduct annual inventory counts. Rentex is among the largest rental suppliers of audio-visual (A/V) and computer equipment for the entertainment sector. Its customers include hotels, film companies and television productions. “As such, we operate 24-7 in a very fast-paced environment to fulfill our customers’ needs,” says Marcus DeLuco, Rentex’s CTO.
The company assembles rental kits filled with the necessary equipment for each customer, as well as processing returns and performing maintenance before the equipment is put back into service. Traditionally, a time-consuming manual process was required to ensure that all the correct items were built into each rental kit as they were sent to customers, and that all were then returned properly. When an order was being filled, workers typically had to physically walk through the warehouse finding the equipment needed, visually confirm that it was the right item, and then scan a barcode or write down the serial number on paper.
Rentex has hundreds of thousands of assets that it rents to customers, and it houses them at 10 facilities. As such, DeLuco says, locating and confirming equipment before sending it to a customer could take considerable time. The company manages its assets via software that he says is similar to the operation model of rental car providers. Its existing software did not support RFID, though the company wanted the automation that a technology like RFID could provide, to make pulling, shipping and receiving faster and more accurate. Rentex thus began researching new software that could employ RFID to automate asset management.
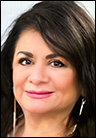
Cindy Trinidad
“We decided to investigate the integration of RFID to increase the efficiency of our warehouse operations,” DeLuco recalls. “It only took a few tests to solidify that RFID had to be inclusive to the planned operational system upgrade.” In January of 2020, the company began working with Rental Tracker—which provides software for tracking and managing inventory in the film entertainment industry—to deploy its RTPro software with RFID technology, cloud-hosted for Rentex. Rental Tracker intends to launch a Web-based version of RTPro in late 2022. The RTPro software is designed to be configured according to a company’s workflows, and to increase warehouse and management visibility, says Cindy Trinidad, Rental Tracker’s president.
When Rentex approach Rental Tracker, it sought a solution that could speed up checkout and check-in times. It also wanted to optimize its inventory and cycle counting, Trinidad says, as well as improve loss prevention by making it easy to locate missing items. Furthermore, the company wanted to obtain an order-verification feature to confirm the accuracy of packed orders as they were shipped. Finally, Rentex wanted to achieve a return on its investment based on the improved efficiency.
The solution was developed and installed within a span of approximately12 months. Rentex adopted handheld UHF RFID readers to locate and identify every asset, Trinidad says. Each item has a passive RFID tag attached to it, encoded with a unique ID number that is linked to the equipment’s information, including its serial number and maintenance history. For the commissioning of tags, Rental Tracker uses a file from tag provider Vizinex that supplies the tags’ EPC codes, and the RTPro software links each tag to the corresponding asset’s information. Rentex’s staff accomplishes the commissioning process in-house as tags are applied to new equipment. This, Trinidad says, is a quick process.
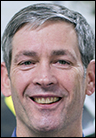
Ken Horton
Vizinex offers Rentex three tags from its portfolio that are designed for the rental-equipment sector, according to Ken Horton, Vizinex’s president and co-founder. The Cable Tag can be attached to cables used by Rentex’s customers for camera or sound equipment, with a holder that is durable enough to sustain the “roughneck treatment the items experience while onsite, while also reading effectively,” he says. The Slim On-metal Tag has a small footprint to fit on a wide variety of metal assets, with a read range of more than 20 feet, while the Duo Tag provides multi-surface mounting and can optionally be used as a hanging tag.
When Rentex receives a customer order, warehouse workers use a pull list of the equipment that needs to be packed for that specific request, such as cameras, lenses, lighting fixtures, projection screens and related cables. The employees then move through the warehouse pulling the necessary equipment and placing it in a staging area. They use a handheld reader to interrogate the tags on all equipment, confirming that the goods match the customer order. If an item is missing, or if the wrong item has been pulled, the workers can view that information and correct the order.
If the equipment requires maintenance, that information can be viewed to ensure it will not be sent to a customer without the proper maintenance. The assets are moved to the loading dock, along with any additional optional equipment required to complete the order, and they are then loaded onto a Rentex delivery vehicle or into a customer’s truck. Data regarding the equipment being shipped is managed in the RTPro software, which can support three staging points with RFID reads, enabling Rentex to use RFID readers again during the receiving process to ensure all equipment is received.
RTPro enables Rentex to conduct analytics regarding equipment utilization, as well as the revenue generated by a parent company, its customers, rental agents, salespeople, projects, locations or departments. It also contains reports for ROI and projections. The software can display or send alerts for pre-configured events, such as goals met, changes to orders and items being sent for repair, and the company conducts annual physical inventories of all the goods at it sites. That process can now be accomplished with RFID, requiring a fraction of the time that a manual inventory count had demanded.
The technology was taken live simultaneously at all 10 locations. The greatest challenge in deployment was the time-consuming process of tagging all the equipment, the company reports, though Trinidad says the software was easily implemented across all sites. According to Horton, the rental equipment industry poses some challenges for RFID technology. Cables, in particular, are often packed in bins or piled on pallets, he explains, with up to 50 cables in very close proximity to each other. Some tags can become obscured in RF shadows cast by the metal of other cables in the same container. The Vizinex tags, he says, are designed with a broad frequency response that enables high read rates despite such conditions.
Durability is another challenge this environment poses, Horton says, which he describes as “important in an environment where customers may not be treating equipment gently.” The small footprint provides the ability to tag goods with constrained space, while the mounting of tags includes peel-and-stick adhesive or hangtag options. Since the system was taken live, DeLuco reports, the RFID functionality has reduced the overall processing time in warehouses. Some functions that previously required more than 20 minutes to complete have now been reduced to 10 seconds, he notes.
There have been some additional benefits, DeLuco says, such as the ability to locate assets if an item is missing. Users can simply walk around the warehouse with the reader in Geiger counter mode until that item is located. Ultimately, he says, many “little benefits” add up to big ones, and some of that is built into the software. “It’s the way the new software handles the tag data that ultimately provides the additional information we had to manually reproduce in our previous system.” That includes information about the movement of goods from a customer to an employee, as well as who had those items, who touched them last and where they are most likely located.
Employees using the technology have responded positively, DeLuco reports, and are working with management to improve functionality and work out any stray tag reads. “We are learning every day,” he states, “and constantly improving our internal processes to reduce unwanted proximity tag reads.” The company’s customer-facing workers have indicated they appreciate the ability to verify inventory instantly.
The customers are seeing the benefits of RFID as well, in terms of the speed at which return documentation is now provided. In fact, DeLuco says, “We are being asked to demonstrate how we use it, [and to] discuss how they can implement it in their own facilities and what hurdles we have encountered during implementation.” In the long term, he says, the company may opt to install fixed readers at portals, such as at dock doors, to further automate data capture.