Since launching an RFID-enabled solution to manage its 4,300 assets, Harvard Medical School (HMS) reports that it has reduced the amount of time required for inventory counts by 75 percent, while gaining greater visibility into where its high-value assets, ranging from servers to microscopes, are located, and ensuring they are accessible during government audits. The university deployed a system provided by Radiant RFID that includes passive UHF RFID tags on assets, a Technology Solutions (UK) Ltd. 1128 sled handheld reader tethered to an Apple iPhone, and Radiant’s Web Application on which the collected data is stored and managed.
The RFID-based asset-management information is uploaded to HMS’s Oracle Fixed Assets (OFA) system. The university was a finalist for Best Implementation in this year’s RFID Journal Awards, and Jeff DiCiaccio, HMS’s director of strategic procurement, presented the deployment’s history and successes at RFID Journal LIVE! 2021, held last month in Phoenix, Ariz. Harvard Medical School has approximately 4,300 assets among its 15,000 capital assets, which include servers, incubators, medical freezers, centrifuges, microscopes and thermocyclers for DNA research.
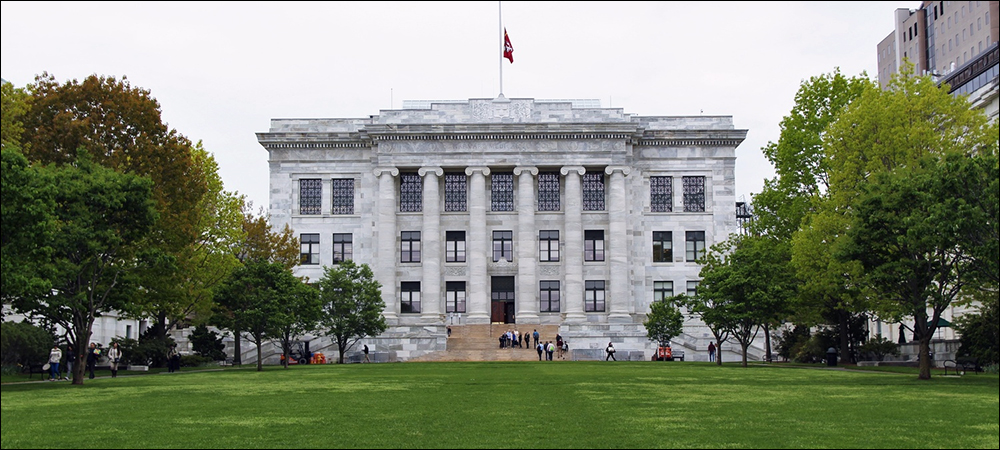
Harvard Medical School
Nearly half of these assets are purchased with funds from external sources, including government-sponsored grants and contracts, and the school is responsible for ensuring the equipment is properly managed. To ensure this is the case, the university submits to a biannual audit by Price Waterhouse, as well as conducting internal inventory counts. “We have to be good stewards of the money we use,” DiCiaccio says, including the assets purchased to conduct its research.
Before deploying the RFID solution, HMS performed inventory counts manually. Typically, each asset was input into Oracle’s Asset Workbench platform, and assigned a printed barcode tag. Research operations managers (ROMs), accompanied by a financial analyst for capital assets, along with DiCiaccio, then carried a Microsoft Excel spreadsheet through every department or lab seeking assets, each of which had a unique serial number. No barcode scanner was available, so the data was visually read and compared against the information for a given room on the spreadsheet, while workers could write down any notes or discrepancies.
If the employees came across any asset tags not listed on the spreadsheet, they often had to look it up on a computer in the OFA system to find out if those items belonged to another department. The results of the asset counts were then manually input and uploaded into OFA. This was not only a time-consuming process but also, at times, disruptive. For instance, the medical school’s Department of Neurobiology had more than 800 assets listed on a spreadsheet that spanned 16 pages.
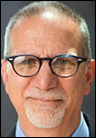
Jeff DiCiaccio
DiCiaccio and Harvard Medical School’s Sophia Xu, a financial analyst for capital assets, would schedule inventory meetings with ROMs for each department, and the latter would escort the team through the labs and help them conduct inventory counts. On average, he says, this process took two hours to locate just 50 assets. “We knew that the previous manual process was not effective and not sustainable,” he states. “The university adds approximately 1,000 assets per year to the total count. While the number of assets increases annually, we had to take action and look at alternatives.”
Therefore, HMS conducted two months of bidding for an automated solution during the summer of 2017, then evaluated proposals and carried out a second bidding process before awarding a contract. Upon selecting Radiant’s solution, HMS began a field trial in two departments that volunteered to be part of the testing: The Department of Cell Biology and the Harvard Program in Therapeutic Science. The medical school overcame such challenges as determining how to orient the reader to ensure stray reads would not be captured from neighboring rooms.
The solution was then launched in July 2018, after which the university spent 18 months retagging existing assets with RFID tags, as well as tagging new products as they arrived. Radiant’s cloud-based Virtual Asset Tracker (VAT) solution comes with a mobile app known as VAT2Go. Tags are preordered and are linked to specific assets when workers scan the barcodes and read the RFID tags. Each tag and its related asset are assigned to a particular room.
When operators begin the inventory-counting process, they employ VAT2Go, running on an iPhone, and input the building, along with the room they are entering. As they read the tags, they can view the results in the app. They can view all assets confirmed to be in the specific rooms in which they were expected, along with any that were missing from the rooms they were supposed to be in, and any found in a room that weren’t supposed to be there. The results are synched with the VAT2Go Web-based application, and users can download a report from VAT and upload it into OFA, which continues to be the university’s system of record.
“The Web-based app allows us to make individual and mass changes,” DiCiaccio says, “either through uploads or manually.” That could include reassigning assets to another location, for example. HMS can also use the solution to retire assets in OFA and remove them from the VAT system. The benefits of RFID management include more accurate and more efficient inventory counting, DiCiaccio reports, which means ROMs and asset managers conducting inventories with them spend less time in the labs interrupting research. The actual inventory-counting process, he reports, is less disruptive than the manual version.
The process of deploying the technology has been a journey that has included negotiating some obstacles, DiCiaccio says, and funding proved to be a challenge that slowed the process. Some project members initially leading the effort left to pursue other jobs, and the COVID-19 pandemic led to the school shutting down in March 2020, with only essential workers allowed onsite. DiCiaccio couldn’t be there himself, nor could Xu, so she mailed the tags to ROMs onsite as new assets were purchased and received.
Since the system was taken live, DiCiaccio says, only a single inventory count has been conducted, due to the pandemic. However, he notes, the results of that one count proved the time savings. “One of the beautiful things about RFID,” DiCiaccio states, “is if a Cell Biology asset is located in Neurobiology, or even at another Harvard school in a Cambridge location, RFID doesn’t care which department it belongs to. It will read all of the assets in that room,” thereby sparing the need to look up asset information for each individual department or school.
Audits conducted by Price Waterhouse do not require RFID tag reads, though RFID provides preparation support since the school can locate any items selected for audit and ensure they are readily available when auditors arrive. To date, this has consisted of a virtual audit conducted in a Microsoft Teams meeting. Going forward, DiCiaccio says he expects the technology to provide benefits for other activities, such as the renovation of a lab space. An RFID reader could scan the space before the renovation, then again when a move is completed into the newly renovated space, in order to prevent items from going missing.
Another benefit is the ability to locate a missing asset by searching for an RFID tag with the reader in Geiger counter mode. In 2019, DiCiaccio recalls capturing an unexpected tag read of a refrigerated centrifuge that was not visible. “I was getting a read,” he says, “but I couldn’t find it.” As he moved the reader closer to the signal’s source, he discovered the asset in a drawer of a wooden bench. “Had I not had RFID, we might have thought the asset lost, stolen or disposed of, but with RFID I was able to see an invisible asset.”
The RFID system is now being implemented or has already been taken live at the university’s Faculty of Arts and Sciences, School of Engineering and Applied Sciences and Wyss Institute, in addition to the HMS. Wyss has completed the tagging of all older assets with RFID, DiCiaccio reports, while FAS and SEAS are now in the process of tagging approximately 8,000 assets. The four schools have assets in around 100 buildings.