Knapp, an Austrian firm specializing in warehouse automation and logistics, has developed an RFID-based conveyor system for sorting and packing goods in a specified sequence. The solution ensures that items can be placed within boxes in the correct order—for instance, with the heaviest products on the bottom—and that packages can be loaded onto trucks in a particular sequence, so they can be unloaded easily at various stops along a delivery route. At present, the system is being installed at a warehouse operated by Olymp, a German manufacturer of men’s shirts.
To create its Pick-it-Easy Pocket solution, Knapp outfitted its hanging conveyor with a radio frequency identification tag on each of the conveyor’s roll adapters—ring-shaped receptacles from which objects being conveyed are hung. A cloth bag, designed to hold almost any sort of merchandise, is attached to each roll adapter. The Pick-it-Easy Pocket system can comprise several thousand tagged roll adapters, depending on its size, each containing a passive 13.56 MHz RFID plastic-encased tag conforming to the ISO 15692 standard.
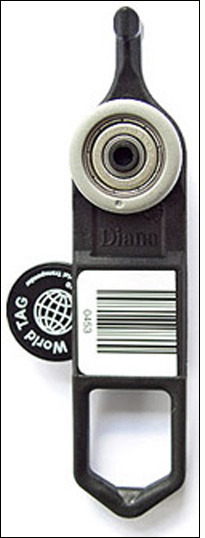
The bags, or “pockets,” that hang from the conveyor at each roll adapter are used to hold merchandise sorted and sequenced by the system, according to Oliver Lehner, the head of product management at Knapp, which is headquartered near the southern Austrian city of Graz.
“Systems for sequencing goods are something our customers have been asking for ever more often,” Lehner says. The solution is well suited for e-commerce operations, he adds, given its ability to sequence the picking of items and make the handling of returns easier. (E-commerce businesses, Lehner explains, typically have high return rates.)
To use the system, workers stand at a Pick-it-Easy Pocket station along the conveyor, where they remove goods from their original shipping case—for example, 10 dress shirts—and place each object into a separate hanging cloth bag. Prior to inserting an item into a hanging bag, a worker uses a bar-code reader built into the Pick-it-Easy Pocket station to scan the bar-code label attached to the garment’s plastic packaging. The solution then indicates in which hanging bag that item should be placed, based on the details of the batch-picking work order.
A built-in RFID reader on the conveyor track identifies each roll adapter by reading the unique ID number encoded to its tag. The system then links that ID to the bar-code data about the contents of the hanging bag. The RFID tags and interrogators are produced by Turck.
The bag of merchandise remains on the conveyor until all items within that batch have been picked and it is time to pack a shipping carton. At that point, bags are automatically moved along the conveyor to another station for packing. If a customer has requested a batch including seven items, for instance, the seven cloth bags holding those products will be moved into the order specified and then be forwarded to the packing station, known as Pick-it-Easy Pack.
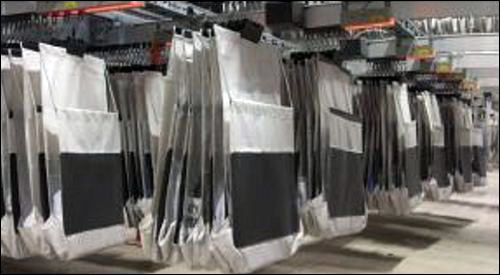
Workers unpack the cloth bags from the front to the back of the conveyor line, placing the items in that same order inside the shipping box. Because the RFID tags associated with those hanging bags were interrogated at various intervals, the product within each hanging bag has been accurately identified, thereby enabling the system to make sure the goods are in the proper order for packing.
“For batch-picking of e-commerce orders, it’s important that heavier items get placed at the bottom of the box,” Lehner states. “Our system makes sure the items are in the right order for packing.”
As goods are moved around by the sorting and sequencing machine, the RFID tags are interrogated at two key conveyor switching points, as well as at other locations along the conveyor system.
“There are dozens of reading points,” Lehner says. “We read the tag every 30 to 40 meters [98 to 131 feet] to make sure nothing is out of order or missing.” Knapp’s customers, he adds, are interested in the solution because it provides accurate sorting and process reliability. “The RFID tags are far more durable than bar codes, which can easily be ripped when hanging bags are fed into and out of the conveyor system.”
In addition, the company reports, customers are looking for operational savings and solutions that can be quickly adapted for changing business requirements. Olymp was performing batch-commissioning by hand prior to purchasing the system, which Knapp tested before bringing it to market.
The Pick-it-Easy Pocket and Pick-it-Easy Pack stations were developed simultaneously, Lehner says. They were designed as part of Knapp’s broader solutions for warehouse automation. The conveyor systems are manufactured by Duerkopp, which became part of the Knapp Group in 2010.