- RFID Brings Laundry Services to Remote Locations
- Using RFID Readers, Antennas, Cameras and a Solar Panel
- Leveraging Technology Experience from Years of Testing
Australian commercial laundry company Specialised Linen Services (SPL) has deployed and patented a new RFID technology-based solution for managing self-service linens operations out of a fully autonomous, mobile structure. The system was developed to serve the Airbnb market, but it is being considered as well for use by university residences and resorts in Australia and Europe. With the company’s Mobile Linen Hub, business operators can drop off their soiled sheets and towels, then help themselves to clean ones, without placing orders or waiting for delivery drivers.
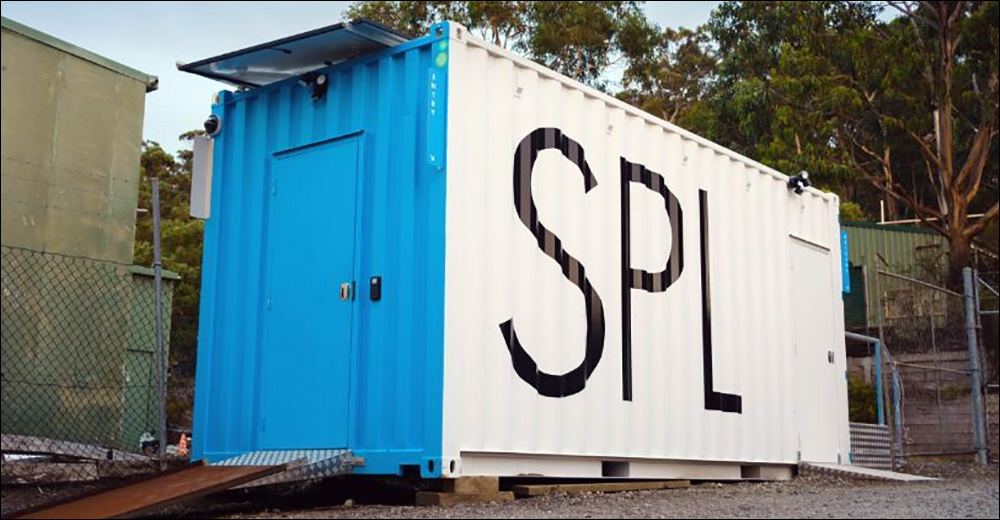
SPL’s Mobile Linen Hub
The unmanned unit stores clean linens for use by service subscribers such as neighboring Airbnb businesses, and it also receives soiled linens. Its UHF RFID readers and antennas capture the ID number of every item removed and returned by customers, then bills them accordingly. Cameras provide further data by identifying movement to indicate when people are onsite, while capturing video recording during that time. Solar panels provide power, with a 4G unit linking data to the cloud. The solution is provided by RFID managed services company High Frequency.
SPL is a Melbourne-based family business, says Ray Hayes, the company’s executive director, and has been growing its clientele throughout Australia. It is the second largest laundry provider in that country, he reports, with eight sites and 11 distribution centers. A private equity firm purchased SPL in September 2018, providing the resources to investigate innovation, including development of the Mobile Linen Hub. The company has a large presence in the hospitality market, Hayes says, as well as years of RFID technology experience, as it has been using UHF RFID tags and readers to track linens traveling to and from customer sites and through the laundering process.
RFID Brings Laundry Services to Remote Locations
At the time SPL began developing the Mobile Linen Hub, Hayes recalls, Airbnb was becoming a market that laundries in Australia (and beyond) found difficult to serve. Airbnb’s marketplace consists of numerous small businesses, seasonal by nature and spread across wide areas. “Particularly in the southern areas of Australia,” he explains, “they’re located in high tourist spots, but in the winter months obviously there are very big swings in linen consumption.” Servicing these small businesses had involved sending delivery trucks to pick up soiled linens and drop off clean ones, which meant workers spent a great deal of that time driving from one site to the next.
For customers, an order for clean linens could thus be significantly delayed. “We found that with a linen hub, that challenge would be removed,” Hayes says, “because we could offer one central delivery point for the laundry.” The Airbnb operators could retrieve linens themselves at a central neighborhood location, at a time convenient to them. To manage the inventory, however, the company needed intelligence to understand what was onsite, what needed to be stocked, and which soiled linens needed to be picked up.
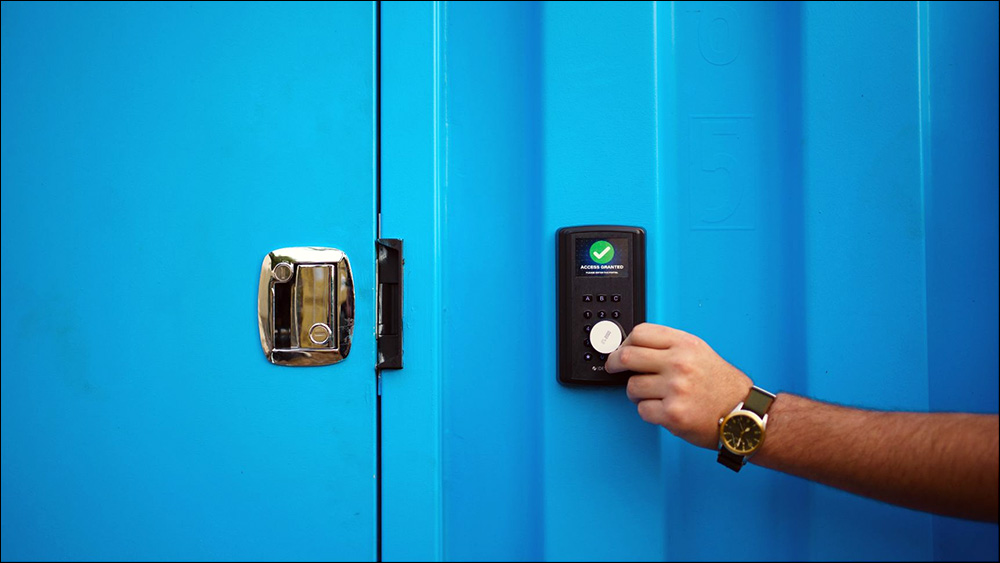
Users receive a contactless access fob with which they can use the unit.
At that time, Hayes says his son, Isaac Hayes, had founded High Frequency, an RFID and Internet of Things (IoT) solutions company. High Frequency leverages a variety of RFID technologies, as well as Bluetooth Low Energy (BLE), for IoT solutions. The firm provides software and integration, and it serves the laundry industry, in addition to retail, mining and other sectors. SPL and High Frequency collaborated to develop an intelligent, unmanned hub, and the first Mobile Linen Hub was taken live in 2021. At present, five such units are in use in various parts of the country.
Each Mobile Linen Hub consists of a 20-foot steel container, built by a third-party to be moveable on a trailer. It comes with three rooms, an entrance, and clean and soiled linen storage areas. The unit can be delivered to a site at which multiple customers are located nearby. Users receive a contactless access fob with which they can use the unit. Upon arrival, they can scan their access card to be identified by software, and a chute is released so they can throw soiled linens inside. A reader at the chute identifies each linen based on the unique ID encoded on its sewn-in passive UHF RFID tag. Once the item is identified, it is displayed on a screen so users can view and confirm what has been placed in the chute.
The users can then utilize the same fob to enter the container, which contains an entryway with shelves and a built-in reader to identify the tagged items placed on the counter. Thousands of products can be stored in the unit, all with RFID tags attached. Users would walk into the storage room, select the required items, return to the entryway and place those linens on the counter. A screen would display what they have taken, and they could simply pick up the items selected and leave. The reader in the storage area would no longer read those tagged items, causing the unit’s inventory data to be updated in the software.
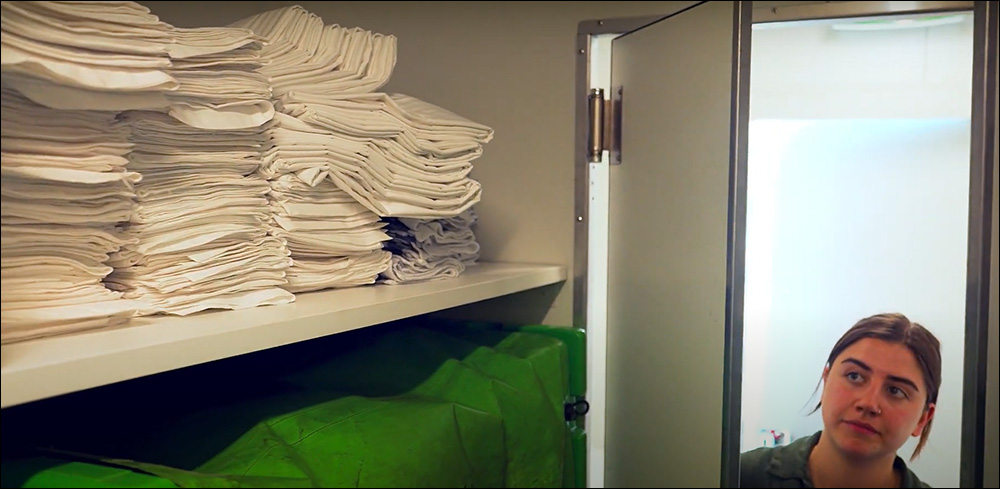
The container includes shelves and a built-in reader to identify tagged items.
Using RFID Readers, Antennas, Cameras and a Solar Panel
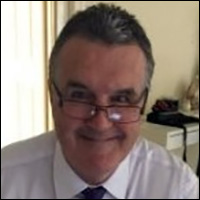
Ray Hayes
Cameras are used for object detection to identify that an individual has entered the unit. The system can record video of an individual’s time onsite for historical records, in case a discrepancy takes place. For those onsite, Ray Hayes says, “There’s zero interaction with having to press buttons or do anything. They just take the linen that they want and then they leave.” The software automatically bills their account, and data from the unit is forwarded to the cloud via a 4G connection.
Each unit features three Impinj R700 UHF RFID readers and more than 20 antennas, Isaac Hayes says, primarily located inside the clean area. UHF RFID was the best technology option, he explains, since the linen tags are relatively low-cost, can sustain washing and are already in use by SPL to track commercial linens for the healthcare sector. For SPL, the solution is a way to further leverage the RFID technology it has been using. “I’ve been a very strong proponent of RFID in laundry industries for many years,” Ray Hayes notes, “but the technology is just catching up to a point where we felt that it was robust enough for this concept.”
The UHF RFID tags are applied to linens at the point of manufacture. SPL presently employs RFID readers at a large laundry site in Melbourne, for instance, where approximately 600 tons of laundry are processed each week for hotels, hospitals, nursing homes and other commercial customers. A larger percentage of the businesses are using the RFID data captured by onsite RFID readers, Ray Hayes says.
Leveraging Technology Experience from Years of Testing
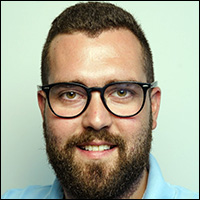
Isaac Hayes
The existing use of RFID, as well as the company’s experience with the technology, eased the transition into SPL’s use of the Mobile Linen Hubs, according to the younger Hayes. “We were only able to implement it because SPL had already taken significant strides to ensure that their plant was RFID-capable,” he states, “and they were already doing that with their existing customers.”
The technology is intended to serve very small companies in remote locations. It can identify an area where real-estate agents, property managers or small mom-and-pop Airbnbs could sign up for access to the hub. The cloud-based software, designed by High Frequency, collects usage data that provides the option for analytics—for instance, tracking how many times a specific towel or sheet is used, along with each item’s return rate.
Ultimately, Ray Hayes says, “The unit increases our efficiency of servicing the Airbnb sector.” So far, he adds, feedback has been positive. “The Airbnb customers absolutely loved it.” If those same businesses were contracted with other commercial laundry companies, they would typically have had to pre-order all necessary linens, then wait for the delivery to be dropped off at a collection point or onsite. “Now, if they want to turn up at 11:00 at night and pick up five pillowcases and a face washer, they’re able to do that without a problem.”
Key Takeaways:
- The unmanned, intelligent linen unit enables Airbnb business owners to drop off dirty linens and pick up the laundered versions with the tap of a key fob.
- With RFID readers capturing inventory in soiled and clean linen storage, SPL has a real-time view into the conditions inside the Mobile Linen Hub and can thus stock it appropriately.