As Internet of Things applications become more widely deployed, there is an increasing demand for edge devices that communicate wirelessly and are powered by batteries. But as the advance of technology has allowed for the ever-decreasing size of our computing devices and provided us with mobile devices that we may have never expected, there is increasing talk about how battery technology has just not kept up. There is, after all, no Moore’s Law for batteries, and so the progress that we have seen has been slow in comparison, with battery sizes and capacities that are not much better than they were a decade ago. But rather than long for a dime-sized battery that will keep your cell phone operating for a week or more, there is another way to look at batteries: eliminating them entirely.
Many IoT devices, communicating via Wi-Fi, Bluetooth or Bluetooth-LE—or via one of the emerging low-power wide-area networking protocols—will need to operate in environments where battery refreshes are not possible. A common design target is for the edge device to operate in the field for 10 years without a battery replacement. But when operating lifetime estimates are simply based on power consumption—calculated from the discharge rate of the battery—we tend to see an unacceptable number of battery failures in the field.
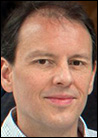
Batteries are chemical devices, and ensuring their reliability is a challenging proposition. You don’t have to look far to find a news article about a catastrophic failure of a lithium battery. While those events are actually quite rare, it is illustrative of the very real problems associated with delivering a high percentage of batteries that will live up to their rated lifetime. This is rarely the case due to all manner of variables, including exposure to temperature extremes, improper storage, errors during device assembly and premature activation.
But powering IoT devices through energy-harvesting techniques is an alternative to deployments being dependent on battery reliability. To harvest energy, a circuit scavenges power from energy sources that are already present for reasons other than powering the circuit. A solar-powered module is an example of energy harvesting, as is a self-winding watch that uses the kinetic energy of the wearer’s arm movement to keep the watch running. For IoT applications, there are many more interesting power sources to consider.
Perhaps the best-known example of energy harvesting in edge devices is in passive radio frequency identification (RFID) tags, which are powered from the RF energy delivered over the air from nearby readers. As the distance from the reader increases, the power available to the tag is reduced to microwatts, but advanced circuit techniques and semiconductor processes keep the circuit power consumption to usable levels. Equally important, the most commonly used signaling protocol for passive RFID tags, EPC Gen 2, has been designed from the start to facilitate low-power operation.
The battery-less operation of RFID tags is explanatory of other RF power-harvesting opportunities. There is energy available in the carrier waves that are ultimately modulated for communications signals, and it can be put to use in unexpected ways. Signals like wireless Ethernet, radio and television transmissions, and even the 50Hz or 60Hz from AC power distribution, are virtually everywhere and can be scavenged to energize low-power circuits. This is just the beginning.
Mechanical transducers can convert any type of motion to electrical energy, and micro-electromechanical (MEMS) technology is starting to be applied to this application to provide size, efficiency and price points not previously available. MEMS can be thought of as “moving parts on ASIC chips” and are the basis for harvesting power on single-chip devices. That self-winding watch can now be made on a single chip, without a spring to be wound or a battery to be replaced.
Reliability problems can also be addressed by combining energy harvesting with the latest in energy-storage technology, such as supercapacitors. Consider an IoT deployment to monitor the temperature of items in transit. Modules attached to the assets can use temperature sensors which store data locally and are periodically polled by a reader installed in transport vehicles. Depending on the application, asset data can be moved to the cloud, either during transit or at the end of a run. But how best to power the temperature modules? Mechanical transducers can harvest energy from vehicle vibration, but to keep the module size small and the cost down, it may not be enough to power the sensor and store the resulting energy. Including a supercapacitor enables vibration energy to be collected and stored.
Once enough power has accumulated, the module wakes up and stores a sensor reading, then goes back to sleep. These types of designs address not only the reliability of the battery that is no longer needed, but also the reliability of the power source, which may be intermittent.
So far, only RF and mechanical energy sources have been considered here, but advancements in transducer technology mean IoT edge devices can be powered from sources such as waste heat from machinery, chemical processes including biodegradation, salinity gradients, and internal processes in the human body, just to name a few. As IoT deployments proliferate, it will be critical to address the lifetime and reliability shortcomings of batteries and either replace or augment their usage with approaches based on energy harvesting.
Bob Hamlin is the chief technology officer of Tego, based in Waltham, Mass. Tego develops RFID products and related software used in aerospace and other industries. Hamlin is a senior engineering and product-management executive with more than 20 years’ experience and a history of profitable products, including semiconductors for telecommunications and RFID tags.