- Finding the Right Tags for Pallets and Their Use Cases
- Manufacturers Track Assets and the Products Loaded on Them
- Flexibility and Durability for Any Environment
Packaging and pallets company TriEnda has begun providing RFID-enabled versions of the products its customers use to containerize and transport newly assembled products. The company reports that it has teamed up with RFID tag maker Metalcraft to provide RFID tags that can be applied to its reusable pallets and thermoformed packaging to enable customers to better manage those assets’ location and status. In some cases, businesses are also using RFID-based data to understand the locations of goods loaded on those assets. In that way, they can better manage the efficiency of goods shipments to their customers. VI Agents Solutions is providing software and integration.
TriEnda is reportedly North America’s largest manufacturer of thermoformed packaging and material-handling solutions. Its products include room dividers, reusable pallets, sleeve packs and reusable bulk containers, as well as delivery carts, cargo-protection systems and battery packs. Throughout the years, customers in the automotive and food and beverage industries have inquired about bringing intelligence to pallets and packaging via radio frequency identification. Many of its manufacturer customers have been testing or deploying RFID systems to track supplies, work-in-progress and shipping data, including to increase their IT capacity to manage RFID data.
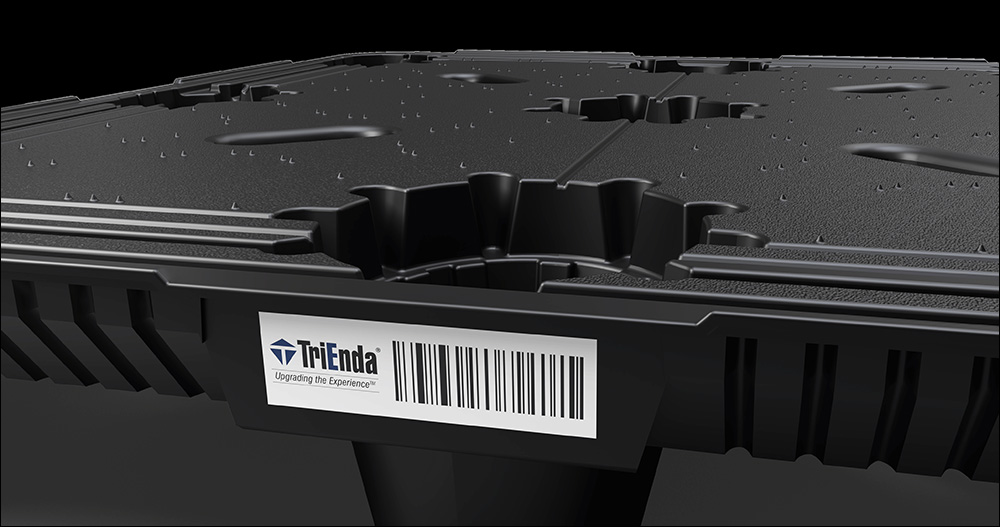
TriEnda and Metalcraft have partnered to provide innovative packaging solutions.
Finding the Right Tags for Pallets and Their Use Cases
The company researched potential options before teaming up with Metalcraft, which manufactures customized, durable RFID labels and tags. “We knew of Metalcraft in the industry, so we contacted them about RFID,” says Heidi Bulgrin, TriEnda’s manager of new product development. Approximately two years ago, she recalls, the companies began devising a system of selecting the most effective tag for each form factor of pallets or containers, as well as for each use case.
A company in the grocery sector was the first to employ TriEnda’s RFID-enabled pallets, while businesses selling food and beverages are planning to use the tagged assets as well. “Their primary incentive is to prevent pallet loss and help them track and keep their assets in order,” Bulgrin says, adding that plastic pallets can be expensive. They are built to last for a long time, and they are valued for that longer life, compared to traditional wooden pallets.
Some businesses are transitioning from wood pallets to TriEnda’s reusable ones, and they may use these new plastic products with RFID tag-tracking capability. By applying tags, Bulgrin says, TriEnda can enable customers to use the data in a variety of ways. For instance, she adds, the technology could help companies manage goods packed on a given pallet, or they can simply track an asset.
Manufacturers Track Assets and the Products Loaded on Them
Companies that already have RFID readers onsite for tracking UHF RFID-tagged components, equipment or materials can leverage their existing system to capture the pallet or packaging tags’ ID numbers. Each ID is linked to data about the corresponding product. The tag can be read at any key point along the manufacturing or shipping process, where fixed UHF RFID readers are installed, or where workers carry handheld readers. For instance, when a pallet is loaded with goods, a company can read each tag to update that pallet’s status.
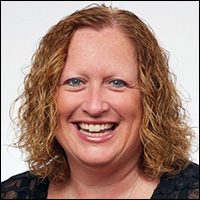
Heidi Bulgrin
If the pallet is shipped, the tag can be interrogated as it is loaded onto a truck. The software could link that shipment to the date and time, as well as to the customer receiving that pallet. The manufacturer could then track who had the pallet and when it was returned. If the pallet was not returned on time, the manufacturer could send a notice reminding the customer to do so. The pallet tag could also be read as the pallet underwent washing, sanitization and repair processes before being used for another shipment.
All data related to these activities could be stored in a user’s software, indicating not only where an asset was located, but also how many times it had been used, when it was inspected or maintained, and when it may require replacement. The tagging of TriEnda products is part of a trend taking place across the manufacturing industry, according to Mike Winchell, Metalcraft’s territory specialist. By now, Winchell says, many users understand what RFID is and what it can do, and they are prepared to invest in the technology to become more efficient or eliminate bottlenecks.
TriEnda recommends working with VI Agents Solutions, which provides systems related to RFID data collection, as well as others that leverage LoRaWAN technologies. “We have an end-to-end software solution that can be used with any RFID equipment and tags” says Tim Shideler, VI Agents Solutions’ president and CEO, and that can provide a sensor-based solution for cold chain monitoring or other use cases that require real-time temperature or humidity tracking.
Flexibility and Durability for Any Environment
TriEnda has attached the tags to the exterior of each pallet, where they can be visible to those handling the pallets. They come with human-readable serial numbers and barcodes. “A tag that has an RFID chip, a barcode and a human-readable number means that you have three failsafe forms of identification on that pallet,” Bulgrin states, and that the tag is intended to last throughout the pallet’s lifetime. Many companies are opting to apply multiple tags to a given pallet in order to ensure a read from either side.
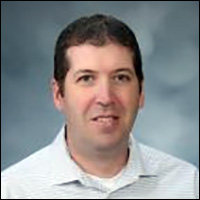
Mike Winchell
Customization is key to the offering, Bulgrin says. “We don’t use the same kind of tag for everybody,” she explains. Based on exposure to specific temperatures, chemicals, liquids and other environmental factors, TriEnda will determine the best RFID tag for each particular product and customer. It can thus provide a tag and attachment based on in-house testing and experience. “Often,” she states, “we will say, ‘There are 10 samples. Try them out. Do your worst and see if they survive.'”
For instance, the automotive manufacturing site is typically a stringent environment, and so tags must sustain the presence of chemicals without being damaged or falling loose. On the other hand, some food manufacturers may put the products through sanitization processes and power-washing. “Metalcraft makes custom, durable tags. That’s our forte,” Winchell states. “Everything is designed based on the application.” That fits with TriEnda’s own business model, he adds, by which its own pallets can be customized.
The early adopters of TriEnda’s RFID-enabled products have reported benefits related to reduced asset loss and better management of their assets so that they are available when needed for production or shipping. “Seeing their benefits,” Bulgrin says, “we’ve been sharing that capability with other customers.” Initially, those customers are in the United States, where TriEnda is based, though the RFID-enabled products are also available in Europe.
According to Bulgrin, the company will continue to offer the non-RFID version. “But I do see customers really wanting that technology going forward,” she states, adding that it represents “a small cost” of the overall product. TriEnda could also retrofit existing pallets that customers use, though the RFID functionality has so far only been applied to new products before they are shipped to the company using them.
Key Takeaways
- Manufacturers that already leverage RFID technology at their production sites can track pallets and packaging from TriEnda with the company’s new offering.
- The Metalcraft tags are being designed, along with TriEnda’s products, to meet the specifications for customer environments and use cases.