Damage occurs with approximately 2 percent of all shipped products, according to SpotSee, a company that specializes in shock detection, and shippers, brands and retailers typically absorb this cost. When, where and how damage occurs is often unclear. SpotSee has targeted that challenge with a variety of solutions throughout the past decades, but most recently it has introduced RFID technology to capture data wirelessly. With RFID, some businesses are leveraging their existing RFID reading technology for supply chain and inventory management to also collect shock data automatically.
SpotSee’s ShockWatch RFID solution consists of a passive UHF-enabled impact indicator. The company partners with systems integrators that can provide integration with existing software or cloud-based software services. The battery-free ShockWatch devices, which contain a low-cost mechanical indicator and an RFID chip, harvest energy from the UHF interrogation of the tag in order to transmit a unique ID and notice if a shock event has occurred. The company discussed the technology and how it is being used at last month’s RFID Journal Virtually LIVE! event.
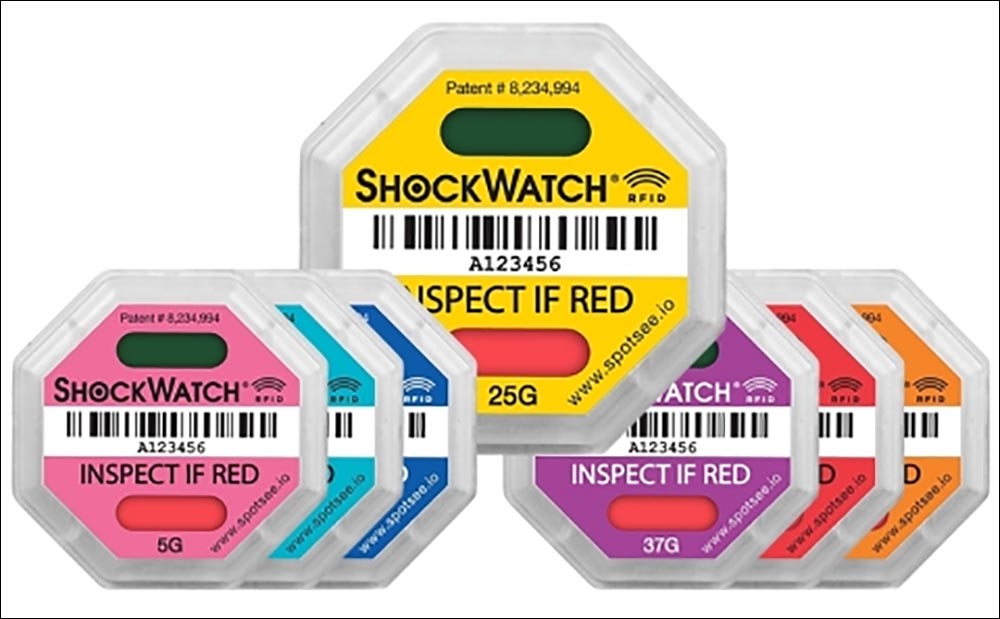
SpotSee’s ShockWatch RFID solution consists of a passive UHF-enabled impact indicator.
Numerous brands, original equipment manufacturers and shipping companies are using the system, though they have asked to remain unnamed. Most commonly, the technology is used to detect impacts on goods such as aerospace or automotive parts, sensitive medical equipment or electronics. The ShockWatch product is designed to deter bad handling behaviors, the company explains, since users know the technology is in place.
In the event that an incident occurs, such as a drop or other heavy impact that could cause damage, the system provides data and software analytics to help shippers or product owners understand what has occurred, address the issue and prevent future such incidents. The company has been making products for the identification and prevention of shipping damage since 1974. Because things can go wrong in the supply chain, shipping damage costs about $2.3 trillion worldwide each year, according to Tyson Stuelpe, SpotSee’s global sales leader.
SpotSee’s customers have achieved an approximate 40 to 60 percent reduction in damage when the system is deployed, according to Jan Van NieKerk, the company’s VP of engineering and innovation. SpotSee provides mechanical impact sensors that display a visual notification if an impact has occurred. The impact device comes with a window, a coil and a red plastic sheet that slides into the window so that it can be viewed in the event of an impact. The company has also incorporated other environmental sensors and cellular connectivity for tracking high-value goods in transit.
In 2017, SpotSee combined several of its brands, including ShockWatch, to create a tracking network designed to help customers identify damage to their assets in real time, no matter where in the supply chain such damage may have occurred. If a tagged item experiences a drop or other impact event, the sensor mechanical release visually indicates that action, and the system can transmit that data so users do not need to physically check the front of each device. “By adding RFID, we use modern, ubiquitous state-of-the-art technology to detect and transmit the status of this indicator,” Van NieKerk says, adding, “The fact that we don’t have to use a battery means it has unlimited shelf life.”
To set up the system, users must configure the devices. They input four lines of code related to such dictates as the amount of memory required and how many words need to be read during an interrogation. The tags can be placed in a carton or be attached to a product. Companies are deploying the devices in the supply chain, as well as when items (electrical equipment, for example) are used. As such, the devices are applied throughout the supply chain, wherever damage is experienced. Some customers are applying the tags to sensitive equipment at the point of use, Van NieKerk reports, to ensure that such items are handled with care.
In the most common use case, tags are applied by manufacturers and others along a supply chain. After the tags are programmed and applied, they are read at shipping and receiving points, such as at a warehouse or distribution center dock door. “However, since RFID makes for fast, convenient inventory, tags are also read during inventory sessions,” Van NieKerk says. For instance, a user equipped with a handheld reader can capture the tags of goods throughout a warehouse for two purposes: inventory counting and damage detection.
Who can access the resultant data may vary, Van NieKerk explains. Companies can set up proprietary software and determine which stakeholders can share access to the data as a product moves through the supply chain, or they can create a public blockchain system. For manufacturers, the tags can reduce their cost of goods returned due to damage, by deterring what damage has occurred and detecting who was the custodian when this happened. Retailers, meanwhile, can benefit from knowing if a product has experienced shock upon receiving new goods.
The read range is designed to be long enough so that tags can be read from the distance of a typical dock door’s width, Van NieKerk reports. The tags can be interrogated by any off-the-shelf UHF RFID reader. While the solution is most commonly in use in the automotive and aerospace sectors to track products being made and built into assemblies, it is also used for tracking electronics, such as server racks moving to their destination, or for monitoring medical equipment or other highly calibrated instruments. Other use cases include the transport of foods, as well as beverages packaged in glass containers.
The RIFD indicator device is tamper-evident, so it can be visually detected if the adhesive has been broken. Because it doesn’t have a battery, the company reports, the device will likely operate for a decade. “We provide a two-year lifetime based on the life of the adhesive,” Stuelpe says. Future versions of the tags could include temperature indicators.
The RFID ShockWatch tag has a suggested retail price of $2.40 per tag, which drops in high volumes. “Since you have visual indication, you could start using it in the supply chain without an RFID reader,” Van NieKerk says, then deploy RFID in a supply chain system. The products provide sensitivity thresholds from 5 to 75 g-force. There are seven increments provided, and users can match those thresholds with the relative fragility of the products being shipped. SpotSee provides tables to help companies identify the g-force sensitivity that they might need, based on the products being tracked.
“Many of our customers simply run tests” with their own products, Van NieKerk explains, to determine the best device sensitivity required. Sensors can detect the direction of the impact vertically or horizontally, based on the mechanical switch. Users seeking direction detection from all sides can use two tags to provide north-south or east-west impact detection. Companies can use several devices set to different g-force impact-detection ranges in order to understand how strong an impact was. Because there is no battery, the device does not record the time of the impact. “Key for many of our customers,” Van NieKerk says, “is not knowing the exact time [of an event], but understanding custody at the time of an incident.”
For real-time data, the company offers a cellular-based damage detector known as SpotBot Cellular. If the unit detects an impact, it immediately transmits data via the local cellular network. This detection via real-time data helped a major car manufacturer identify the cause of damaged windshields arriving from a particular supplier, van NieKerk says. After installing a SpotBot on a pallet loaded with windshields, the company discovered a railroad crossing that gave the delivering truck a significant bump every time it went over the rails. Once the crossing was repaired, he says, no further damage was experienced.