Food-processing technology company Marel has released an RFID-enabled system that moves fish through weighing, trimming and quality-control processes, while tracking data and identifying product for inspection, based on information collected by RFID readers and antennas. The solution, known as Production Control Flowline for Filleting and Trimming (or ProCon Flowline), consists of a modular unit with a conveyor, stations for employees to conduct trimming, another station for inspection and two weight scales—all with built-in ultrahigh-frequency (UHF) RFID reader antennas to interrogate tags built into baskets containing the fish.
Most fish processing is performed manually. The fish, often already cut into fillets, are delivered to trimmers who remove the animals’ fins, skins and other refuse, and then forward the trimmed meat so it can be packaged and shipped to customers. The companies that conduct this business range in size from relatively small, with a weekly production of 20,000 pounds of fish , to very large operations that process 6 million pounds daily, using a vast array of trimmers working in multiple, long production lines. No matter an operation’s size, Marel reports, companies can find it nearly impossible to track who is trimming which fish, how well this is being done and what should be inspected, in order to ensure high quality. As a result, processors have indicated to Marel that their work might proceed more slowly than necessary, and that trimmers might be wasting product by overly cutting the fillets.
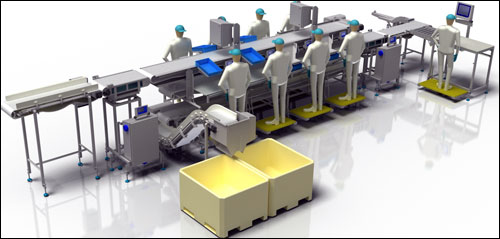
Marel, the largest global supplier of technology for processing fish and meat, is headquartered in Iceland, with offices worldwide and a research-and-development division in Seattle. The company had received requests from fish-processing customers around the world, including some very large operations in Alaska, for a system that would help track work-in-progress, as well as product movements throughout their facilities. Marel already provides customers with its Innova software to manage data related to the receipt, processing and shipping of fish products. In recent years, the firm had also provided some customers with a system that employs passive high-frequency (HF) RFID tags to identify when a particular basket of fish was at a specific location. An HF tag is placed loose in a basket of fish and read by the operator to link that basket with that workstation. However, the company notes, the tags’ short read range have proved problematic.
Approximately eight months ago, Marel’s Seattle R&D division began working on the ProCon Flowline system, which consists of the modular unit of weight scales and fish-trimming and -inspection stations, but also includes at least one Impinj Speedway Revolution four-port reader and antennas at each worker’s station and scale. The system also comes with touchscreens, installed at each station, that display Innova software data regarding the production underway at that site, according to Arnar Olgeirsson, Marel’s service and innovation director.
Workers first fill baskets with fish fillets ready to be trimmed. Each basket has a built-in passive EPC Gen 2 UHF RFID tag, the unique ID number of which is stored in the Innova software. The production manager enters product information, such as the fish’s species, source and supplier. Once placed on the conveyor, the basket is automatically moved to a scale that weighs the fillets and links that weight with the basket’s tag ID.
The basket is then moved to the available fish trimmer, and the antenna at that reader captures its tag ID and forwards that information to the software, which determines the station at which the basket is located. Upon beginning a shift, a worker inputs his or her own employee ID, which the Innova software links to that specific station, so that all baskets of product dwelling at that station will be attributed to that employee.
The worker first dumps the fish out of the basket and then begins the trimming process, returning the trimmed fillets to the same basket and discarding the waste. Once this is finished, the basket is moved to a second scale, where it is again weighed. The fish is expected to weigh less at this point, since waste product has been removed; however, the fish-processing company seeks the highest weight possible for every fish, thereby indicating that no edible meat had been inadvertently trimmed away from the fillet. The second weight is attributed to the station and the employee working there, and he or she can view those details on the touchscreen at that station, indicating the current weight and the amount of weight loss, based on the first scale’s initial measurement. That data is presented to that employee, along with a comparison against the facility-wide average, enabling the worker to determine how well he or she is doing.
The fish processor conducts quality inspections on a limited number of its baskets, in order to ensure that they the fish within are being trimmed properly, and that nothing remains on the fillet that could affect quality, such as a piece of skin or a blood spot. The company can conduct those inspections based on a random selection of one out of every 20 baskets, or it could select those that seem to have a weight change exceeding the norm. An automatic arm on the Flowline unit then pushes the basket to the quality-control inspection station. If the company is singling out one in 20 baskets for inspection, the solution can track which worker prepared each basket before it is selected for inspection, thereby ensuring that operators’ work is screened evenly. The system determines this information by comparing the trimming station’s ID for that basket against the number of inspections already conducted for that particular station during that shift.
When conducting inspections, operators enter the results—such as satisfactory or unsatisfactory—into the system, and the Innova software then displays those results at the station from which the basket originated. That data can also be stored and viewed by management in real time, or at a later date.
In addition, Marel can provide RFID readers at key locations within a facility, to track when fish are first received at the plant, as well as when they are moved into cold storage and when they are shipped. At present, Olgeirsson says, no one is using the new UHF-based ProCon Flowline RFID-enabled system. However, he expects several businesses to begin doing so this year.
The technology is anticipated to increase the yield gain of the fish processing—in other words, a larger percentage of the meat will be retained due to increased employee diligence. Marel predicts the average increase will be about 4 percent. “The biggest financial gain will be in the yield increase,” Olgeirsson explains, though he notes that the technology will also increase operators’ throughput time at a rate of about 35 percent, thus reducing operational costs. The quality of the trimmed filets will also increase, he adds, as workers gain greater ownership over their work.
What’s more, Olgeirsson says, the software offers other potential benefits. In the event of a recall, for instance, a company would be able to trace product—assuming it had been monitored through the shipping process via RFID—back to the operator station where the fish was trimmed. In that way, the firm would be able to better isolate the contaminated fish specific to a single station or worker, and thereby reduce the risk of having to discard all of the plant’s fish from a particular day.