In an unprecedented pilot sponsored by EPCglobal‘s Transportation and Logistics Services Industry Action Group, 37 companies and organizations—including worldwide logistics providers, technology vendors and government agencies—worked together to use RFID to track goods from the Port of Shanghai to the Port of Los Angeles, one of the busiest trade lanes in the world today. The pilot, which concluded in March, showed that RFID could provide end-to-end visibility into the whereabouts of tires, computers, agricultural machinery and other goods shipped from factories in China to distribution centers in the United States.
Key to the pilot’s success were the logistics providers, including DHL, Maersk Line and NYK Line, which stand between the manufacturers and the retailers. It was an achievement that logistics companies could only imagine in 2005, when RFID Journal last wrote in depth about the use of RFID in the logistics industry.
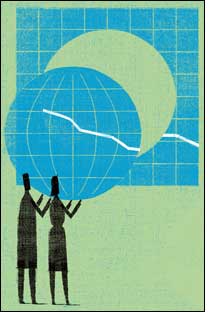
Back then, logistics companies were using RFID internally to track assets, such as shipping containers and freight cars, and they were RFID-tagging goods for manufacturers that had to meet retailer mandates. Logistics companies knew they’d play a significant role in the use of RFID to track goods through the global supply chain, but many challenges stood in the way. In particular, how would logistics companies, which maintain proprietary data systems, share and secure data as goods changed hands from trucking companies to sea or air carriers to third-party logistics companies, which unpack and label goods for shipment to stores?
It was a difficult question, because the answer—EPC (Electronic Product Code) Information Services—was still on the drawing board. EPCIS, which was ratified in April 2007 by EPCglobal, is a standard for sharing EPC-related information among trading partners securely and in real time. The EPCIS databases sit on top of companies’ proprietary systems, without replacing them. Logistics companies can enter into EPCIS only the “events”—departure from a factory, arrival at a port, delivery to a warehouse—they want to share with other trading partners. At the same time, more detailed or sensitive data—names of other customers or location of ships at sea—can be kept private.
“Before there was an in-depth understanding of how this could work, there were some concerns about it,” says Gay Whitney, EPCglobal’s standards director. That began to change in 2006, when EPCglobal established its Transportation and Logistics Services Industry Action Group (TLS IAG) to develop standards for the industry. “They worked together to understand where [RFID] could best be utilized in a standardized way—and in a universal way—to benefit the most participants in the supply chain,” Whitney says.
The ability to use RFID to track international shipments promises to open up new business opportunities for logistics companies and their manufacturing and retail customers, but several challenges still need to be overcome before that can happen. Open-loop deployment in logistics—across networks and with multiple trading partners—will be feasible only when a critical mass of industry players deploys RFID, along with their customers in aerospace, automotive, chemicals, consumer electronics, pharmaceuticals, retail and other sectors.
“In the logistics industry, there are many links in the chain that have to be passed,” says Doug Olson, general manager of systems and process for Schneider Logistics, based in Green Bay, Wis., and a TLS IAG co-chair. Schneider, which has been using GPS technology to track the real-time location of all its trucks and containers since 1983, participated in the pilot by reading RFID tags as its trucks picked up shipments in Los Angeles and delivered them to warehouses.
In addition, “we have to collaborate on standards to make it work,” Olson says. The TLS IAG has developed RFID tag requirements for transportation and logistics. The passive Conveyance Asset Tag (CAT) and the active XCAT version are optimized to perform well with the industry’s often long read ranges and sometimes harsh and/or metallic port environments. But standards work still remains, such as developing hardware and software interfaces.
Meanwhile, logistics companies are deploying RFID in closed-loop situations, where they have control over tagging, reading and environments. They’re using RFID internally and offering value-added services to customers to maintain their competitive edge.
Better Business
The China-U.S. pilot was phase two in a series of EPCglobal TLS IAG pilots that will help develop RFID standards and demonstrate to logistics companies how EPCIS can help them share information about shipments that will change hands among providers during transit. It expanded a phase-one pilot, completed in 2007, that successfully tracked RFID-tagged containers of footwear shipped by sea from ports in Hong Kong to Japan, demonstrating interoperability through multiple trading and service providers. The phase-two pilot included trucks, sea carriers and air cargo as it tracked goods across two continents.
A phase-three pilot, expected to begin later this year, is designed to test how RFID and EPCIS can be used to communicate customs information for shipments of electronic goods from Asia to Europe.
Logistics providers that adopt RFID tracking through the global supply chain could provide their customers with valuable information they could use to make better business decisions and meet government regulations. Say, for instance, a chemicals manufacturer in the United States is looking to buy cheaper supplies. The manufacturer could get a better price from a Chinese supplier, but at present the lower price would be offset by the need to commit more capital to keep additional stock on site because of the long travel time and the lack of information about when the supplies would arrive.
“If I do a more global supply chain, it increases my lead times and forces me to increase inventory stock,” says Paul Schmidt, RFID lead for Accenture. “But if I can have visibility as goods are moving through the global supply chain, I can have greater confidence in that movement and therefore reduce my safety stock.”
The adoption of RFID by logistics providers could also help the chemicals manufacturer meet government requirements for maintaining a chain-of-custody record for regulated or potentially hazardous goods. The U.S. Food and Drug Administration (FDA) is preparing a recommendation for an electronic-pedigree system that would identify products as they move through the supply chain. If the FDA recommends RFID—public comments, which the agency solicited, favored RFID—logistics providers would be integral to documenting the track-and-trace solution to prevent counterfeit drugs from entering the supply chain.
In the future, the data gathered through the reading of RFID-tagged container shipments could help manufacturers better meet consumer demand. Currently, ocean-bound shipments from Asia to European markets often take three or four weeks to arrive. By then, some goods, such as apparel and footwear or consumer electronics, might have become obsolete. Manufacturers tell logistics providers they would like to have more flexibility to ship those goods where demand is still strong, but increasingly rigid customs clearance processes due to security concerns stand in the way. The question is whether the RFID data will satisfy customs regulations in Europe and allow the 11th-hour altering of shipping destinations.
“Because of the complexity of transportation and logistics and the lack of interoperability between logistics providers, it is pretty hard for the shipper or consignee to amend the customs clearance documents,” says Naotaka Ishizawa, RFID project manager at Monohakobi Technology Institute, the R&D branch of Tokyo-based shipping and logistics provider NYK Line, and another co-chair of the TLS IAG. “So now most of the consignees are giving up amending the customs clearing documents.”
Also on the horizon is the use of RFID in conjunction with GPS, cellular or satellite tracking technologies; Schneider and some other companies are already doing this. By providing customers with such real-time visibility, logistics providers would empower them to make business decisions based on the whereabouts of their shipments. “Convergence,” says Michael Liard, research director of RFID and contactless at ABI Research, “is going to be a key message going forward.”
Faster—and Safer—Business
The benefits that logistics providers and their customers can realize from RFID aren’t all in the future. RFID is helping some logistics providers speed through customs, even in the wake of the more stringent requirements established since the terrorist attacks on the United States and in Europe. Governments, concerned about the security of shipping containers, have been enticing manufacturers and logistics providers to use measures—such as RFID-based electronic seals that will report any tampering with a container—to fight smuggling, counterfeiting and theft, and improve security.
The United States, for example, launched the Customs-Trade Partnership Against Terrorism two months after the Sept. 11, 2001, terrorist attacks. Companies that can prove shipments have not been tampered with during transit can receive expedited customs clearance. The program has 8,200 certified partners, comprising manufacturers, importers and logistics providers, including trucking companies, rail and sea carriers, and freight consolidators.
One such manufacturer enjoying faster customs clearance is Western Digital Thailand because the computer components it ships are secured with RFID-based e-seals from Savi Technology at the point of manufacture, and those seals are read using Savi’s proprietary software upon export from Thai ports and import into the United States. Likewise, truck drivers from Mexico and Canada have been assured quicker transit across borders to the United States through the Free and Secure Trade (FAST) program, which issues qualified drivers RFID-enabled identity cards and their trucks RFID-based electronic vehicle registrations.
An ABI Research report released late last year found that the market for cargo tracking and security is expected to grow from $204 million in 2008 to $601 million by 2013. Active RFID was the leading technology used for container tracking and security, although RFID was also sometimes used in conjunction with other technologies, such as GPS, satellite or cellular communications, to provide real-time visibility into shipments, according to Liard. The market would be even larger if governments mandated use of the technology for security or customs purposes. “Short of a mandate,” Liard says, “you’re relying on individual shippers and ports to adopt the technology.”
Accountability in Business
As goods travel around the world via different modes of transportation, logistics providers see business benefits in offering customers RFID-related services and data that can provide better accountability to settle billing disputes and responsibility for spoiled or damaged shipments. For example, RFID could establish which logistics company last had possession of a shipment of flat-panel TVs that went missing.
Logistics providers are also using RFID with sensors to verify that shipments of temperature-sensitive goods—such as pharmaceuticals, life science products and food—were kept in the right conditions during transport. “Say I drop off a shipment of ice cream at Shaw’s, and I know that it didn’t melt during the entire process,” Liard says. “If that ice cream melts within Shaw’s, that’s Shaw’s fault. If Shaw’s receives something that’s not in good condition, then there’s recourse for action.”
Since 2007, DHL has been using sensors to monitor drugs for Swiss pharmaceuticals company Roche Diagnostics (DHL won the 2007 Journal Award for best use of RFID in a service). The temperature monitoring helps Roche determine a product’s freshness. If a drug isn’t kept at the optimal temperature, it may have a shorter life expectancy, but it could be expedited or rerouted to a pharmacy or hospital while it’s still usable and safe for patients. DHL is now piloting the service with other companies in the food and chemicals industries.
Currently, most temperature-sensitive products are monitored during transit with data loggers—battery-operated devices that record temperature variation over time, but whose data typically has to be downloaded upon arrival at a destination. The problem is that the monitoring isn’t in real time. “You’re looking at the information after the fact,” says Tony Hollis, director of innovation and technology management for Exel, a logistics provider throughout North and South America that’s part of Deutsche Post World Net, which has logistics operations in 220 countries and territories around the world. “If you have a shipment of spoiled milk,” he says, “you don’t have any real-time awareness not to deliver this shipment.”
Future Business
Logistics players believe that in the future RFID will be used seamlessly across supply chains and different networks, to enable instant visibility into cargo movements around the world. “The logistics industry is looking for next-generation visibility tools to cope with modern-day supply-chain challenges,” says Mogens Bak, VP of DHL Logistics and a co-chair of the TLS IAG. “Those challenges include capacity restraints in ports, seasonal-product launches, de-stocking, and other lean initiatives.”
The ultimate goal is to provide manufacturers and retailers with the type of on-the-spot visibility across the global supply chain that consumers now enjoy with logistics companies that use proprietary systems to allow package tracking—think of FedEx or UPS. Using EPCIS to track shipments of raw materials or retail goods through intermodal transportation is a step in the right direction. It remains to be seen whether—and how quickly—logistics providers deploy this technology. When RFID tagging moves back to the source of manufacturing and logistics providers realize customers may pay for better information, RFID adoption could become more attractive.
For now, the cost of RFID technology is still a challenge in the logistics trade, where margins can be small and competition fierce. “There is probably a reluctance to invest as long as the low point in price has not been reached,” says Bak. “There is also some way to go on the standards development side….Therefore, I foresee that RFID deployment will remain closed-loop for some years, and once a sufficient mass in these deployments has been achieved, open-loop deployments will become more common and have a much better business case. Also, if such closed-loop deployments are made on the back of global standards, it will be much easier to hook them up once deployments go open-loop.”
Internal Visibility
“When we talk about RFID,” says Gay Whitney, EPCglobal’s standards director, “it’s all about visibility.” And not just in the global supply chain. Logistics companies are adopting RFID solutions internally to track assets or gain efficiencies in warehouses.
Monohakobi Technology Institute, the R&D division of Tokyo-based shipping and logistics provider NYK Line, has several internal RFID asset management and real-time location management applications throughout Asia, Europe and North America. The company is now using 1.5 million RFID tags on assets, such as plastic boxes and shipping containers, to prevent them from getting lost or sitting idle, says Naotaka Ishizawa, RFID project manager at Monohakobi and co-chair of EPCglobal’s Transportation and Logistics Services Industry Action Group. The company also uses RFID in its U.S warehouse and open-air yard to track oceangoing containers so they can be more quickly and easily located and shipped out.
Greek third-party logistics provider Diakinisis is employing RFID tags to track 1,300 pallets per day for a food and beverage supplier at a distribution center the company operates in Athens. The pallets are tagged when they arrive at the DC and are transported to a storage location by forklifts rigged with RFID interrogators and computers. The process eliminates errors regarding product placement on the racks. The pallets also are read as they leave the DC for transport to stores. Because the food often has expiration dates, the logistics provider is able to minimize the number of human errors and associated costs of shipping the wrong products or those that have passed their prime.
The YCH Group, a large logistics provider in Singapore and a bonded warehouse for controlled items such as alcohol and cigarettes, is using RFID to operate its facilities more efficiently. Since the company started RFID-tagging goods in its warehouse, it has seen improvements of up to 40 percent in turnaround times between order receipt and order shipment, according to Chris Warner, senior marketing manager for Motorola, one of YCH’s technology suppliers. “They know where all the components reside in the warehouse and the best pull routes,” he says.
Closing the Loop, Opening Up Benefits
One of the biggest problems facing pharmaceutical and medical-device suppliers to health-care facilities throughout the Asia-Pacific region is replenishing stocks before they are depleted. Manufacturers often have to send staff to hospitals and medical centers, which may be in far-flung locations, to inventory stock and reorder supplies.
DHL, a global logistics provider that warehouses and repackages medical devices and pharmaceuticals at its Asia Healthcare Hub in Singapore, is taking steps to solve the problem. In May, DHL, along with technology provider Hewlett-Packard, started testing an RFID system in development since 2006 that automates both the tracking and ordering of medical devices and pharmaceuticals.
The RFID service is a natural business opportunity for DHL. “We tend to receive a lot of products here at the distribution hub, and we need to unpack and redistribute them to various destinations or consumption points in Asia,” says Michael Lim Hong Hai, VP of business development for DHL.
For the pilot, DHL hand-tags the devices and medicines as shipments from manufacturers are divided for redistribution. The Singapore hospitals participating in the pilot are equipped with smart shelves that can identify tagged items in real time. When supplies get low, the networked system sends automatic alerts to the DHL Asia Healthcare Hub, which, in turn, sends orders for new stock to manufacturers.
“It’s in effect a win-win-win situation,” says Tim Wilkinson, HP’s manager for RFID and supply chain for Asia Pacific. “For the hospitals, they’re obviously not going to run out of stock of items, because this is being monitored on a real-time basis, and new supplies are ordered before they run out. At the same time, DHL provides a very efficient service to its customers. The drug manufacturers or medical-device manufacturers ensure that they have the right stocks in the right place at the right time.”
DHL says the system works, and it’s now in negotiations with hospitals in Singapore to implement the RFID smart-shelf solution. The company hopes that hospitals throughout the 10-country region served by its Asia Healthcare Hub will also be interested. “Other industries with high-value items, such as consumer electronics, might also benefit from a similar RFID solution,” says Alfred Goh, VP of Asia-Pacific supply-chain logistics for DHL.
Editor’s note: To keep abreast of the latest news on RFID in the logistics industry—and to read case studies of early adopters—go to www.rfidjournal.com/logistics or click on Transport/Logistics on the top menu bar of the RFID Journal Web site.