A Finnish forwarder, Assistor Oy, is using passive ultrahigh-frequency (UHF) RFID tags to track new imported cars from the time the company receives them at port until it delivers the vehicles to their next handler. With 25,000 EPC Gen 2 tags presently in deployment, the project is Finland’s largest application of RFID in business or production processes, according to Digia, the firm that supplied and implemented the system for Assistor.
Assistor operates vehicle terminals in the Finnish ports of Hanko and Paldiski, and also maintains a terminal in Espoo for handling parts shipments. In 2007, the company forwarded 266,000 new cars for 20 manufacturers, including BMW, Chrysler and Toyota. This year, it expects to handle more than 300,000 cars.
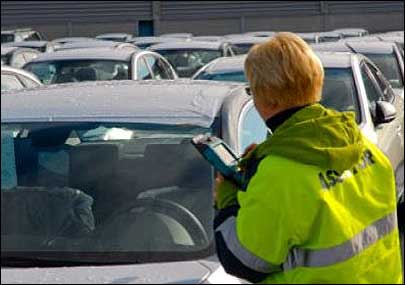
Last year, Assistor decided to update its IT system. Digia, a Helsinki-based provider of information and communications technology, recommended its RFID-compatible Digia Enterprise ERP software and system, which Assistor tested and rolled out in December 2007. “With the RFID system, we have been able to handle more cars with the same number of staff,” says Tom Suvanto, Assistor’s deputy managing director, though he declines to provide specific figures.
Before implementing RFID, the company relied on a bar-code and paper-based tracking system. When a car was received, workers scanned a bar-coded label on the vehicle’s front or back windshield, thereby collecting its unique 17-digit vehicle identification number (VIN). Some carmakers don’t use bar codes, however, and the bar codes were often unreadable. If a bar code could not be scanned, employees entered the VIN manually. The VIN was then used to identify the car on all printed work orders, such as instructions for a worker to take the vehicle to the car wash or holding area.
With RFID, workers can now identify cars more quickly. What’s more, they experience fewer mix-ups regarding which cars go where, and the system is essentially paperless. When Assistor receives a car at port, an employee utilizes a Nordic ID handheld computer to scan its bar-coded VIN. (This is the only bar-code scan necessary, unless an RFID tag is damaged or missing. In such a case, the bar code acts as a backup.) Then, using the same Nordic ID handheld device—which includes an RFID interrogator—a worker reads an RFID tag.
The tag, manufactured by UPM Raflatac and encased in plastic, is hung on the car’s rearview mirror. Assistor opted for this style of housing because manufacturers often forbid handlers from attaching anything to the outside of a car. The tag comes with a unique six-digit number encoded to its chip and also imprinted on its housing, in case a worker needs to identify that tag without using an RFID interrogator.
The back-end system links a car’s VIN with its tag’s ID number. At present, Assistor employs 100 readers in the application. Workers read a tag anytime a car must be moved from one point to another while Assistor is holding the vehicle; the average number of interrogations is 10. The final reading occurs when cars are handed over to the next operator, such as a forwarder, after which the connection between the car’s VIN and the RFID tag number is deleted, enabling the tag to be reused for another vehicle.
Assistor is very happy with the application, Suvanto says, and has experienced no problems operating it since initial problems were worked out. When the company began using the tags and readers, some workers accidentally read the wrong tags because they were carrying multiple tags around with them. “We were not aware how easy it is to read the RFID tags compared to the bar code,” he states. “Now we all know how this works.”
In addition to saving time, Suvanto says, the firm also gained an unexpected benefit: During Finland’s heavy winters, workers had to scrape snow off cars before they could scan each vehicle’s bar code and complete work orders. Now, workers just need to move the reader close to the car to know if they are handling the correct vehicle.
In the future, Suvanto says he would like for his company to receive cars already tagged. “I think this would be a good solution from the factory to the dealer,” he notes. Later this year, Assistor hopes to add 5,000 to 10,000 additional tags to the number it currently has in circulation. During the next few years, it may add diverse stationery read points at key junctures, such as at carwash entrances or at the loading dock, to provide an even more precise overview of the location of vehicles.