Mutual Materials, a Pacific Northwest manufacturer and hauler of stones, bricks and other masonry products used for landscaping and construction purposes, is monitoring the locations and conditions of its vehicles via an RFID-based solution provided by electronic fleet-management technology company Zonar. The solution consists of passive low-frequency (LF) RFID tags on vehicles, trailers and moffets (truck-mounted forklifts), as well as Zonar’s Android-based tablets with built-in RFID readers that capture tag IDs and enable users to input vehicle inspection data or report problems. The collected data is then forwarded to Zonar’s hosted server via a cellular connection.
Mutual Materials is a family-run operation with customers throughout the Northwest United States, as well as in British Columbia and Japan. The company’s 42 trucks, along with one leased truck, deliver 671,000 tons of material annually and complete 43,000 deliveries. The relatively small vehicle fleet is operated by approximately 90 drivers, in consecutive shifts, to ensure that freight is moving a maximum amount of time. In addition, during its off-season (winter), the firm hauls roofing and other material for a separate set of customers.
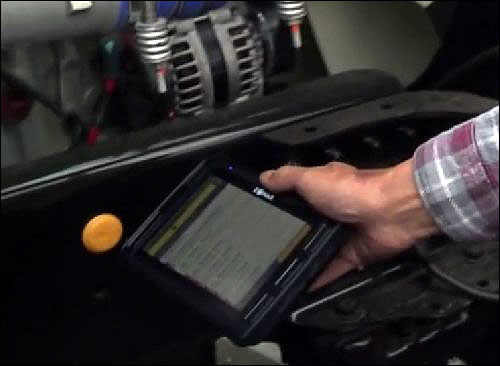
Because the trucks cover a wide geographic area with multiple drivers (a truck, during a single month, may typically be operated by about 20 drivers), tracking information regarding each vehicle, including its condition and location, can be a monumental task. Complicating matters further, the company maintains 12 manufacturing sites, 16 local branches and three distribution facilities. Until 2005, each of the company’s drivers filled out paper forms, stored on the truck, in order to track the number of hours they worked, as well as vehicle inspections and any problems regarding the truck. At the end of the week, each driver sent this paperwork to the company’s office in Kent, Wash., to be input into the system.
If a vehicle experienced a problem requiring urgent attention, says Tim Johnson, the company’s fleet manager, a separate form had to be filled out as well. This form was immediately sent to the maintenance staff, which led to duplicate efforts.
The company acquired a Qualcomm onboard electronic log system to allow drivers to use a keypad on the onboard device to input their ID number and create a record of their driving hours with that vehicle. The firm also installed Oracle Transportation Management (OTM) software in 2012, which is used in the offices, to monitor the dispatching of vehicles and predicted deliveries. Information stored in the OTM software could be shared with customers.
However, the onboard electronic and OTM systems were not integrated, so drivers were still required to manually report the inspections and truck-related problems they found. By using an onboard system integrated with the OTM, Johnson explains, a driver could relay information in real time to Mutual Materials, which could then communicate shipment location and delivery information to its customers. In addition, by integrating data from the truck and driver to the OTM, the firm could reroute drivers based on live updates—such as a behind-schedule or ahead-of-schedule status.
Consequently, Mutual Materials replaced the Qualcomm onboard system with an Android-based solution from Zonar. The new system, which was taken live last month, consists of a Zonar 2020 tablet and an app that will share data with the OTM software. That integration with the OTM software is planned for completion by April 2015.
The Zonar 2020 tablet contains an LF RFID reader, a GPS unit, a camera and cellular functionality, and is docked on a vehicle’s dashboard. About seven button-sized passive 125 kHz RFID tags, known as Zone Tags, are affixed to each vehicle, each representing a specific inspection area—such as the rear tires. Approximately four tags are attached to every trailer, and two more to each moffett.
Upon beginning his shift, a driver proceeds to the tablet and uses its touchscreen to manually enter his user ID number and password. The system also allows drivers to read an RFID-based ID card, though Johnson says the company opted against using RFID ID cards, so that there would be one less thing for the drivers to potentially forget.
By entering his ID and password, the driver creates a record of when he began his shift. He can then proceed to each Zone Tag, tap his tablet against it and follow prompts indicating the results of his visual inspection. The driver can utilize the camera to take pictures of any problems, such as a flat tire, an air leak or a malfunctioning marker light. Any item that would make equipment illegal to operate on public roads according to U.S. Department of Transportation standards must be tracked, explains Mike Jones, Mutual Materials’ director of distribution and branch operations. Upon completing his inspection, the driver returns the tablet to the dashboard dock, and the device then transmits the inspection data via a cellular connection, along with the GPS data, thereby indicating where the vehicle and driver are located.
The tablet, via the docking station, is connected to the vehicle’s engine and also collects function data, such as temperature levels or any operational problems. All data is forwarded via the app to Zonar’s hosted server, which distributes the information to Mutual Materials’ maintenance staff as needed. For example, the Oracle system can automatically route data regarding engine trouble to Mutual Materials’ maintenance staff, as well as to the company’s third-party maintenance provider.
When a user finishes his shift, he next inspects another vehicle, trailer and moffett, by reading the tags and entering the necessary information.
Jones says he expects the Zonar system to reduce dispatch and driver labor, and to increase efficiency. “The moment they dock the 2020, notification is sent to dispatch, our third-party maintenance shop and all our repair facilities, so we are all aware of the problem immediately,” he states. “This helps speed up the repair time, and the record-keeping is visible all at the same time before, during and after the repair.”
To date, with a combination of the Zonar solution and the Oracle software, the company has reduced its number of dispatchers from eight to five, since it is much easier to determine each vehicle’s location, and who is operating it. Drivers can be assured that they have updated information regarding their vehicles’ functionality, since they can view it on the screen when they pull up records associated with a particular tag ID whenever they read a tag. Moreover, says DJ Britton, Mutual Materials’ dispatch manager, they can be assured that problem reports are received immediately, and are thereby resolved by the appropriate maintenance staff.
By April of next year, Johnson says he expects Mutual Materials’ Zonar system to provide some features for customers as well. For instance, Zonar’s EVIR system comes with an application programming interface (API) that can be utilized by third-party apps, enabling a customer to use his or her mobile phone or tablet to receive data about the exact location of a vehicle headed to their work site. In the future, he notes, the technology could also allow drivers to update a shipment’s status as delivered as soon as they unload the freight.
“To stay ahead of the competition,” Johnson reports, “we try to offer our customers the latest technology and continue looking ahead.”
Zonar has offered an RFID-based electronic vehicle inspection solution since 2001, says Andrew Johnson, Zonar’s VP of marketing and sales support, to reduce the need for paper-based inspection systems. The company provided software, tags and a handheld RFID reader. The 2020 tablet—the company’s latest product—enables users to employ an app to view and manage the collected read data. The technology is also employed for school bus fleet management and, in some cases, the tracking of children entering or exiting school buses.
Zonar also provides its system for inspection tracking to Goodfellow Bros., a general contractor based in Wenatchee, Wash. Goodfellow, which operates a fleet of 1,200 vehicles and earth-moving equipment, added RFID tags to its crushing equipment so that employees could scan the tags using Zonar handheld readers or 2020 tablets, and then input the amount of fuel they put into the machines, along with the number of hours the machines have run. By tracking these details, the company is better able to manage the amount of fuel being used, and to potentially lower emissions by identifying when vehicles are running excessively. Goodfellow has also placed tags on vehicles and equipment used during construction projects, to automate the inspection process by enabling drivers to read a specific tag and input observations and details regarding that part of the vehicle.