RFID Journal LIVE! 2023 will feature end-user companies discussing RFID’s use in construction, industrial and other applications, as well as exhibitors offering tagging solutions for those sectors. To learn more, visit the event’s website.
- Starting with Tool Management
- Heavy Asset Tracking in Construction
- Building on Saulsbury’s Tool-Tracking Success
Several construction companies have begun employing a software-based solution to track heavy equipment being used on worksites. The technology enables such businesses to gain wireless and real-time access to data indicating where equipment is located, when it is being operated or was last maintained, and if the individual operating the machinery is authorized to do so.
ToolWatch, a Colorado-based construction operations solutions provider, commercially released its Heavy Equipment Asset Management Solution in January 2023 to enable companies to more effectively manage their largest and highest-value assets, which can be used with GPS and cellular-based data. The new heavy equipment offering is an expansion on ToolWatch’s existing platform that has been allowing companies to manage tools and consumables for years, according to Troy Suttle, ToolWatch’s VP of marketing.
Companies that use the latest version of its solution van integrate data from hardware such as Geotab‘s GPS trackers installed on heavy equipment, while ToolWatch continues to offer small equipment management capability, traditionally with barcodes and more recently Bluetooth Low Energy (BLE) and RFID. Although the heavy asset-management system is being announced now, ToolWatch already offered the earliest iteration of the technology for its existing customer Saulsbury Industries, which now can track even large, high-value items through each project automatically. Saulsbury Industries partnered with ToolWatch to develop the heavy equipment management offering.
Starting with Tool Management
ToolWatch is a solution provider for the construction industry, including general and specialty contractors. The business was founded three decades ago by an electrical contractor who could not find off-the-shelf tool-tracking software. The resultant solutions company built a software system for electrician tools, and then for other sectors in the construction industry as well. That platform has since grown beyond basic equipment tracking, the company reports, to a wider variety of functions around cost accounting.
Companies can employ the software to charge customers for the amount of time that equipment was used on a site. The collected data can then be integrated with a company’s enterprise resource planning (ERP) and accounting systems. Throughout the years, the software firm has been making improvements and adding more offerings to its platform related to support for asset maintenance, tracking utilization and operator certification management.
For example, if a piece of equipment requires workers to have specific certification before being used, the system can monitor the certification of every new employee or operator who might utilize that equipment. Before assigning a worker to a particular piece of equipment, a manager would open the ToolWatch software on a tablet or smartphone, then input that operator’s information. They could thus be alerted to any potential problems before authorizing that operator to use a specific vehicle or tool.
Heavy Asset Tracking in Construction
Recently, some construction companies have indicated they wanted to use ToolWatch’s solution to manage their heavy assets. By capturing real-time data from bulldozers, cranes or other high-value machinery—which is often leased equipment—they wanted to track the return on investment (ROI) for each piece of equipment on a monthly basis. Additionally, the businesses wanted to know for which job each piece of equipment was being charged, as well as and how to accurately bill for the equipment’s use.
Heavy commercial equipment comes with strict service requirements. “ToolWatch’s management system has been designed to help avoid unplanned maintenance,” Suttle explains, “by keeping machines on track for service.” Improved service can expand the equipment’s lifecycle, further raising its ROI.
Some of the data captured by the device includes utilization details measured onsite, enabling companies to track not only the equipment’s location but also the number of hours the machinery operates. Suttle says users can “make sure that they know either how much to charge their jobs, or just in general how much value they’re getting out of the asset, versus how much they’re paying for it each month.” All of that information shows up in ToolWatch’s software, where it can be interpreted and managed for reporting and analysis purposes.
The system comes with a job cost and billing module for heavy equipment. “We streamline the process of getting the data from the utilization of the asset into the accounting and ERP system,” Suttle says. The technology, he notes, is intended to help users understand how often equipment is operating, as well as when it might require maintenance, and to ultimately extend the equipment’s productive lifespan.
To accomplish this, ToolWatch offers a service and calibration module that allows users to import their maintenance schedule for a particular asset, then receive automated notifications to create work orders to make sure maintenance is performed at the right time. For contractors, Suttle says, “The heavy equipment are their most expensive assets. The fact that they want to manage those really proactively makes a lot of sense.”
Building on Saulsbury’s Tool-Tracking Success
Saulsbury Industries has been using ToolWatch’s solution for years, tracking tangible assets ranging from hand tools and grinders to trucks, trailers and tool vans. The company, located in Odessa, Texas, is a full-service engineering, procurement and construction firm that serves the energy and industrial sectors. In recent years, the business has experienced growth, with a large number of assets needing to be managed at numerous sites throughout Texas, Oklahoma, New Mexico and North Dakota.
Traditionally, Saulsbury Industries managed assets manually, using pen and paper on clipboards. To better manage all of its assets, the company adopted the ToolWatch software, which is being used with its existing Spectrum resource-management and planning platforms. Next, it expanded its use of the technology beyond tracking tools to heavy equipment, with Geotab devices integrated into its vehicles.
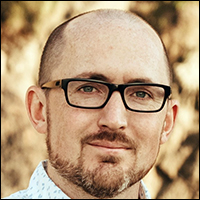
Troy Suttle
With the technology, superintendents or project managers can acquire a list of tools, equipment and materials needed for each project. They can use the software to create pick tickets, then track the pulling of tools from shelves for the project and monitor fleet information used in the same software platform. The software also tracks costs and billing by automating invoices from the Spectrum software.
At the end of the project, Salisbury’s supervisors employ the ToolWatch software to identify the status and location of all assets still assigned to the project, thereby enabling them to round up those assets before the project ends. At present, ToolWatch powers the company’s entire asset operations, from managing the inventory of small equipment and tools to integrating GPS data from its vehicles and heavy equipment.
ToolWatch is marketing the heavy equipment solution to specialty companies such as utility, electrical and civil contractors. Businesses already using the heavy equipment management system include those working in oil and gas, as well as in other energy sectors. The key value points consist of five benefits, the company says: identifying location, utilization, maintenance, operator certification management, and job cost and billing. For both small tools and heavy equipment offerings, ToolWatch says it can provide a holistic construction asset-management solution.
Key Takeaways
- ToolWatch has been providing heavy asset management functionality to contractors or industrial companies for several years.
- Now, the company has commercialized the solution for all its existing and new customers, to help them track and manage equipment ranging from cranes to bulldozers and vans.