Zebra Technologies has put its own real-time location system (RTLS) technology to work at two of its warehouses—one in Vernon Hills, Ill., and a second in Heerenveen, the Netherlands. The solution saves time employees previously spent locating the proper place for loads of picked goods (approximately three minutes per load), estimates Gary Meekma, Zebra’s senior manager of warehouse operations, while also reducing the amount of space required to stage each load by about 40 percent.
Zebra Technologies employs an Oracle warehouse-management system (WMS), along with Zebra’s own ultra-wideband (UWB) Dart RFID sensors (readers) and tags. By reducing the amount of time workers spend searching for the proper location to gather together goods within the warehouse’s staging area, the company reports that it saves 451 man-hours per month.
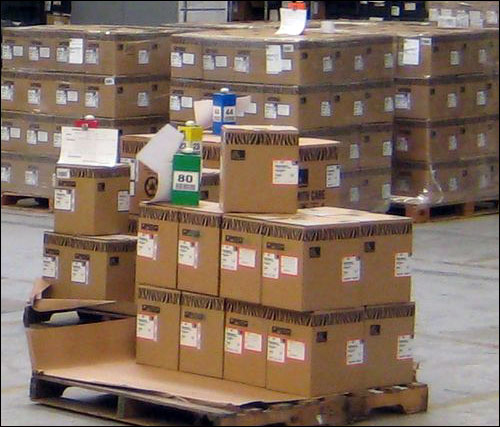
Zebra also utilized its new software tool, known as System Builder, to help it design the warehouse’s RTLS deployment, by identifying the best placement of Zebra Dart UWB devices for the purpose of tracking assets.
The warehouse’s new tracking system consists of Oracle software integrated with Zebra Technologies’ software for managing the locations of orders, in addition to variously colored plastic traffic cones with built-in Dart tags for identifying an order’s location, and Motorola Solutions‘ Symbol handheld computers with bar-code scanners that display location and order data. The handhelds also enable a user to scan a product’s bar code as it is moved to the staging area. Six UWB Dart readers installed around the staging area identify the locations of the tagged cones, and forward that location data to the Oracle system via Zebra’s software.
Zebra’s Vernon Hills warehouse consists of four separate pods, created through multiple expansions to accommodate the company’s growth. After the firm reconfigures its printers and related supplies according to customers’ needs, they are placed in the warehouse, within the same building, before being packed to fill orders and then being sent to customers via truck. Until February 2012, the staff used paper-based picking orders and moved throughout all four pods, manually assembling items for an order. Those items were taken by forklift to the 10,000-square-foot staging area where orders were built. The worker who packed the order then proceeded to the warehouse for another load until that order was filled. However, the company reports, the system proved time-consuming for the warehouse staff.
In February, Zebra Technologies installed an Oracle WMS at its North American locations (its other facilities went live with Oracle in January 2011), in order to eliminate the need for paper, and to help the staff locate the goods picked for orders. Each warehouse worker carries a Symbol handheld bar-code scanner that lists the locations of items to be picked, as well as the approximate spot at which each product should be placed within the staging area to fill an order. A worker scans the bar code on the each item while picking it, and that scan indicates what was being pulled for the order in the WMS residing on Zebra’s back-end system.
Thanks to this system, Zebra reports, it is no longer necessary for a single staff member to work on one order in order to track what had been picked. Now, as many as five employees could work simultaneously to fill the same order, simply by following directions displayed on a Symbol scanner, based on Oracle data.
However, Meekma says, although this system saved a few minutes for each picking load, and also enabled multiple individuals to work on an order simultaneously, this new process could create confusion in the staging area without an RTLS solution in place. To make efficient use of space, the staging area is designed for flexible staging. That means staff members create a lane for loading a particular order, based on the order’s size. A smaller order does not require as much space as a larger one. When more than one person is working on a single order, however, only the employee who makes the first drop-off knows the exact location of the staging area for that particular order.
This is where Zebra’s UWB solution comes in. The company installed UWB tags in the tops of 100 plastic traffic cones used to identify the lanes. The cones come in one of five colors, such as yellow or red, with 20 cones for each color. By providing color coding, the staff can more easily identify the correct lane by searching for the color (such as red) of the cone associated with that specific order. The Zebra Dart RTLS UWT-1100-A-00AB tag on the top of each cone transmits a unique ID number every four seconds, via a UWB 500 MHz to 10.6 GHz signal complying with the IEEE 802.15.4f standard. Six sensors (readers) installed on the ceiling receive that signal and then forward the read data to Zebra’s Visibility Server Software (VSS). The software uses triangulation to identify each cone’s location, explains Adebayo Onigbanjo, Zebra Technologies’ senior product marketing manager. It then integrates that information into the Oracle WMS, where a cone’s unique ID is linked to that cone’s color.
Upon dropping off the first items for a particular order, a worker places those products on a pallet within the staging area, and then takes a cone and places it on one of the boxes in that order. Next, the employee uses the Symbol device to scan the bar-code number printed on the box, as well as a bar-code number printed on the cone, thus linking the order with that specific cone and color.
The Symbol handheld displays additional items for that order for the staff to pick. Once the load is moved to the staging area for drop-off, the handheld also provides the color of the cone associated with that order, along with its location, based on reader data, which is then displayed as a location number that is also stenciled on the floor. Workers use the stenciled numbers to pinpoint the location of the staging area assigned to a particular order.
When a worker’s handheld displays an item to be picked, that individual retrieves the product and inputs or scans its bar-coded number, confirming that the load has been picked up. The employee is then directed to the stenciled location number and colored cone where the item should be dropped off. After placing the object next to those already in the staging lane designated for that order, the staff member scans the bar-code number printed on the cone. If there is a mistake, the worker will see an alert on the scanner’s screen, indicating that the goods are being placed in the incorrect staging lane. Once the order is completely assembled within the staging area, the cone is temporarily removed while the pallet is covered in stretch wrap. The cone is then placed back on top of the stretch-wrapped pallet, in order to help the staff identify the order and load it onto the appropriate truck, where the cone is then removed and returned to the staging area.
Without an RTLS solution, the company reports, the process of locating a shipment in the staging area could take the staff from one to eight minutes—approximately three minutes on average. Since the warehouse averages 1,000 drops daily, Meekma says, that time adds up quickly, though the RTLS cuts about a minute off each drop time.
Based on the Zebra technology’s cost, Meekma estimates that had the system been purchased, the warehouse would have seen a return on investment (ROI) in about six months, thanks to a reduction in man-hours. Until July of this year, the RTLS data was displayed on a monitor within the staging area, he says. Now that the RTLS solution has been integrated with the Oracle software, however, the facility has been able to display that data on the Symbol scanners, thereby saving several more seconds per load drop, by sparing the staff from having to go to the monitor in order to search for each order.
To design the system, Onigbanjo says, Zebra’s installation team used the company’s new System Builder tool. First, Meekma provided details regarding how the staging area was configured, as well as the type of data he required. “When we got input from Gary, we could go into the [System Builder] tool,” Onigbanjo says, and begin entering additional details as well—such as where metal racks or other obstacles could affect the RFID tags’ signal strength—and began mapping out the system. In so doing, he explains, the development of the system for this location was much faster, since it was not necessary to move sensor antennas around through a process of trial and error to create the proper read environment. In addition, Zebra’s customers can purchase the System Builder software for their own deployments.
With the RTLS solution, Onigbanjo says, the tagged cones’ locations can be pinpointed within about a foot. The system was so successful, Meekma adds, that it was also installed at Zebra’s warehouse in the Netherlands this past June.