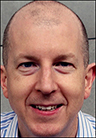
Modern manufacturers are familiar with a variety of data-driven optimization tools for improving quality and eliminating waste in manufacturing processes. Until recently, though, these methodologies have not been mirrored in the supply chain world. In large part, this is because a lack of data has made it difficult to translate those data-driven strategies into supply chain management. But these days, managers are gaining access to new data sources, making it possible for companies to bring a new level of optimization to the supply chain.
Specifically, companies are using new IoT tools to track shipments across a global supply chain and attain real-time data for key metrics, such as delays and damage rates, for each leg of a shipment’s journey. Armed with these new, comprehensive datasets, managers can adapt many of the most impactful data-driven manufacturing strategies to supply chain.
Statistical Process Control
One of the most well-known tools for quality control and optimization in manufacturing is statistical process control (SPC). The term refers to the practice of measuring and controlling variation within a process, and is often achieved through the use of a control chart: a graph in which data for a given variable is plotted over time and compared to the average, upper limit and lower limit of historical data. A control chart highlights outliers and allows for immediate investigation as soon as data comes in outside of acceptable bounds.
Manufacturers use control charts to optimize assembly steps, such as drilling a hole to a precise diameter or cutting a part to a specific length, but supply chains also have critical dimensions that benefit from optimization. These variables include trip durations, mishandling rates, temperature excursion rates and so on. With real-time data regarding shipment damages or delays, managers can apply SPC analysis to the supply chain and get a heads-up as soon as a variable goes out of control.
For example, by comparing durations for a given route against past data, a supply chain manager can determine that a certain leg of a given route is experiencing excessive delays. Similarly, a comparison of the frequency of shock events a shipment experiences can highlight certain routes or locations as particularly prone to damages. Without access to data, this sort of analysis is difficult to impossible. Even if total trip duration is known, real-time visibility is necessary to determine exactly when and where along a route an issue is taking place. Internet of Things (IoT) tools give managers the data they need to isolate important variables and be notified as soon as an excursion occurs.
Lean and Six Sigma
These new tools are also helping managers to integrate data-driven Lean and Six Sigma methodologies into the supply chain. Lean refers to the concept of systematically removing waste from a process, while Six Sigma is a set of tools and methodologies for improving quality and reducing risk. IoT tools have made it possible to bring a new level of data-driven analysis to bear, enabling the IoT-powered supply chain to reach new levels of Lean and Six Sigma success.
Visibility into every link of the chain, in combination with the SPC analysis described above, helps companies develop a baseline for normal deviations in shipment time and inventory at every point. This enables managers to implement targeted increases in safety stock at critical vulnerability points, while removing excess safety stock in other parts of the chain. In addition, greater visibility into the real-time location and condition of goods gives companies the ability to respond to problems with agility, preemptively rerouting and calling on backup suppliers when demand surges occur. Instead of relying on large amounts of safety stock, companies can use the data from an IoT tracking system to run lean, distributing inventory efficiently without sacrificing risk tolerances.
That brings us to the concept of Six Sigma. Six Sigma is all about leveraging data to reduce risk and improve quality within a given process. With real-time data for all shipments, a manager can optimize shipping processes to minimize the rate of delays or damages per million products shipped. This data makes it possible to set up success metrics and ensure quality along every step of the supply chain.
The implications of the data-driven supply chain are huge. New IoT data sources are allowing companies to apply tried-and-true methodologies, from the manufacturing world to supply chain management. Ultimately, this data-driven approach is helping companies reduce waste, lower costs and, ultimately, increase bottom-line revenues.
Rob Stevens is the co-founder and chief revenue officer at Tive, a provider of sensor-driven tracking solutions designed to deliver full visibility into products as they move through the supply chain.