Industry 4.0 is at its greatest inflection point. Digital technologies like artificial intelligence (AI), augmented reality (AR), machine learning (ML), big data and robotics are disrupting almost every layer of the enterprise to make it more evolved, customer-friendly and efficient. AI-driven predictive maintenance is already saving huge operating costs for manufacturers. Interconnected products and ecosystems and the process of automation lie at the heart of a company’s success.
Most industries and businesses have already recognized this trend and are preparing themselves for digitization—as is reflected in the significant rise in information and communication technology (ICT) spending taking place. According to IDC, ICT spending will jump from $4.3 trillion in 2016 to $5.6 trillion by 2021. That growth equates to a 6 percent compound annual growth rate. Companies that are yet to make a roadmap in digitalization run the risk of becoming completely irrelevant or falling way behind competitors.
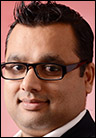
Why Go Digital?
According to Gartner, companies risk losing a minimum of 25 percent of their business due to a weak digital business model. Technologies like AI, ML and robotics help companies to redefine business models—enhancing and creating value, increasing both quality and efficiency, and digitally remastering the way to put great minds at work.
1. Predictive Maintenance: Unplanned machine downtimes and failures are chronic problems that incur heavy costs for manufacturing companies across the world. Sending technicians to repair a machine after it stops working means loss of production, critical man hours and precious manufacturing money. However, the proliferation of Industrial Internet of Things (IIoT) systems is helping manufacturers to transform economies and achieve a new level of competitiveness.
By aggregating real-time data from sensors installed on the machinery and equipment, manufacturers can track current machine operational status and also receive alerts if there is a possibility of any failures or unplanned downtime. All these factors can contribute to enhancing operational efficiencies and increasing revenues.
2. Enhanced Customer Service: The IoT, coupled with AR, is helping companies to set new benchmarks in customer service. Companies that have their products and equipment distributed across different locations often face a challenge with after-sales service or troubleshooting. Usually, these companies have field-service executives that visit different locations for troubleshooting or servicing the equipment.
Often, these field executives or technicians must spend a great amount of time going back and forth with back-office experts for more complex problems, or refer to technical guides or tedious repair manuals. The IoT and AR can help field-service executives in many ways. Through the use of wearables such as smart glasses, technicians can work hands-free and even work remotely with back-office experts.
Field technicians can also share real-time photos and videos through shared visuals and even create a handholding mechanism with back-office personnel, thereby making troubleshooting quick and seamless. Faster and more efficient customer service not only saves huge costs for the company, but also ensures greater customer satisfaction and higher customer retention—which, in turn, result in higher profits.
3. Process Automation: Arguably, the most controversial of the loT, robot-driven process automation has created controversy, surrounding the fears that it will eliminate jobs. The biggest misunderstanding around this is that process automation means deploying large armies of robots that would completely replace human workers and eventually take over the world. However, this could not be further from the truth.
The future of process automation would include robots working side by side with the human workforce. Companies can use automation for mundane or routine tasks like filling forms or using robots as labor for unloading goods, sorting and stacking into pallets that can be stored. A research study shows that about 80 percent of current warehouses are manually operated with almost no supporting automation. Automating these processes can free human workers for more high-end and complex tasks, allowing companies to maximize productivity and enhance outcomes.
4. Lowering Operational Costs: One of the biggest factors driving operating costs for companies is to acquire and retain enough high-quality or skilled employees. For the first time in history, future populations will be smaller than past generations in the mature markets. A recent study by BCG shows that during the next 15 years, Germany alone could see a labor deficit of up to 10 million workers. For companies to stay afloat, they would need to spend more to get good workers to maintain or increase productivity. Automation would then be the best bet.
Technologies like chatbots and virtual digital assistants (VDAs) can be the future of cost-effective customer service. Chatbots can be the perfect tool for 24-7 customer service, and can provide quick resolutions for customer complaints, troubleshooting or tracking order status. A cheaper and low-maintenance alternative, chatbots can also liberate hapless customers from the painfully long and frustrating automated call system. Chatbots can also help in automating boring tasks like filing tax returns and expense reports, and in staying on top of ledger reports.
5. Digital Natives: Today’s children are tomorrow’s customers, and for millennials, mobile phones, tablets and other digital devices are the most obvious choice. Thus, for companies to stay visible and relevant to these customers of tomorrow, it is important to have a digital framework.
U.S. telecommunications and information technology solutions giant CenturyLink revealed in a study that 57 percent of the 613 companies surveyed in the Asia-Pacific region, including China, Japan, Singapore and Hong Kong, already have a formal roadmap to digitalize their business. Of them, 63 percent plan to complete their digital transformations during the next three to six years. Thus, the question is not when, but how soon a company should start digitalizing. And the answer is: it may already be too late.
An entrepreneur and information technology leader, Ankush Tiwari is responsible for building Mobiliya‘s global engineering teams, engineering delivery responsibilities and engineering strategy and direction. Ankush is an Advisory Board member for Venture Catalysts, a seed investment and innovation platform. A renowned name in the mobile engineering industry and a recognized influencer worldwide in telecommunication and mobile software, he is a trusted advisor to senior executives in Fortune 100 companies. Ankush shares insights regularly at conference keynotes, and has been published and quoted in numerous renowned publications. He has amassed more than a decade of experience in software for mobility, having served as the lead architect for Azingo (acquired by Motorola), where he led the Web 2.0 application framework and middleware architecture for the open-source Linux platform and the open-source browser for embedded systems.