A stone’s throw away from the idyllic resort town of Vevey is the headquarters of one of the largest RFID transponder producers in the world: Sokymat. Founded in 1964 in the French part of Switzerland, Sokymat began as a maker of coils and later micro coils for the Swiss watch and clock industry. The original owners of the company were from Milan, Italy.
In 1977, Ake Gustafson, a Swedish businessman and inventor, bought the company, which continued to manufacture coils, micro coils and the machines that produce them. But in the late ’80s, as Sokymat faced stiff competition from Asian manufacturers, the company’s business shifted from coils to transponders for animal identification. Gustafson invented the “direct bonding” technology, which automated the assembly of a transponder by soldering the copper coil of the RFID antenna directly onto the pads of the silicon chip. This enabled the company, which filed the patent for the technology in 1991, to mass-produce cost-efficient transponders.
|
Sokymat was acquired in 2003 by Assa Abloy, the world’s leading manufacturer and supplier of locking solutions. The company is now part of Assa Abloy’s Identification Technology Group, which focuses on current and emerging identification solutions within the RFID and smart card markets.
Today, Sokymat produces roughly 75 million low-, high- and ultra-high frequency RFID transponders per year. It supplies manufacturers, vendors and systems integrators with RFID tags, cards and labels for use in logistics, access control and animal identification. The company also designs and manufactures custom transponders for specific operating environments and packaging materials, including tags that work on metal and containers that store liquids. The majority of its transponders are compliant with the International Organization for Standardization (ISO), but Sokymat also manufactures transponders for close-loop systems and other special projects.
“Sokymat’s true competitive advantage is in fact our 15 years of working experience in transponder manufacturing technology,” says André Ziegler, CEO of Sokymat. “Thanks to the know-how we inherited as a company with a 40 year history in the development of advanced industrial automation equipment, we developed many of our own manufacturing lines and patented assembly technologies that make our transponders unique.”
In November 2004, Cubit Electronics, an RFID transponder manufacturing company based in Erfurt, Germany, joined Sokymat. Cubit’s expertise is in unique and patented technologies for advanced high frequency transponders. “With Cubit’s integration and by adding to our know-how the expertise that Cubit has in the area of 13.56 MHz RFID transponders, we acquire a competitive advantage on the side of technology,” says Ziegler, “just like when we introduced the direct bonding technology for low frequency transponders.”Cubit, which specializes in the production of HF transponders as inlays and prelams for contactless cards, will strengthen Sokymat’s position in the HF market. “This will allow our customers to obtain leading edge technology transponders of all frequencies,” says Thomas Hitzer, Sokymat’s vice president of sales, “and enable us to enter new market segments.”
Sokymat, which employs 250 people worldwide, has both a research and development center and a manufacturing plant in Granges, Switzerland, and in Ronneby, Sweden. In addition to its headquarters in Switzerland, Sokymat has offices in Australia, France, Germany, Spain, Sweden, the United States and the United Kingdom, and distributors worldwide including in Brazil, Canada, Denmark, Italy, Japan, Singapore and South Africa.
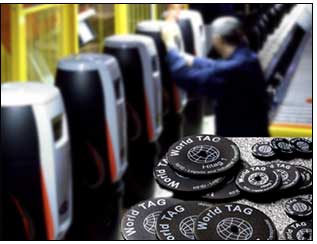
As part of Sokymat’s strategic plan for continuing global expansion, the company recently reorganized its customer service centers in Switzerland, Sweden and Germany. Trained service professionals respond directly to client inquiries in four languages—English, French, German and Swedish—to better satisfy the increasing demand for pre- and post-sales support
“A customer service department is the ideal interface to respond to our clients’ request for assistance in the fastest possible way,” says Ziegler. “Sokymat’s customer service centers will improve our reaction times to any inquiry and establish a further communication channel between our company and the market. With new products being developed in our R&D centers and added to our product portfolio all the time, we need to keep a strong contact with the different industry segments that use our transponders. Timely delivery of information to our customers will result in faster time-to-market for their applications.”
Sokymat is organized around three market segments: access and security, food and animal, industry and logistics. “Sokymat is present in all the major market segments that express a strong interest in the benefits of RFID technology,” says Ziegler. “For all of these target markets we have developed and continue to develop the most targeted and reliable solutions available.”
Sokymat’s access and security division develops and manufactures application-specific transponders for access control, employee time and attendance tracking, tickets for recreational venues and public transits, and other security applications such as e-passports and identification cards. Its product portfolio includes ISO cards (compliant with the ISO norm 7816-1, type ID-I), clamshell cards, key fobs, E-Units (Electronic Units), prelams (pre-laminated sheets that are sold to other companies which use them to produce ISO standard cards), wristbands and CCD labels (used mainly in DVD rental stock management).
The company produces about 40 million units for this market segment per year. Its ISO cards are widely used by public transits in Northern Europe. Currently, working in conjunction with partners in Europe and the United States, developing e-Passport is a major focus of Sokymat.The food and animal division develops and produces a wide range of full-duplex (FDX) RFID transponders designed to identify individual animals. The product portfolio includes both standard and customized transponders such as glass tags, disc tags and electronic units developed for identifying livestock, pets, fish and exotic animals. According to Jean-Miguel Robadey, product manager of the food and animal unit, all of these products comply with the ISO standards defined for animal identification (ISO 11784/85) and have the ability to conform to any future legislation that might require the traceability of animals from “stall to steak.”
In September, Sokymat SA Glass Tag RFID transponders were selected by Asocebú, one of the largest livestock farmers associations in Colombia, for its cattle tracking system. And in January, Sokymat transponders will be used in several RFID rollouts required by Canada’s National ID Program, to track cattle, bison and sheep.
Sokymat’s RFID transponders are also being used to track pets, as various governments mandate their use to provide quick identification and improve rabies control. For example, in October 2004, an EU regulation required all dogs to be identified with a microchip or a tattoo. The tattoo will be acceptable until the end 2011; afterward, only RFID will be used.
Another growth area for Sokymat is the use of transponders to track fish and exotic animals. Commercial salmon hatcheries, mainly in Norway and Chile, use glass tags to collect data about breeding and growth patterns and to control the population of Pacific and Atlantic salmon. And zoos are using the tags to identify their animals for internal management and exchange programs. The tags are also starting to be used to prevent poaching and the exportation of endangered species and rare breeds.
Sokymat’s industry and logistics division develops transponder solutions for tracking goods, from supply chain and inventory management to material handling and waste management. The company designs RFID tags that can resist harsh operating environments, including tags for beer kegs, gas cylinders, metal containers, tires and industrial laundry operations.
French company STP (Société de Traitement de Presse), a subsidiary of the French postal service La Poste, deployed a real-time tracking system to optimize the management of its 16,000 plastic containers used to sort and transport 3.5 million newspapers. The entire pallet tracking solution, which used 125 KHz read-write Sokymat World tags, was delivered by the French systems integrator and Sokymat partner Athelia.
Proprietary RFID solutions have been deployed in the commercial laundry industry for more than 10 years. To move toward an open platform, Dutch RFID systems integrator RFID-Net developed a system that enables a single scan station to read both the old proprietary tags and the new non-proprietary tags. It uses transponders from Sokymat’s Logi TAG family. In June 2004, Sokymat unveiled the Logi TAG 160 Sedna, its first ISO 15693-compatible laundry tag and the smallest 13.56 MHz laundry tag available on the market. The tag has a 64 bit UID and 56 bit one time programmable memory chip and supports Electronic Product Codes.In the Netherlands, major textile rental services and laundries, such as Initial Hokatex (Rentokil Initial group) and Lips Textielservice, have adopted this solution. More than two million Sokymat tags and two hundred reading stations optimized by RFID-net have been successfully installed since 2001.
Besides working to integrate new transponder products in the low- and high-frequency segment of its portfolio, Ziegler says Sokymat has been developing and designing ultra high frequency (UHF) transponders during the past two years and is manufacturing UHF tags for a number of projects. According to Egon Konopitzky, vice president of industry and logistics, due to customer demand, the company plans to unveil two new standard UHF tags by the end of this quarter: one for use in high temperature conditions, and one for use in harsh environments (resistant to heat, corrosion and shock). The products can be mounted on metal containers or used in close-loop manufacturing plants, such as in a paint shop in automobile manufacturing plant.
While Sokymat is keeping an eye on the standards issue, the company does not have immediate plans to develop UHF EPC tags. “The development of an international standard such as EPC, which is now endorsed by EAN and UCC, is indeed an important milestone,” says Ziegler. “But it is important to keep in mind that the market for RFID components is still substantially elsewhere.”
The volumes of manufactured EPC tags are still very small compared to those of traditional RFID tags, and Ziegler does not think this proportion is about to change in the very near future. He believes that price and reliability are two of the biggest issues facing the adoption of RFID technology in the world of retail and related supply chain applications. “Looking at the manufacturing technologies used today,” says Ziegler, “I just cannot see any manufacturer of RFID transponders reach the desired price point of 5 cents per unit.”
Ziegler believes the key to overcoming these two major hurdles is to improve manufacturing techniques: “Many challenges still need to be addressed in UHF technology, such as antenna designs that fit all items, low cost antenna manufacturing, chip handling and connection to the antenna for high volume and low cost production in combination with the tag’s functional reliability.”
Sokymat is working on these areas by exploring the different antenna manufacturing technologies and connectivity technologies. “We believe that additive antenna manufacturing technology will surpass subtractive technology for UHF tags targeting the extremely high volume retail applications [item-level tracking],” says Ziegler. The company plans to concentrate on research and development until it can guarantee the same quality that characterizes the rest of its product line.
“What we offer to our clients is always based on fully proven and highly stable processes. We aim to put on the market the most reliable transponders, manufactured according to the highest quality standards,” says Zeigler. “RFID transponders have been manufactured for decades and integrated into various systems over the years. What the end users are really looking for is a stable and cost-effective technology.”