Hundreds of offshore rigs populate the Gulf of Mexico, the North Sea, the Persian Gulf and other bodies of water to keep the world supplied with energy. The rigs are like industrial towns at sea that house the workers and the myriad items they need to live there, as well as the tools and equipment required to drill wells in the ocean floor, extract oil or natural gas, and transport the product back to shore. It can cost hundreds of thousands of dollars per day to operate each rig. If one essential part breaks or is misplaced and no replacement arrives in the next regularly scheduled ferry container shipment, a rig can be forced to halt production.
“As one vice president of an energy company told me, ‘If we lose something, FedEx doesn’t deliver 50 miles out into the Gulf of Mexico,'” says John Rommel, senior manager of RFID channel development for Motorola. As a result, companies sometimes have to hire helicopters to transport just one item out to a rig, at a cost of several thousand dollars per trip.
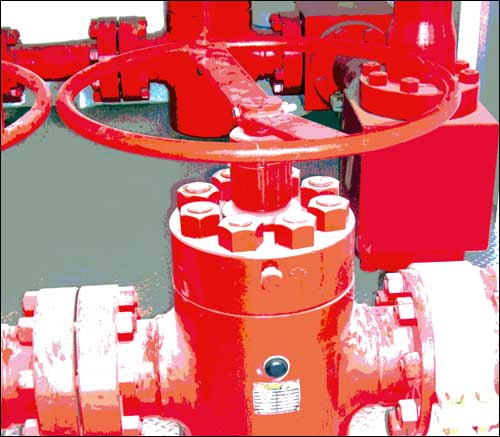
Keeping rigs operating 24 hours a day is one reason many leading-edge drill and exploration companies are deploying RFID to track products from their distribution centers in Louisiana seaports, which service 90 percent of the Gulf of Mexico’s oil production, to various deep-sea and inland oil platforms. RFID can ensure that the right containers stocked with the correct supplies—from toilet paper and soap to pumps and tools—are sent to the designated rigs. In addition, the U.S. government requires a manifest be created for each shipment and container delivered to these platforms, something RFID technology can generate automatically.
Saving money by improving asset management is another reason, and it represents a shift in focus for the energy sector, which has been considered somewhat of a laggard in technology adoption except when it came to oil or gas production. “If you’re getting $145 a barrel for the oil or $13 per MMBTU [1 million British thermal units], then your focus isn’t necessarily on losing an asset—it’s on making sure you can get an extra 5,000 barrels a day,” says Konrad Konarski, president of KBR Wireless, a provider of automatic identification and wireless solutions for the energy sector. That changed when the price of oil and natural gas dropped. “There’s more interest in saving money by managing assets, making sure you don’t rent an asset back to yourself, improving supply-chain efficiency, and not shipping products by helicopter that should have been sent by boat.”Konarski is a cofounder of the Oil & Gas RFID Solution Group (OGR), a consortium of petroleum companies, RFID vendors and academics devoted to developing common RFID applications across the energy industries. The group has been developing, testing and deploying passive RFID to track the contents of a shipment and tie that information to an active RFID tag with a location device—either GPS or real-time locating system (RTLS)—on the container itself. The passive tag would be used to generate an electronic shipment manifest, and the location device would let rig workers know the goods they need are en route.
The system, which will improve asset visibility as well as security, was also designed to address contingencies, such as natural disasters and business cycles. It includes portable RFID interrogators and battery backups, so companies can track supplies that might have to be moved from offshore rigs to DCs during a hurricane, for instance. Assets also may need to be returned for storage in DCs if production cycles ebb. To ensure the equipment is reused properly later, the system calls for tags to have extended memory, so they can store information—when and under what conditions (pressure and temperature) a pipe was used, and its grade of steel, for example.
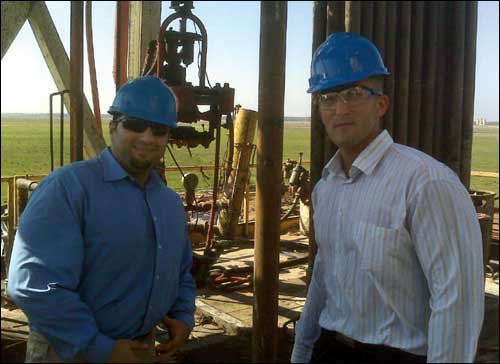
The oil and natural gas industries involve complex supply chains and processes, ranging from drilling and exploration on land-based and offshore rigs to storage and transportation of often liquid products, refining of products and eventual distribution worldwide. Chemical companies have similar environments, including production facilities, storage tanks, pipelines and rail cars. BP and Dow Chemical, which use oil and gas in many of their petrochemical products, recently joined the consortium to work on industrywide RFID applications.
The results of a combined industry approach to RFID will likely be that more products are developed for the sector, prices for the technology drop and rates of adoption increase, says Ben Zoghi, a professor at Texas A&M University who oversees the school’s Sensors and RFID Technologies Laboratory and also serves as OGR director. “A lot of companies are waiting to see what others are doing with RFID before they join the crowd,” Zoghi says. “If we have common standards, there is no reason to wait anymore.”
Energy industry spending on RFID solutions was up about 20 percent in 2008 to $125 million, according to Drew Nathanson, director of operations for technology research firm VDC. In addition to asset management, applications include smart cards for employee identification and safety, and equipment maintenance and repair operations. Utility companies, including providers of electricity, natural gas, water and sewage services, are also adopting RFID. “We’ve seen a big pickup in activity,” Nathanson says.Asset Management
RFID could help energy companies, which own or lease billions of dollars of equipment, avoid unnecessary costs and comply with the Sarbanes-Oxley Act of 2002, a U.S. federal law that requires public companies to improve accounting of their assets. Sometimes drilling companies share a rig and equipment. When assets are misplaced or stolen, they’re often written off and replaced. Leased equipment that is misplaced—or returned to vendor-managed locations without proper documentation—can result in penalties and extra charges. “There are a lot of co-owned or leased goods, such as tools, that involve billbacks and charges,” says Jason Brewer, strategic account manager for Avery Dennison, an OGR member.
Earlier this year, Nabors Canada, a land-drilling product and services provider, started using RFID to manage and maintain the equipment on its oil and natural gas drill rigs at 86 locations across Canada. Now the company can know at any given time where its assets are, as well as whether they have been maintained and inspected, and when. The RFID system replaced a labor-intensive, paper-based process of tracking the locations, conditions and histories of hundreds of assets, including generators, pumps and motors. “This allows field workers to use handheld interrogators to read tags on hundreds of assets to provide updated data on their location and operational status and exchange that data wirelessly with the back-end server,” says Greg Slater, VP of TrigPoint Solutions, which supplied the technology to Nabors.
Energy companies are also employing RFID to track reusable containers they use to ship products to customers. Air Liquide, a worldwide supplier of gases for industry, health and the environment, has RFID-tagged more than 500,000 industrial and medical cylinders. The company offers clients an online service to help them track cylinders—which store nitrogen, argon and other gases—through the supply chain. And Dow Chemical is starting a pilot this fall to track reusable 400-gallon plastic totes used to transport agricultural chemicals to farmers in Canada.
Manufacturers that supply equipment to the energy industry are adopting RFID to track production and validate customer orders. If pipes and other equipment are not made of the right gauge of steel and treated with the proper coatings to withstand pressure and heat, pipes can rupture and other accidents can occur, resulting in forced shutdowns and spills of hazardous or combustible materials.
In 2007, Tejas Tubular Products, a Houston-based provider of drill pipes and other products for the oil industry, deployed RFID to boost efficiencies in its manufacturing operations and to provide a documented history for each product, which is required for certification by the American Petroleum Institute. The RFID tags serve as a traceability system, recording manufacturing and quality-control information at each step in the production process.Maintenance and Repair
The equipment used to develop, refine and transport energy products is continuously reused by companies, and requires maintenance and servicing. RFID brings two benefits to maintenance and repair operations, according to KBR Wireless’ Konarski. First, the capability to write to the tag enables automatic updating of service and maintenance records. Second, because these operations are often performed in remote locations where there is no access to an enterprise system, RFID allows workers to access and update records on-site.
In addition, it’s common for energy companies to employ many contractors. “RFID can help maintenance personnel confirm that they are in the right place at the right time and working on the right part,” says Bill Moton, IBM senior manager for sensor solutions architecture. Also, unlike other technologies used to identify parts and equipment—including bar codes, serial numbers etched into parts and color-coded bands that distinguish types of pipe—RFID tags can be read by handheld interrogators without direct line of sight.
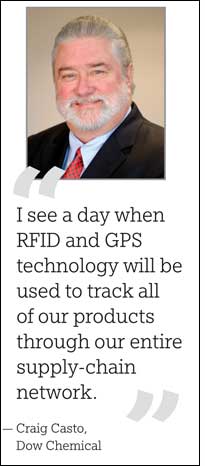
Craig Casto, global leader of Dow’s RFID GPS Auto ID Expertise Center, says the company has deployed the technology on 400 of the 650 railcars it uses to transport TIH chemicals and plans to complete installation by the end of 2009. In addition, Dow is testing a new product that combines a transponder with five- to seven-year battery life and a wireless mesh network through the railcar, so sensors can communicate to the GPS device without cables or wires. Dow is testing the technology on hopper railcars that transport polyethylene pellets and have sensors that capture data when gates on the top or bottom of the cars are opened to receive or release products. “The sensors will wake up the GPS device if the car is in transit somewhere between its origin and destination and someone tampers with the car openings,” Casto says. “It will send a message so that we can take the appropriate security response in real time.”
The extraction and refining of oil and natural gas can also pose safety and security risks to workers and other personnel. Shortly after a 2005 explosion at BP’s Texas City Refinery that killed 15 workers and injured more than 170 others, the company started testing active RFID badges for workers at its oil refinery in Cherry Point, Wash. BP now tracks 3,000 workers at the refinery’s processing area, tank farm and docks. “The deployment was focused specifically on improving visibility of individuals during a time of emergency or for emergency drill purposes,” says Moton, of IBM, which worked with BP on the project.Common Standards and Applications
The harsh environment in which much of the energy sector operates has presented a challenge for RFID deployment. Drilling and extraction is often done in remote and wet areas, under extreme temperature and pressure, subject to violent shocks, using metal equipment and structures—all factors that can interfere with the accurate reading of RFID tags. But recently, manufacturers such as Merrick Systems have developed tags that can withstand temperatures up to 400 degrees Fahrenheit and pressure up to 30,000 pounds per square inch.
For drilling companies and energy conglomerates, RFID adoption will be more attractive when the tagging of pipes, drill bits and other equipment is pushed back through the supply chain to manufacturing. Some companies, such as Merrick, offer this service, but uptake has been slow due to a lack of industry mandates or standards. In separate transactions, Dow is partnering with the Shenhua Group in China and Saudi Aramco in Saudi Arabia to build chemical facilities in those countries, with plans to build RFID into the design to track supplies, work in process and warehoused goods. “I see a day when RFID and GPS technology will be used to track all of our products through our entire supply-chain network,” Casto says.
In the future, RF nanotechnologies will be employed to monitor illicit entry into pipelines by thieves, which is a big problem in the Middle East. RFID can also be used in conjunction with sensors to control fluids in pipelines during transport. “The objective of using these technologies is to ensure that the fluid is safely and securely moved or delivered from one location to another and accelerate the response time to any illegitimate attempt to gain entry into the pipeline,” Konarski says.
In addition to participating in the OGR consortium, energy companies are working through standards bodies such as EPCglobal, a division of GS1, to foster interoperability for RFID technology so it can be used throughout the supply chain. Standards
are needed to allow RFID data to be incorporated into standard data formats now used in the oil and gas industry. They also are needed to define safe and unified operating frequencies for RFID. “If [you] go to China or Europe, you can’t use the same reader,” says Texas A&M’s Zoghi. “These companies don’t want to have 50 different readers for 50 different regions. Having a common denominator will help the industry drastically.”
Energy companies were focused on increasing production when oil was trading at record highs last year, but now they are using tools such as RFID to cut costs. “They’re looking for savings,” says Avery Dennison’s Brewer. “They’re improving labor by not having to search for tools as long. They’re improving the management of their inventory. And they’re continuing to look for ways to do more with less.”RFID Energizes Utilities
A few years ago, Sempra Energy, a $12 billion Fortune 500 energy services company that consists of Southern California Gas and San Diego Gas & Electric, discovered during internal audits that it was losing roughly $1.5 million a year to customers who were not being billed for their natural gas service. The reason? Gas meters installed on an estimated 3,300 homes and businesses had not been officially recorded by technicians, a process required to initiate billing.
To remedy the situation, Sempra turned to RFID. For the past two years, the energy company has been tracking gas meters for Southern California Gas customers from the manufacturer all the way to the installation truck. The return on investment was almost immediate—the RFID system ensured customers were billed, and it reduced the paperwork and time spent trying to track down unrecorded meters. “By saving us more than a million dollars a year, we’ve paid for that project a couple of times over already,” says Jim Pilant, who oversees Sempra’s RFID program. “We still occasionally have a few lost meters, but they’re easier to track down.”
Now Pilant says Sempra is exploring the use of RFID to track transformers and switches—which can cost more than $25,000 apiece—in the warehouse yards at San Diego Gas & Electric. In addition to improving inventory visibility, RFID could help the company better account for capital expenses. California utilities, including providers of electricity, natural gas, water and sewage services, are regulated by a public commission that determines the utility’s rate of return—or earnings—based partly on how much the company spends on capital improvements.
But it’s hard to account for the expensive equipment during storms, fires or other emergencies, when crews take it offsite with only written documentation or no documentation at all. Often, without RFID, yard managers don’t realize the equipment is missing or don’t know which capital account to bill it to. If a switch still shows up in inventory after it’s been removed, for example, the utility can’t claim it as a capital expense and earn a rate of return on that expense. “If you have a $25,000 switch,” Pilant says, “you can afford to put a $10 tag on it and read it as it goes out the gate during an emergency.”
RFID is also helping utilities monitor field services, such as inspections of utility poles and underground pipes, and maintenance and repair operations. “Once equipment is installed, you can capture the geo coordinates of where the asset is located and write it directly onto the RFID tag, so that you have records if you need to revisit that equipment,” says Sam Falsafi, senior energy principal for Shipcom Wireless, an RFID and supply-chain software solutions provider that works with Sempra and other utilities. “One of our customers had a recall on plastic gas pipes from a certain manufacturer that came out after the pipes were already buried. They had to go to each location and find where each gas pipe was to determine whether it was the recalled pipe. It turned out to be a $5 million issue for them.
“Think of an RFID tag as a USB stick you can put on an asset,” Falsafi says. “It makes the maintenance independent of any back-end application that needs to be available in the field, where connectivity is an issue.”