RFiD Discovery (a Paragon ID company) has released an automated solution to help hospital employees fill medical kits used in surgical units, to ensure the right equipment is available on time for each procedure. With the system, RFID-tagged or barcoded items are identified every time they are packed for a surgery or returned to supply shelves unused. RFiD Discovery’s app and software, which provide instructions for selecting each item, ensure that the right products are picked.
The system was initially deployed in 2016 by the first adopter, a large, acute National Health Services (NHS) trust hospital in the eastern United Kingdom that has asked to remain unnamed, and it has saved seven or eight labor hours a day for clinicians and nurses, enabling non-healthcare personnel to conduct the collection and return of unused equipment for operations. The solution is aimed at sparing nurses and other highly paid and busy healthcare providers from having to manage supplies and equipment instead of spending that time with patients.
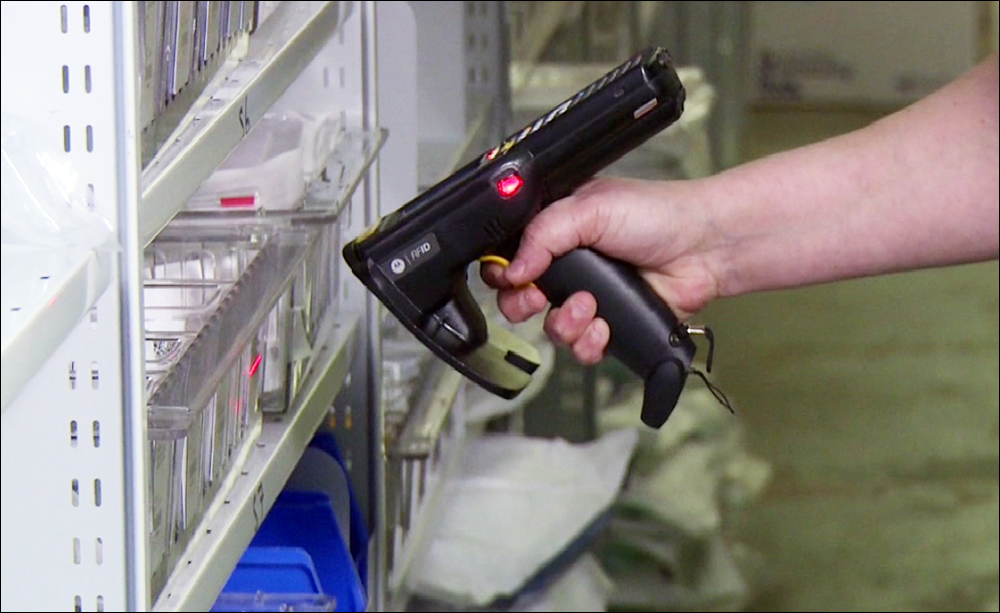
When workers begin their daily picking process, they use a handheld RFID reader and barcode scanner running RFiD Discovery’s app.
RFiD Discovery developed the solution for the NHS hospital and is now selling it commercially for hospitals worldwide. The company designed the system to make the collection of tools and supplies more automatic. Another U.K. hospital is now deploying the technology, and RFiD Discovery reports that the system is expected to save its clinical staff time, as well as ensure no procedure is delayed due to a failure to prepare the appropriate equipment in the surgical room. RFiD Discovery views the technology as a tool to help hospitals address the backlog of surgeries that have occurred due to the COVID-19 pandemic, says Simon Dawkins, the company’s lead RFID consultant.
The traditional responsibility of selecting equipment for each surgery, Dawkins says, has fallen on highly paid nurses and clinicians, who must go to the supply room and collect equipment before each procedure. They typically know what they need and may select multiples of some items to ensure anything that might be required during an operation is on hand. Items not used could then be returned to the shelves. However, such a manual process not only consumes time for nurses but also leads to high volumes of goods being moved to and from surgeries, with limited attention to what might have been wasted or gone missing.
For nurses and other clinicians, Dawkins explains, the point is to ensure all equipment needed during every surgery is available. The solution is intended to make the process of selecting and returning goods transparent and easy to accomplish. “We turned the process on its head,” he says, by building a system that can guide individuals who collect equipment through the process for each patient procedure. Dawkins likens it to making a grocery store run with a list of needed items, though the data is digital and the system automatically tracks what is being done to prevent errors. The hospital uses the software and app to manage data, and each site can opt to employ UHF RFID tags, barcodes or a combination of the two.
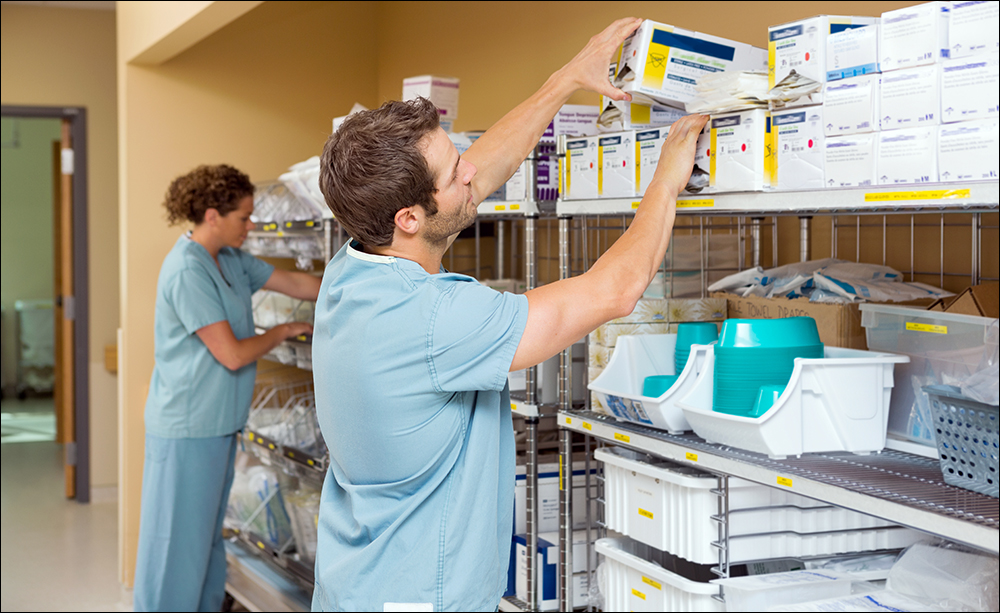
The solution is aimed at sparing nurses and other highly paid and busy healthcare providers from having to manage supplies and equipment.
Each new supply, implant or tool is tagged with a unique ID number that is encoded or printed on the tag and is then linked to that item in the software. The software also stores the shelf on which every product should be stored. When workers begin their daily picking process, they use a handheld RFID reader and barcode scanner running RFiD Discovery’s app, which displays the first scheduled surgical procedure and lists the items required, along with the shelf on which they are stored. The users can then collect the necessary items in reusable totes, scanning or interrogating each tag as they do so.
The app updates the list after each scan and displays a warning on the reader if the wrong item is selected. The app does not finalize the order until all items are packed, and users can add additional items through exception reports, as well as enter notes if necessary. They would then read the RFID tag on the tote, linking it to all items packed within for that procedure. The system prints a label listing the name of the patient and the tools placed in the tote, which can be attached to it.
The tote is moved directly to the assigned surgical room, where an RFID reader in that room can capture the tote ID to confirm what has been received. After the procedure has been completed, any unused items can then be placed back in the same tote (some might not have even been removed), to be returned to the supply area. A staff member scans or reads each tag as the goods are returned, and the collected data can be stored to provide a record of which supplies, tools or implants were used on that patient.
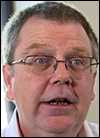
Simon Dawkins
“What it means is that every operation starts on time,” Dawkins states, “and everything needed is in that box.” Post-surgery, he says, the data provides an opportunity for analysis. “Over time, we can start to analyze what they are using and not using.” For instance, if certain items are often being added to a procedure’s list or are frequently returned unused, the system could determine whether the hospital needs to update its procurement systems. Long after the surgery is done, the data could be used in the event of a recall, such as an implant that could be traceable to a particular patient.
The company is releasing the solution after five years of its use by NHS trust hospital, as demand for surgical efficiency has been increasing. That may be due, in part, to the pandemic, the company notes. “Because of COVID, there is a backlog on surgeries,” Dawkins explains, “so this is about making sure they have everything they need so operations start on time, and [helping] them deal with that backlog.”
The solution includes Paragon ID’s UHF RFID tags, but it is agnostic when it comes to RFID readers and can include a reader that suits a particular use case and cost requirements. For example, low-value consumables might receive barcodes, whereas high-end items such as implants or tools would have RFID tags, and a handheld device that could read RFID tags as well as scan barcodes would typically be employed. The system can also include real-time location capability via overhead readers, or smart cabinets for automatic data regarding inventory levels within supply areas.
A hospital that conducts 55,000 surgeries annually in 42 theaters is using the solution for all of those theaters. Since the deployment, the facility has found that the solution has saved it 60 pounds of reduced waste per operation, by identifying where supplies are located and ensuring they aren’t discarded unused. In addition, it has achieved clinical time savings, and the technology has led to a stock reduction of a million pounds. For many hospitals, RFiD Discovery indicates, the challenge in adopting technology is in breaking existing traditions and a reluctance on the part of healthcare workers to change.
“You’re moving responsibility from OR staff to the procurement side,” Dawkins says, which can raise concerns for healthcare providers until they adjust to the new solution. Many facilities, he adds, may not realize how much product is being wasted until they obtain the data that RFID can provide. If management is unaware of which products are being discarded without being used, a hospital doesn’t know the cost of such waste. “It’s the analytics that makes the whole thing work.”