Polish RFID technology company Smart Technology Group has developed what it calls the Safe and Sound Evacuation, which employs radio frequency identification technology to ensure personnel are accounted for at a work place in the event of an emergency. The system relies on passive ultrahigh-frequency (UHF) RFID readers and lanyards worn by workers to identify when they pass specific locations.
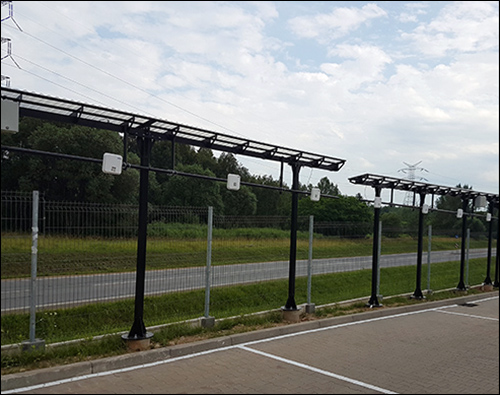
Ficomirrors Polska (part of Ficosa International), in the Silesian area of Poland, was among the early adopters of this technology, and has been using the system since June 2017 to ensure the location and thus the safety of more than 1,000 workers. Ficomirrors makes automotive mirrors, windshields and other products used on vehicles worldwide. It sought an automated system for its facility that could better ensure that all workers could be accounted for in the event that an evacuation was necessary.
Before the implementation of the Smart Technology Group’s RFID solution, the verification of people at collection points “was based on paper attendance lists and reports,” says Anna Zagala, Ficomirrors Polska’s Environmental Health and Safety (EH&S) manager. The team leader was responsible for the company’s ongoing update. “At the time of the evacuation, they were used to verify the personal status at the collection point and to determine the number of missing persons.”
This is a common method for evacuation management across most companies, according to Karolina Kozłowska, Smart Technology Group’s president and CEO. Evacuation systems are typically coordinated manually, she explains, and can generate a great deal of confusion during an actual emergency. People either visually identify and count individuals—a process prone to errors—or ask that employees scan proximity cards to indicate their locations. The problem in an emergency, she explains, is that workers may not always remember their proximity cards as they evacuate, or have time to scan them.
Knowing who is onsite at any given time, as well as whether or not all those individuals have left the premises during a fire or other emergency, is critical. In practice, however, companies like Ficomirrors found that managers often cannot be immediately sure that everyone is safe.
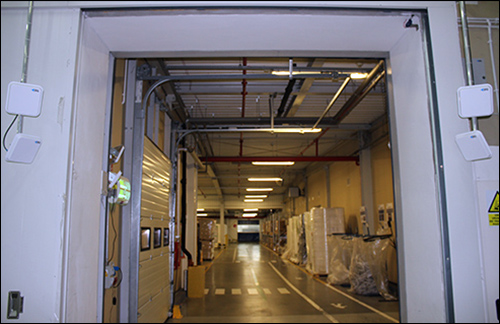
Smart Technology Group provides two versions of its evacuation system: one that identifies employees in specific zones and another that identifies them only at evacuation or mustering points. The firm provides a UHF RFID tag on a lanyard for each employee, with RFID readers installed at doors or gates. As individuals with RFID-enabled badges pass the gates, the tag IDs are read, thereby linking each badge to a specific individual. Those IDs are then displayed for managers in the software.
The readers forward the collected data to the software (which resides on a cloud-based server) via a cellular connection. The data can be accessed via a user ID and password from a PC, laptop or tablet device. In that way, personnel at each collection area can view who has reported to that location and who remains unaccounted for. According to Smart Technology Group, the readers can capture as many as 350 tagged individuals simultaneously as they pass near or through a gate.
Users of the software can view when each individual passes a specific read, the direction in which he or she is moving, and thus whether that person has been safely evacuated or is in harm’s way. It also enables managers to view the number and identities of employees who need to be evacuated.
In the case of Ficomirrors, Smart Technology Group installed six of its Master 01 RFID gates, each at a collection point at which workers congregate during an evacuation. Each reader comes with four A24 RFID antennas to identify the direction in which each worker is moving as he or she passes the reader. Ficomirrors has tested the technology in practice evacuations since the system was taken live this past summer. “They do testing and practice evacuation regularly to be prepared in case of any danger,” Kozłowska states.
When installing the system, Zagala says, “We were primarily concerned on eliminating weaknesses in the current procedure and streamlining the entire evacuation process. This, in turn, significantly reduces the risk of people’s health or live treatment of at the time of fire.”
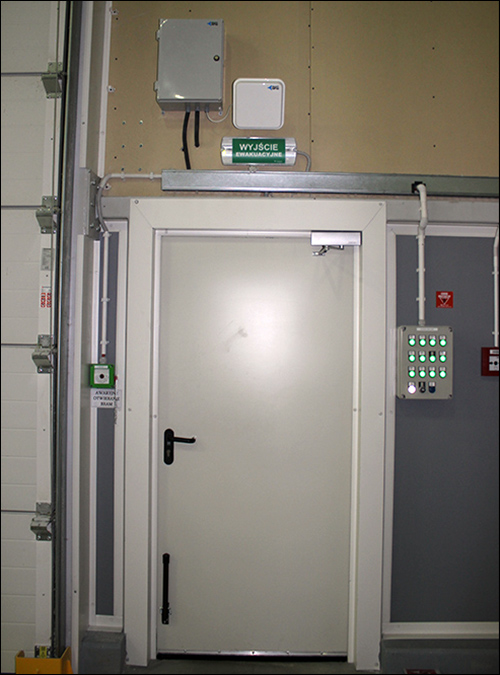
To date, Zagala reports, the company has found that it can better control the evacuation process. An evacuation coordinator could observe, on his or her tablet, who is inside the building, who is leaving the premises and who is reporting to each collecting point. “If someone was lost, the coordinator would exactly know who,” she says, as well as where the individual was last identified via the RFID readers.
While the technology’s primary benefit is worker safety, Kozłowska notes, the technology can also be used to understand the movement of traffic into and out of a building or yard, and thereby provide business intelligence to a company. She says the system is intended for use at assembly or production sites, in warehouses and in office buildings.