German energy technology company SSC Wind is using passive ultrahigh-frequency (UHF) and high-frequency (HF) RFID tags, in combination with GPS technology, to manage tools and equipment stored within containers and service vehicles on its job sites. In so doing, the company can better account for the tools and ensure their return at day’s end, thereby saving the cost of searching for or replacing them. The solution was supplied by track-and-trace systems provider DHL-MyIDentification, with RFID tags attached to tools that were provided predominantly by assembly and fastening materials maker Würth.
SSC Wind first deployed the solution in 2014 as a pilot involving 1,000 pieces of equipment and 600 tools stored in a single container and one vehicle at a lone site. This year, the company is deploying RFID-tagged items at each of its energy projects throughout Europe—a total of about 20 different locations.
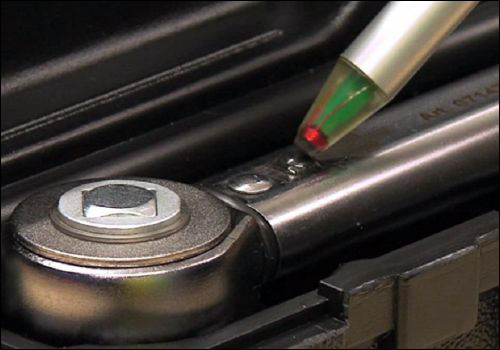
For the past 14 years, SSC Wind has been providing operations and maintenance support at various European wind farms. In this capacity, the company has built and now maintains 1,300 wind turbines, both onshore and offshore.
At each project, the firm sends a team of workers who use wrenches, pliers, slings, harnesses and other equipment, all stored onsite within vehicles or trailers. The teams are expected to focus on maintenance tasks, but are often distracted by the need to locate equipment. Losing tools can be costly. The company also needs to track the use of tools to be sure they are properly calibrated and certified.
SSC Wind had been seeking a cost-effective way to simplify the tasks of technicians, electricians and supervisors. To that end, it launched a project known as “Partnership…The Next Generation,” which DHL-MyIdentification delivered in order to enable the automatic tracking and tracing of tools and equipment.
“In our business, the requirement for reliable equipment is key to improving operational reliability, safety and functionality,” says Rene Psarski, SSC Wind’s managing director. “We work in a highly demanding and developing industry. SSC Wind is continuously looking at how to improve the efficiency of operation processes.”
Before the company deployed the RFID system, Psarski says, equipment could be lost or returned damaged, and there was no history of which assets were used. Often, only 25 percent of the tools were returned. The RFID system, with GPS location data and a satellite connection, enables the company to monitor the locations of all assets on each work site. With RFID, he reports, 98 percent of assets are now returned, with only 1 percent coming back damaged.
Every tool or other asset was fitted with a DHL-MyID MasterTag. A UHF RFID version of the tag is affixed to small items stored in tool bags, while slings and other assets are fitted with HF 13.56 MHz MasterTags compliant with the ISO 15693 standard. By using HF technology for most items, rather than UHF, the company can be assured that a technician has scanned any given asset. “We want to be 100 percent sure that the technician scans that specific security- or safety-related item,” explains Pieter de Valk, DHL-MyIdentification’s CEO.
All MasterTags are designed to be rugged, de Valk says, and to be mounted on metal. For the SSC Wind use case, DHL-MyID supplied the UHF and HF readers and the UHF tags, which it acquired from an unnamed third party.
The cloud-based DHL-MyID Inside software offers a variety of functions and applications, including issuing alerts, collecting and analyzing data from inspections and logistics, and mapping the locations of tagged items based on GPS data. DHL-MyID evaluates a customer’s site prior to customizing these functions, based on the customer’s specific needs, de Valk explains. “We build a so-called bridge to the existing ERP or IT platform of the customer,” he states. “So we do not interfere with the existing IT infrastructure, unless the customer asks us to build onto their platforms as well.” He adds that the solution can be used offline if no Internet connection is available.
First, an SSC Wind worker uses a handheld HF RFID reader to log into the DHL-MyID software on the hosted server. The employee reads the HF MasterTag embedded in his or her key fob ID, as well as the ID numbers of the tags on any equipment he or she is borrowing. At the end of the shift, the worker returns the items to the trailer and again reads the equipment tags, thereby indicating that they are being returned. Tool bags in which small tools are stored also come with passive HF tags, and a worker who borrows a bag of tools interrogates that bag’s tag. Such an individual might also utilize a handheld UHF reader to interrogate the passive UHF tag affixed to each of the approximately 25 tools inside the bag.
A project supervisor can use the technology both during and after a worker’s shift to update inventory data, by reading equipment tags either at the end of the day or at the employee’s location. The software stores an expiration date for each item, and can display an alert in the event that an asset requires scheduled maintenance or calibration. The supervisor or worker can also input data about an item, such as a defect. Additionally, the software can issue an alert via text message or e-mail to project managers or supervisors when an item is due for maintenance or recalibration within a set period of time, without requiring that a user read its tag ID.
The handheld reader’s GPS module collects the location where each tool’s tag is read, and that data is then forwarded to the cloud-based server via a GSM network. If no GSM network is available (such as at an offshore site), a worker can operate the device in standalone format. Once a Wi-Fi connection becomes available, the device will transmit all collected data to the cloud. In this way, the system knows where each item was located when its tag was being read.
Since the system was installed, Psarski says, productivity has been improved by approximately 20 to 25 percent, due to workers spending less time searching for tools. As a result, he adds, labor costs have been reduced by 25 percent, while the cost of replacing missing assets has also saved the company a significant amount of money. Because containers need not be moved as often for the inventory to be counted at an SSC Wind site, the cost of transporting those containers has been lowered by 75 percent.
Previously, the counting of the tools and equipment stored inside a returned container took two to three days to complete, as employees manually checked inventory counts and confirmed calibration. “RFID allows us [automatically] to check… what assets need to be checked again, repaired or replaced,” Psarski says.