Tenaris is a global provider of steel pipe products and related services, which it offers through a network of manufacturing facilities, service yards and commercial offices worldwide. TenarisDalmine, the company’s steel pipe operations in Italy, is that country’s leading producer of seamless steel tubes for the automotive, energy and mechanical industries, with an annual production capacity of 950,000 tons of finished products.
To improve its production efficiency, TenarisDalmine wanted to be able to track, in real time, its work-in-progress (WIP) materials—on average, 20,000 tons of steel pipes daily—that move between 34 production lines via 500 metal storage pallets within a 370-acre industrial area. The pallets are moved by two types of trucks: One is a lifting platform made by Cometto, in which one or two pallets are loaded on top of the vehicle, while the other, from MAFI Transport Systems, tows industrial trailers.
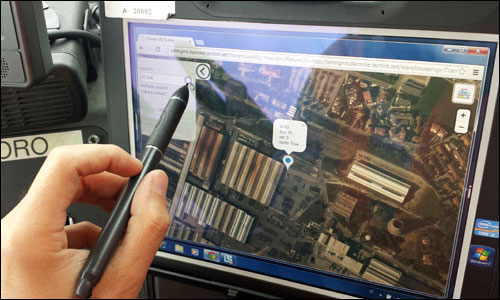
TenarisDalmine’s existing process for tracking material was manual, which had a number of shortcomings, says Massimo Mariano, the company’s product warehouses and service centers manager. Team leaders or drivers had to look for WIP material on an order or item basis, to assure the proper sequence was being fed into each of the company’s 34 production lines. That involved searching for identification numbers that were painted on each pallet or trailer. Inevitably, there were breaks in production or shortages of materials due to inaccurate traceability. In addition to reduced productivity (because of the time it took to find the correct pallet), there were safety risks for those looking for WIP pipes in certain areas during operations.
To address the traceability challenge, TenarisDalmine deployed an RFID solution in November 2013 to automate the processes. Within three months, Mariano reports, the company was seeing benefits.
A Solution in the Pipeline
In early 2013, TenarisDalmine began exploring RFID solutions. It focused on RFID technology for three reasons, Mariano says: the huge physical area in which the tracking activities would be performed, the need for real-time location data in order to feed production lines without interruptions or delays, and the large number of objects to be tracked.
To help identify the best system, the company brought in LIUC Lab#ID, of the University Carlo Cattaneo-LIUC, an educational institution founded in 1991 by 300 Italian entrepreneurs. LIUC Lab#ID specializes in RFID industrial project design and implementation, according to Mariano, who served as the project leader. “Our main goal,” he says, “was to find a partner that could speed up the technology selection and system design, and at the same time have a good knowledge of the system integrators market.”
TenarisDalmine created a crossfunctional team with representatives from its supply chain, IT, industrial automation, production and help desk operations. It also included individuals from La CISA and CGI—two companies Tenaris subcontracted to manage mechanical activities related to transportation, and to repair and manage maintenance activities on pallets—as well as representatives from Lab#ID and Aton Systemes (the firm selected as the project’s systems integrator).
After evaluating technologies from more than 150 companies, the team selected an ultrahigh-frequency (UHF) RFID system comprising the following components: CAEN RFID ION R4300P readers, Motorola AN720 antennas, Confidex Survivor tags for pallets and Xerafy Bric tags for geo-fencing. Aton, meanwhile, developed the middleware.
Tenaris chose the CAEN reader, Mariano explains, because it matched the company’s performance requirements, could be installed on a vehicle, and was expandable (its USB host ports allowed Tenaris to install the GPS unit required for the project) and flexible (the underlying Linux system is standard and open, so the company could install the middleware software on it and be able to quickly design the logic). In addition, it was ETSI-certified.
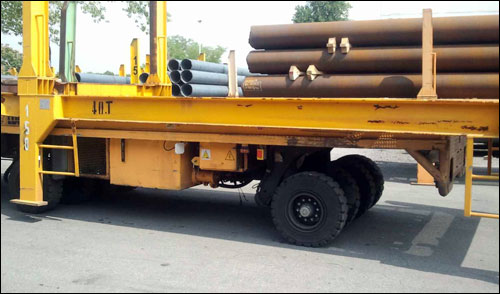
The Motorola antenna was selected because it offered the width of field (100 degrees) necessary to read tags placed directly in front of it on the pallets and under it (beneath the concrete in the loading area). This also enabled the reading of tags on the side of the truck, so pallets could be geo-located while the vehicle passed along them, to provide added redundancy. In addition, the antenna is impact- and vibration-resistant, and can withstand a range of temperatures.
The Confidex tags are extremely rugged and perform well, Mariano says, and were the company’s first choice when designing the project. The Xerafy tags are designed to be embedded in concrete, he notes, and were used for this purpose.
The project launched in April 2013, and was completed by November of that year. That included a three-month feasibility study, analysis of existing processes, vendor selection, technology testing, cost and investment analysis, a two-and-a-half-month pilot project, a two-and-a-half-month implementation and fine-tuning of the system, and the training of personnel, including truck drivers, functional teams and management.
Finding Pallets
The main goal of the application was to locate large pallets (metal frames measuring 10 meters by 10 meters) in a large open-air storage lot. A secondary goal was to detect the pallets as they are placed in a particular loading area, where the tubes from production are loaded onto them.
Technicians attached two tags on each pallet, programmed with the same identification number, which is also stored on a central server. They installed three antennas on each Cometto truck, in such a way that at least one pallet tag is within read range (2 meters) of at least one antenna, for each possible placement of a pallet on the truck. As the Cometto truck slides under the pallet, the antennas read all the tags. “We can be confident that we have, at the very least, one reading at loading and one at unloading,” Mariano states.
The three antennas are connected to an RFID reader installed inside the truck’s cabin, which communicates with the central RFID system via Wi-Fi. A GPS unit is also connected to the reader.
The MAFI trailer trucks are equipped with two RFID antennas at the rear. An RFID reader and Wi-Fi and GPS antennas are installed in the truck’s cabin.
As the pallet tags are interrogated, the logic on the reader associates the event to the time and position coming from the GPS system, then stores in the reader’s memory the first reading of the tag, another reading every 30 seconds, and the final reading when the tag is not seen for at least one minute. This data is stored and forwarded to the central server via the Wi-Fi connection.
“This allows us to geo-locate the pallet currently loaded—and being moved—on the truck,” Mariano says, “and to geo-locate pallets that are not loaded on the truck, but merely fall in the reading range of the antennas as the truck passes along them.”
All data from the 14 trucks is collected by the RFID system and recorded in a database. The culled data is then converted in such a way that the company can determine exactly when a pallet was transported by a specific truck along a particular path.
Both vehicles are equipped with tablet devices that drivers use to display, via a Web browser, the positions of the pallets on trucks, and to search for a given pallet. Each tablet has a software agent that reports the tablet connection’s status to the central server. “This way,” Mariano explains, “centrally we are able to have a complete overview of the situation of the various equipment installed on the trucks at any given time.”
Multiple Challenges
The first challenge the project faced involved identifying where on the transport vehicles to place antennas and tags. Cometto trucks are 12 meters long, and the pallets can be loaded onto the vehicles within two configurations (a single full or empty pallet, or two empty pallets). A pallet can be loaded in three possible positions: in the middle of the truck (single full or empty pallet), in the anterior portion (the first of two empty pallets) or in the rear (the second of the two empty pallets). “Therefore,” Mariano states, “during every loading activity. it is a hard operation for the driver to load the pallet in the exact position.”
Furthermore, antenna placement along the flanks of the trucks must take into account variables such as heat coming from engine and exhaust tubes, as well as vibrations and proximity to moving parts. “By taking into consideration these environmental conditions, it took a fair amount of time for testing and fine-tuning the system in order to find a suitable placement for the antennas,” Mariano recalls. “The technology allowed for a good reading range [about three meters], even with all the metal structures present alongside the antennas.”
Also critical was deciding whether to place an RFID reader inside the truck’s cabin. “The peculiar configuration of the Cometto cabin creates a high amount of vibrations inside the cabinet,” Mariano says. “Since we elected to install a part of the software directly on the reader, we had to test and assure the correct working parameters under different environmental conditions, such as heat, cold and vibrations.”
Another, unexpected issue related to the project’s geo-fencing requirement. “We were required to locate a pallet when it was brought into a particular loading area,” Mariano says. “This area was covered by a wide metal roof that disturbed the GPS signal and inhibited the GPS positioning. As a consequence, we had to bury RFID tags specific for concrete within the basement of each loading bay of the mill, so that the Cometto truck would read them while entering or exiting, and register the fact that it entered or exited that area.”
Quick Benefits
The RFID deployment transformed the manual process of tracking the internal movements and locations of pallets. Each production line now publishes the list of items to be fed on a dedicated Microsoft Sharepoint library, according to the production sequence. Drivers use the onboard tablets to access the lists in real time, and the tablet displays the exact position of the pallet containing the required material on a geocoded map.
Within three months, Mariano reports, Tenaris realized several benefits. Most important is direct and immediate access to information without the need for intermediate processes and people, which increases accuracy, decreases the amount of time necessary to conduct searches, and makes for more productive use of internal transport vehicles.
Inventory accuracy was improved by 25 percent at the main rolling mill. In addition, gasoline costs were reduced by 7 percent, thanks to the company having each pallet’s exact GPS position available on the tablet onboard each vehicle.
What’s more, the technology improved the safety of employees, who no longer needed to move around within the working area—where there are trucks and forklifts handling heavy units of pipes—to manually search for pallets.
The data is a “trove” of information for TenarisDalmine, Mariano says, and can potentially be used to monitor many aspects of the firm’s logistic processes. For example, he notes, it can provide analysis of the most active areas of the lot, in terms of pallet placement and truck passage.
TenarisDalmine plans to extend the project this year, including adopting software that is usable both from desktop and mobile devices, to provide managers with a summary of information related to the RFID system and plant operations, such as RFID system diagnostics, days and hours of use, the number of pallets tracked per hour, and the number of trucks in use. The software will make it easier to create ad hoc statistics.
The company also plans to extend the system’s use to six additional production lines. “The installation done inside the mill area can be reproduced within other automatic lines,” Mariano states, “thus extending the traceability to all areas in TenarisDalmine.”
Following its successful implementation of RFID, TenarisDalmine has received requests for information from Tenaris plants in other regions considering similar deployments.