Increasingly, the technologies on which we rely—from cell phone transmission towers to server farms—rely, in turn, on a constant supply of power. Keeping things running, no matter what, requires reliable backup systems.
Batteries tend to be expensive, as well as sensitive to cold and heat extremes, and often last just a few hours. When batteries are insufficient for a particular task, some turn to fuel cells—automated electricity generators that run on hydrogen, alcohol or other fuel, and can supply power for up to a week, depending on the fuel supply. Fuel cells have been used everywhere from the space shuttle and military submarines to remote weather stations and cell phone towers.
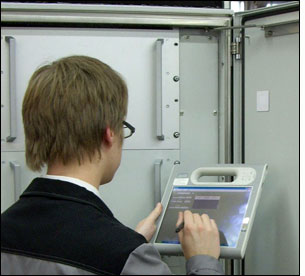
Fuel cells are not maintenance-free, however. To make servicing and repairing fuel cells as efficient as possible, Rittal, a Herborn, Germany, integrator of fuel-cell solutions, turned to RFID technology. To assemble complete fuel cells, the company takes fuel-cell modules supplied by a third party and adds its own enclosures and system components to them (such as a fan, a heater, a power bar and a circuit breaker). Using an RFID solution supplied by German systems integrator Schreiner LogiData, Rittal incorporates an RFID tag inside the enclosure at the end of the production process, after the assembled fuel cell has been put through final testing. The company ultimately plans to outfit all of the fuel cells it sells with the technology, at no extra charge to customers. “The chips contain numbers similar to electronic nameplates, which identify the fuel cell,” says Oliver Puetz-Gerbig, a Schreiner engineer.
Information such as the model type, serial number, production date and location can all be read directly from the fuel cell, using an RFID interrogator built into a tablet PC carried by maintenance technicians employed by Rittal. By storing repair and maintenance data directly on the RFID tag’s 1024 bytes of memory, Puetz-Gerbig says, the system goes beyond what could be accomplished with a standard bar code. “The full history of the fuel cell is stored on the tag,” he states.
That’s critical when it comes to servicing fuel cells, which are often installed in remote or forbidding environments. “A fuel cell might power a cell phone transmission tower on a high mountain,” says Hartmut Paul, a Rittal engineer in charge of fuel-cell development. “If there’s heavy snow, there may be a power interruption, and the fuel cell serves as a backup power source.”
Because of the remoteness of some fuel cells, maintenance could be tricky. “The information the technician needs can’t just be in a database at the headquarters; it has to also be in the product itself,” says Christian Goriup, a Rittal project manager. “This way, we have a complete service history on the product itself.” Consequently, there is no need for a cell phone or data connection to a company’s headquarters, because all of the information a technician requires is stored on the fuel cell’s RFID tag.
Not only does the system make record-keeping easier for technicians, it also has the potential to save money. Fuel cells are complex machines—essentially, they are highly sophisticated generators with a lot of moving parts, including pumps, filters and ventilation systems. With a standard system, a technician making an annual inspection might change out all filters, just to be safe. “If I can save information telling me when each part was installed on an RFID chip, then the technician can tell the whole life-cycle of the fuel cell,” Paul explains. “If the RFID chip shows the filters were changed just a year earlier, and they still look fine, you can save on costs and leave them in.”
Because fuel cells are often installed in spots that are difficult to reach, Schreiner employed high-frequency (HF) 13.57 MHz passive RFID tags that can be scanned at a range of approximately 10 centimeters (4 inches). The transponders comply with the ISO 15693 standard, and are sourced from UPM Raflatac and other suppliers. The tags are placed within the fuel cells’ sturdy enclosures in order to protect them from the elements. The big challenge, Goriup says, involved creating a system that integrated software to work with the database at Rittal’s headquarters, a compatible RFID interrogator and a tablet PC for the technician in the field, as well as the tags on the fuel cells.
To date, according to Rittal, the system has been put through internal testing, and the firm hopes to begin installing RFID-enabled enclosures for customers within the next few months. Schreiner’s Puetz-Gerbig says the system has broad potential for other applications as well. “The advantage is, you can change and add info to the tag,” he says. “It’s an interesting solution for every product or machine that needs regular maintenance.”