Migros Ostschweiz (East Switzerland), one of the 10 regional cooperatives belonging to Swiss supermarket chain Migros, is employing radio frequency identification technology to automate the confirmation of which goods are loaded onto vehicles destined for particular stores, and when this occurs. By using the solution, known as Load Unit Identification and Positioning, or LUIDO (LU-Paletten Identifikation und Ortung), the company can ensure that forklift drivers need not visually verify that they have the correct load, move boxes to do so, or scan bar codes. Instead, they can merely proceed with going about their job of moving goods from the staging area onto trucks, while receiving an alert in the event of a mistake.
Tomislav Pavicic, Migros Ostschweiz’s supply chain architect, says that his company’s adoption of LUIDO is one part of a wider restructuring of the logistics enterprise architecture. The company had recently introduced an Electronic Product Code Information Services (EPCIS)-based database (repository), as a basic component to collect data regarding shipments’ movements and locations.
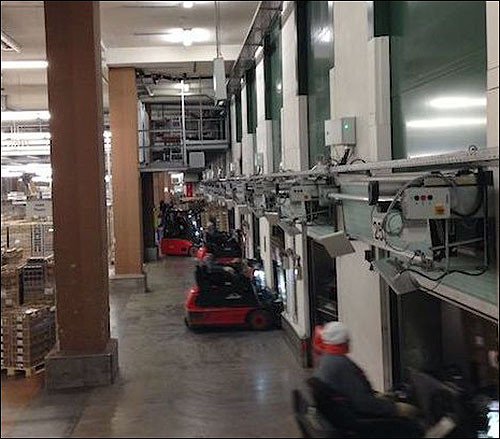
Migros, the largest retail company in Switzerland, is run as a cooperative, and counts a quarter of the nation’s total population of 8 million as members. Each regional cooperative is run independently, while a central organization, Migros Genossenschafts Bund (MGB), manages shared functionalities, which includes managing a pool of 10 million returnable transport items (RTI) and the RFID-tagging of those containers. The regional cooperatives manage their own manufacturing operations, such as meat processing, as well as distribution and warehouse operations. Products also arrive at the facilities from external Migros manufacturing locations and third-party suppliers. The Migros Ostschweiz distribution center in Gossau features a high level of automation. It operates its own trucks to transport goods to stores, in some cases delivering up to eight loads of fruit, vegetables, milk, cheese, fish and other perishable foods to a single store on a given day.
Migros Ostschweiz ships 6,000 pallets of goods daily, and each pallet can include more than 100 plastic RTIs filled with products. The pallets are shipped out of 120 dock doors, 29 of which are located within a refrigerated area in which dairy products, meats and other goods are kept cold prior to transportation. The Migros Ostschweiz DC already uses RFID technology on the conveyor systems in its own meat-processing operation, as well as in perishable picking and RTI packing areas. Late last year, it began working with RFID solutions provider Vilant Systems to devise an automated method of managing the loading of goods onto trucks, initially at the refrigerated area.
The company sought a solution that would track what is loaded onto each vehicle destined for a particular store, but it did not want the system to interfere with workers. According to Antti Virkkunen, a Vilant cofounder who manages Central European operations from Vilant’s Swiss office, Migros Ostschweiz’s philosophy is that forklift drivers should be allowed to carry out their jobs as they always do, including picking up “virtual handling units,” also known as load units (consisting of pallets loaded with multiple RTIs), from the staging area and then loading them onto the appropriate trucks. The onboard computers are used to receive alerts regarding detected exceptions. The company’s management wanted to disrupt that process only if a mistake was about to be made, such as parking a vehicle at the wrong dock or loading the incorrect pallet onto a truck.
“The great benefit of our RFID implementation is that we can support our employees without increasing their workload,” explains Daniel Balmer, Migros Ostschweiz’s director of transport logistics. “They do not have to enter data or manipulate systems, which would be the case for bar-code scanning. It would be an impossible increase in workload to track 6,000 pallets daily in any manual way.”
For the solution, Vilant provided the RFID hardware, along with its Visibility Manager software. Visibility Manager receives data about each shipment from Migros Ostschweiz’s central EPCIS-based database, identifies a tagged RTI’s location and the direction in which it is moving, and then transmits the load event data back to the EPCIS repository. “Exceptions are alerted to the users immediately by the RFID system, for immediate corrective actions,” Balmer explains.
Migros Genossenschafts Bund permanently applied washable passive ultrahigh-frequency (UHF) RFID tags from a variety of vendors to the RTIs, Virkkunen says. A pair of tags—identically encoded and printed with the same serialized Global Returnable Asset Identifier (GRAI)—are attached to each container (there are seven different types and sizes of RTIs), which is packed with goods according to store orders, and is then stacked on a pallet in order to create a virtual handling unit. The automation systems automatically input data about the goods being packed within the container, so that management knows not only which containers are destined for which store, but also what is packed in those shipments.
Once the pallets are fully loaded with RTIs, they are stored in the staging area to await a truck at the appropriate dock door, and a forklift to load them onto those trucks.
Each forklift also comes with two RFID tags attached. When an operator picks up loaded pallets, typically two at a time, it then moves to the appropriate dock door and loads the pallets onto the truck. An Impinj Speedway Revolution reader and antenna installed overhead at the dock door by Vilant captures the ID numbers of as many RTI tags as it can, and forwards that data to the Vilant Visibility Manager software. The reader also captures the IDs of the forklift’s RFID tags. The software’s Vilant Engine component identifies the direction in which the tags are moving, and surmises which pallet is being placed on the truck, as well as which forklift is doing the work.
The key to this system, Virkkunen explains, is that a 100 percent read rate of the RTIs’ tags is unnecessary. Although the system is collecting approximately 70 percent of the tag IDs, an even lower percentage enables the Vilant software to determine which virtual handling unit is being loaded at any given time.
If an incorrect pallet is being loaded onto a truck, the forklift driver views a red light on the gate and a warning message on his or her onboard computer screen. In addition, an audible signal warns the driver that he or she is making a mistake.
Each of Migros Ostschweiz’s delivery trucks also has a passive UHF RFID tag attached to it. The vehicle tag’s unique ID number is linked, in the EPCIS software, to the loading list for each store to which it delivers goods. As a truck backs into the dock, the Speedway Revolution reader installed at that location captures the vehicle’s tag ID and forwards that data to the Visibility Manager software, to determine whether the truck has pulled into the correct spot, as well as document the time of day when the vehicle arrived.
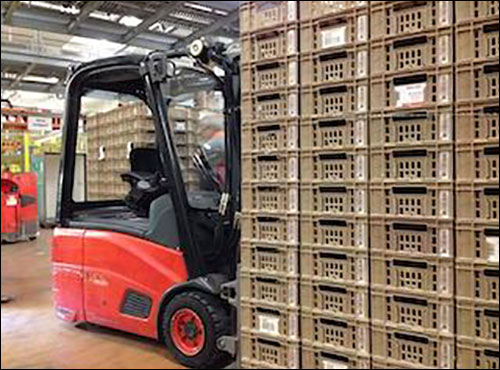
If the truck is in the wrong dock, Migros’ warehouse-management system is alerted, which can then direct reports to the necessary personnel. The system was taken live in January 2014, and has since boosted efficiency and accuracy, by preventing any loading errors.
What’s more, the system provides valuable information related to what has been shipped to a store, as well as when this occurred. For instance, since some busier stores receive up to eight shipments daily, it was not always clear how many of those deliveries have been completed at any given time, and what the deliveries contained. If a store finds that it has run out of fish and knows fish was on that day’s order, Virkkunen says, store managers can log into the system and view whether that fish was already shipped to the store earlier in the day, and thus has been sold out and must be reordered. Management can also determine if the order is still either at the warehouse or in transit, meaning replenishment is imminent. RFID was implemented first at the cold warehouse, Balmer reports, since all of its processes use Migros RTIs, which were already permanently RFID-tagged.
About 1,500 of the daily 6,000 pallets are already covered by the LUIDO RFID system. However, some of the 4,500 RTIs used for shipping non-refrigerated merchandise do not belong to the MGB, and thus are not yet RFID-tagged. “For these processes, certain source-tagging mechanisms have to be implemented, which poses a challenge outside of the actual loading process,” Balmer says. He adds that these source-tagging mechanisms—by which tags are permanently attached to the RTIs—will be further tested before the technology is introduced to the non-cooled shipping process.