- Meeting Customer Requirements with Greater Efficiency
- Finetuning System Hardware and Software
- Planning for RFID Expansion
As audio and video (A/V) rental company Rentex has negotiated its way through the challenges of post COVID-19 pandemic business across the United States, its use of radio frequency identification technology has faced some headwinds around supply chain challenges. But because the technology has been in place since December 2020, RFID has enabled the company’s growth even with the limited labor availability.
Nearly two years after deploying the technology, the company temporarily slowed its fixed RFID reader deployment due to supply chain issues. At the same time, the use of RFID tags on all assets rented by customers has helped Rentex to serve them at times that have been highly challenging. The solution consists of passive UHF RFID tags from Vizinex (an HID company) and Metalcraft, as well as handheld readers from Zebra Technologies and software supplied by Rental Tracker.
When Rentex announced its adoption of RFID technology at all 10 facilities throughout the United States, it was already automating data capture related to the hundreds of thousands of assets it ships out to, and receives back from, its customers (see RFID Raises Efficiency for A/V Rental Equipment). Since then, the company has been deploying approximately 20,000 new tags every few months, and it has benefitted from faster, more accurate processes involving not only shipping and receiving, but also inspections.
The initial rollout involved handheld readers used by employees at each of its sites, says Marcus DeLuco, Rentex’s CTO. But in the future, he notes, the company intends to expand the solution by installing Impinj fixed readers at each facility’s loading ports, as well as building an app and offering low-cost RFID readers to some customers looking to access inventory data about the goods they have rented.
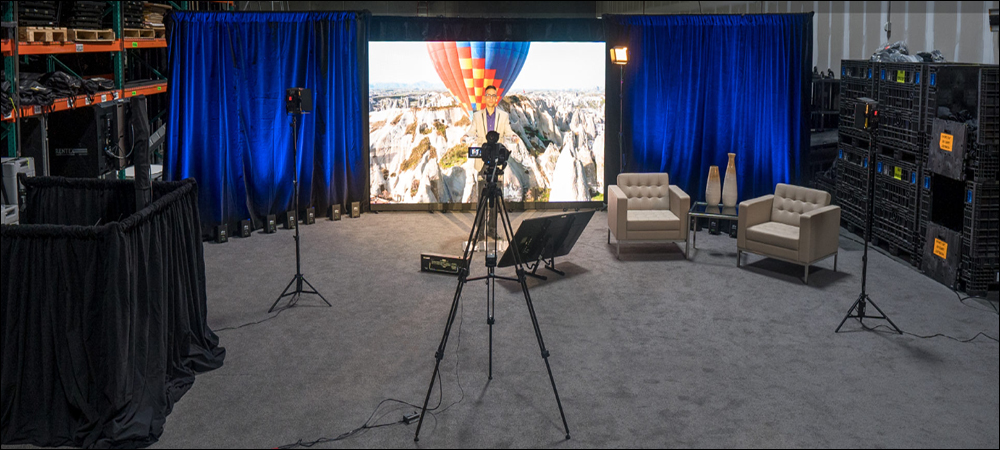
Rentex has adopted RFID technology to track its A/V rental equipment.
Meeting Customer Requirements with Greater Efficiency
It’s been an unusual year in the A/V rental industry. Some companies that provide equipment such as cameras, monitors, computers and projectors went out of business during the pandemic. This has put additional pressure on companies like Rentex, whose equipment is used by production companies, hotels, conference centers and other enterprises that require professional-level audio/visual equipment.
Global supply chain issues have impacted access to some of the equipment that customers rent, and they have also affected the availability of RFID technology, including tags and handheld and fixed readers. Furthermore, the Russian war in Ukraine, with its related energy shortages, has impacted the availability of A/V and computer products coming out of Europe. In addition, a shortage of labor has caused delays in locating, identifying, processing, shipping and maintaining equipment.
That’s where Rentex says it is seeing a benefit in its use of RFID. First and foremost, the technology automates what had been time-consuming processes. As one of the largest wholesale audio and video rental companies in the United States, Rentex previously spent thousands of hours on manual processes every month before it implemented the RFID solution. With or without RFID, once an order is placed, Rentex’s employees assemble rental kits with the items ordered. Without RFID, this was a time-consuming process that typically required barcode scanning and data entry.
These days, workers can use RFID readers to pick items for each other, then capture the unique ID number of each tag while packing the kit, thereby confirming that the order is being properly fulfilled, as well as creating a digital record of what has been sent, when this occurred and to which customers. When goods are returned, the handheld readers are again used to receive those products. The company measured results following the RFID deployment, in one case reducing a 2.5-hour, two-person process to a 15-minute, one-person task. What’s more, Rentex found that it was able to cut a 22-minute check-in process down to only 10 seconds.
Finetuning System Hardware and Software
The company has focused on developing a solution that includes specific tags optimal for each piece of equipment. “We’re always investigating different tag types,” DeLuco says, to address the many asset form factors—from cables to lighting or flat screens—and the material of which they are made. “To perform well, an RFID tag needs to be compatible with the material it’s mounted on.” Tags needed to be sized according to each asset, but also durable for the environment to which rental equipment can be exposed.
Rentex tested its tags by placing one on a metal plate and hitting it with a ball-peen hammer. The tag withstood three high-force blows before it stopped transmitting, HID reports. The force of the blows was significantly higher than anything the tags would encounter during normal use, DeLuco notes. For assets for which it was unclear whether the materials were metal or plastic, the company is using HID’s Sentry Duo universal tag, which is designed to be compatible with any surface. Cable assemblies, a particularly troublesome type of asset to track, were tagged with HID’s Sentry Cable tags, while Metalcraft’s on-metal tags were applied to some other metallic assets.
According to DeLuco, software development has continued as the system has evolved. “We’re always working with our software developer [Rental Tracker] to finetune how the system responds,” he states. In the future, the company intends to assign an individual worker whose responsibility will be dedicated to the RFID program, including its expansion and the testing of the fixed readers.
With handheld readers, Rentex aims to capture inventory audits as well. “We want to be able to sweep the warehouses as fast as possible,” DeLuco explains, capturing at least 85 to 90 percent of all the tags via the handhelds. The sites come with some environmental challenges for RFID tag reads, he says. Assets are stacked on racks as high as 18 feet, for example. Therefore, the company is looking into solutions that could include a forklift-mounted reader that can be raised to that level.
Other challenges include the tag form factors of smaller assets. While RFID tags can be very small, DeLuco says, in some cases they don’t include space for human-readable IDs. Thus, he adds, these tag deployments require the overlay of a paper label. To make such tagging requirements easier, the company has developed a template resource for employees at all of its facilities, for use when applying tags. Each asset type comes with instructions and photographs indicating where tags should be mounted, along with the types of tags to be used.
Planning for RFID Expansion
Initially, Rentex had hoped to have installed fixed RFID readers and antennas by this time, and it has been testing the technology for several months. However, DeLuco admits, supply chain problems have delayed that effort. “We’re still actively working and testing,” he says, “and we have been able to conduct tests with fixed, polarized antennas so they face each other—and they are working really well.” Fixed reader deployments, he says, are still on the company’s roadmap.
At the same time, the RFID technology already in place has provided benefits that have carried the company through many of 2022’s challenges. “We couldn’t do what we’re doing without it,” DeLuco says. Many companies are looking into RFID technology to fill gaps created by labor shortages, he notes, adding, “Fortunately, we were already on the bandwagon. The speed by which we have to process would not be possible without the technology.”
The technology helps to ensure that Rentex makes good use of its existing assets, as replacements are often slowed in the supply chain. For instance, the company operates a missing and damaged evaluation process by which goods are checked when they are returned from customers, and any item not returned with an order is identified, while the received items can be inspected for damage. “Sometimes,” DeLuco says, “customers don’t return their entire order.”
For larger customers, there are times when they simply cannot find missing items. When this happens, the customers could be billed for those assets, while Rentex must order replacements, which could be delayed. With the use of RFID, an alternative is for Rentex to visit the site with a handheld reader. “We’ve been able to use the RFID [reader] in the Geiger counter mode,” DeLuco says, by simply inputting data about missing items and walking or driving around the customer’s warehouse or facility to find them. The reader identifies the assets and can guide users to them.
In the future, Rentex plans to offer an app and customer-facing handheld readers for those wishing to take advantage of the automatic identification capability RFID can provide. The system could include a Bluetooth-based UHF RFID reader that can be connected to a smartphone. There is already interest among some of Rentex’s clients to adopt such a system. “In our customer base,” DeLuco states, “we invite them to our warehouses to let them see how it works.”
Key Takeaways:
- Rentex benefitted from deploying its RFID technology as business grew and labor shortages meant a unique challenge in terms of hiring individuals to track goods moving into and out of its facilities.
- With the RFID system, Rentex can better navigate supply chain challenges and ensure its equipment is available for customers, and that the assets are then returned properly.