Texas A&M has completed a simulation project for a cash courier company to bring visibility to cash movement between banks and businesses, as well as through sortation and counting.
When it comes to asset management, few assets are as important and sensitive as cash – before, during, and after it is transported between businesses and banks in armored courier vehicles. Researchers at The Texas A&M University System have developed an RFID-based solution that automates data capture for cash – where it is and in whose custody – that enables robotic sortation, cuts labor hours, and reduces the duration of truck routes. In fact, according to Lance Decker, researcher at Texas A&M’s College of Engineering, using RFID to track cash can reduce teller labor hours by 79 percent and the transit time of each bag of cash by 43 percent. Decker led the cash management project and designed the solution as part of his dissertation.
The technology-based benefits equated to an average annual savings of approximately $2.2 million after a one-year payback, Decker says, for armored truck carriers (ATCs). The solution consists of an API that enables sharing of RFID-based data between all parties in the cash management ecosystem, as well as fixed RFID readers at sortation sites, in trucks, and handheld readers carried by drivers. An RFID printer could print IoT-enabled labels at businesses where the cash bags originate, and those labels could then be attached to each bag.
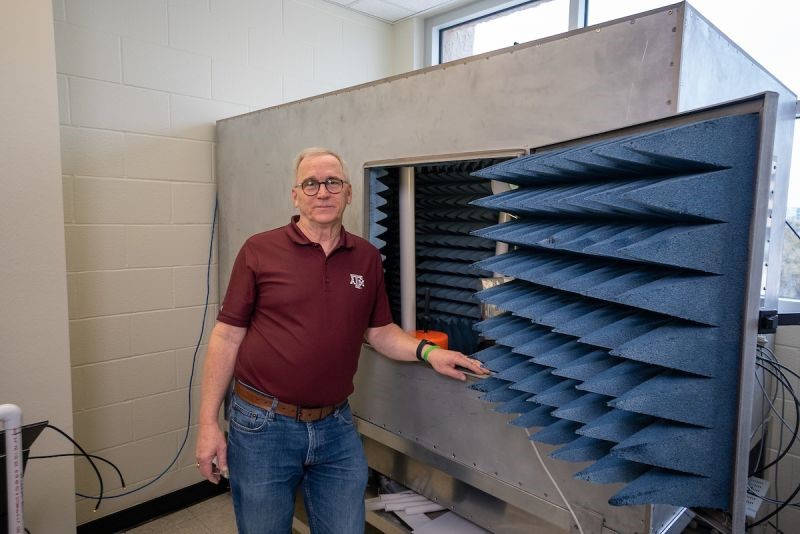
Lance Decker, FMCSA Technology Division Researcher, at Texas A&M’s College of Engineering
Prior to the cash management project, Decker planned to research general cargo traceability by deploying RFID readers on truck trailers rather than at dock doors. “That way you could see cargo going on and off of the trailer anywhere it went,” rather than just at the site where dock door readers are installed. When a large, armored cash courier approached the university to examine how RFID might help them manage their movement of cash, Decker took on the challenge, modifying his initial plan specifically for the transport of cash.
Traditionally, armored cash couriers have been slow to adopt new technologies, and cash transfers are still reliant on paper receipts. Transitioning to something more automated, therefore, requires some faith that data captured by RFID would be as accurate as manual methods. The courier who approached Texas A&M and Decker (whom Decker declines to name) wanted to make moving money more efficient and accurate, decrease insurance costs, and serve clients faster. They were also interested in deploying a robotic sortation system to sort bags of cash according to where the bags were destined. An RFID solution could enable that.
Cash movement is still a large industry. In fact, while cashless transactions and cryptocurrencies are widespread, according to the Federal Reserve, $2.1 trillion in cash is still being circulated today.
To move cash between banks and businesses, a courier conducts a daily cycle – bags of paper cash, checks, and coins are picked up from retailers and banks, then transported to a courier cash managing facility or to a bank or business. The bags of cash are sorted and their contents counted. If a courier service has about 50 trucks making 50 to 60 stops a day, they may be transporting up to 5,000 bags – some with large amounts of cash; others with a single check. Large cadres of tellers working for the courier service companies are charged with counting and confirming the contents of each bag. This includes opening a bag, pulling out a deposit ticket, and making sure it aligns with the deposit. In the manual process, tellers write on the bag to confirm the sorting with full cash amounts. The process is slow, labor-intensive, and prone to errors.
How the RFID Solution Works
Decker developed a solution that has been simulated for effectiveness and affordability. When a bag is filled with cash an RFID tag is printed, and users employ an API to link the tag’s unique ID to data indicating the contents of the bag. This could be accomplished by the courier service, a bank, or a retailer depositing cash in the bank. The data could then be accessible to related parties via a cloud-based or dedicated server. Once the tag is printed and entered into the system, a driver would be assigned to pick up the bag.
The labels would include not only the UHF RFID tag but also a printed human-readable identifier and barcode. No matter how the data is captured, it needs to be readily available, Decker points out. “Resilience is really important to them. They need to be able to operate if all the equipment stops working; they still need to be able to operate in a manual mode.” Drivers can view pick-up and delivery data on an app to make their transit more efficient. For instance, they can view which businesses on their route have cash bags to pick up, and which businesses do not. They can then skip the businesses that have nothing to pick up. In fact, without RFID, says Decker, a driver may routinely stop at places where there’s no bag to pick up, potentially wasting 10 minutes at each site – the driver needs to leave the truck, walk inside, and wait for a manager to say there is nothing to pick up.
The RFID application can also be used to trigger notices to businesses when a courier is approaching their site, based on the driver’s GPS data. The manager can start preparing for the driver’s arrival.
The rollout would include fixed RFID readers mounted inside the truck. Most armored carriers have two access points: a door in the back and another in the front. Readers would be mounted at each access point to capture the tag ID of every cash bag that enters and leaves the vehicle, which could also be married to the GPS data related to where the truck has stopped. With one more antenna mounted inside the truck, the system could also capture real-time data by reading all tags on the cash bags in the vehicle. Once the truck delivers the bags to the courier facility, an RFID reader mounted at the entrance to the robotic sortation system would analyze the bag tags. With this tag ID data, the system can compare the tag data against the truck’s digital manifest in the application (so each bag label is read). If the tag ID matches the expected details, a green light would illuminate and the bag would enter the sortation system. Sorting is done by robot which would eliminate the manual process. Texas A&M’s research team estimates that there would be about a 3 percent error rate in sortation, such as a tag not being read, and the discrepancy could then cause the automated system to screen out that bag for manual checking.
Cutting Time on the Road for Couriers
Decker says their research found a driver’s route – with about 70 stops – could take 12 or 14 hours. With RFID this could be reduced to just six hours. Other savings would include cutting the cost of fuel due to less driving and idling at customer sites. The benefits beyond efficiency and reduced errors could be the transparency between members of the cash supply chain. If the courier service uses the RFID solution, they could share the data with banks and businesses whose cash is being managed. The research has also included capturing RTLS data with an RFID tag applied to the bins in which bags are transported around a warehouse or distribution center. The active tag provides real-time location data from the bin, which could then link to the RFID tagged data from each bag’s label.
The system also potentially aids in the management of teller trash, Decker says. Bags that have been emptied of money are typically stored for days so that they can be accessed again if a mistake is discovered (such as a missing check that could have been misplaced in a bag). With the RFID tag on each bag, individuals could use a handheld reader to easily locate the right bag within a storage area filled with such refuse. The solution can leverage off-the-shelf RFID readers, says Decker, including those from Zebra and Impinj. In general, says Decker, the simulation centered around the higher priced hardware, including the price of RFID labels at 10 cents each. In that way “when we applied the math we could give the most conservative view of what it would cost.”
“The research’s fundamental hypothesis is that adding IoT technology to the cash movement ecosystem reduces costs, improves capacity, and provides visibility to all parties involved in the cash movement,” says Decker. He has discussed the research and the API integration that was developed with RFID technology at conferences around the US this spring and summer. He says he hopes companies could then pick up the efforts to take the study to proof of concept and build a solution.
Key Takeaways:
- Texas A&M project has found that the cost of an RFID system to manage the transfer, counting, and sortation of cash could yield a significant return on investment in a year.
- The technology with fixed and handheld RFID readers, tags on money bags, and software API, was built in simulation and the researchers’ hope to see the technology tested in the field.