Scientific institutes typically have a complex system for providing materials to researchers whose work is funded by grants. Because researchers need a variety of goods—ranging from an $8 box of latex gloves to chemical compounds valued at thousands of dollars—and must bill the grant supporting their research, most institutes and universities must staff a storage area with someone who can record and authorize every transaction. An alternative to this method is an automated system consisting of locked cabinets that can utilize biometrics, radio frequency identification or both, in order to provide goods to authorized individuals and create an invoice for the appropriate party.
The Stowers Institute for Medical Research, located in Kansas City, Mo., conceived of an RFID solution that was then created by automated inventory-management technology firm Terso Solutions. The system consists of an RFID-enabled store at which individuals can shop for and select the products they need, and then make their purchases. The system was taken live in late September 2012 at the institute’s Kansas City campus. Terso is now marketing that solution, known as Smart Stockroom.
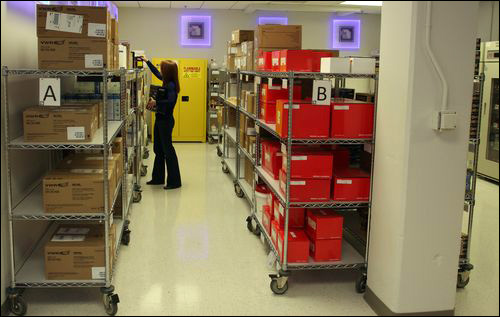
The Stowers Institute employs 350 scientists, each of whom utilizes a variety of tools while investigating the causes, treatment and prevention of diseases. Those tools include reagent test kits, containers of chemicals used in experiments, and compounds made onsite for specific uses.
Until this year, the institute had a biometrics-based locked cabinet solution provided by Cardinal Health. At any given time, 24 hours a day, researchers could access a bank of locked cabinets and gain access to the items stored within. After undergoing a fingerprint scan, an employee would use the touch screen to select the desired product, thereby unlocking the door to the appropriate cabinet, where that individual would then find what he or she needed and request that it be billed to the appropriate grant. The team liked the system, says Jessica Witt, the head of research systems for Stowers’ Resource Management division. Researchers were pleased to be able to access the goods they required 24 hours a day, seven days a week, she explains, since it did not require a staff member onsite to manually provide the tools and create invoices.
The Cardinal Health system, however, would no longer support integration with the institute’s Oracle system, so Witt began investigating other solutions. She had seen an RFID-based convenience store at a Florida airport, and considered adopting that concept. The institute approached Terso Solutions, which offers RFID-enabled cabinets to the health-care industry, with the idea of obtaining a storage room that could act as a store for researchers, allowing them to browse through the available goods to find what they seek, perform comparison shopping, make a purchase via RFID technology and then have their grant provider billed.
Terso Solutions developed a system consisting of EPC Gen 2 passive ultrahigh-frequency (UHF) RFID tags, a printer-encoder and three RFID interrogators, as well as software that tracks each read, links the read data with billing and inventory management, and forwards that information to the Oracle system. The Oracle solution orders replenishment when necessary, and also forwards invoices, says Keith Hoffman, Terso Solutions’ director of marketing.
To date, Terso and the Stowers Institute have attached tags to a total of 3,500 goods. The deployment, Hoffman says, utilizes a combination of various RFID tag models supplied by Avery Dennison and Alien Technology.
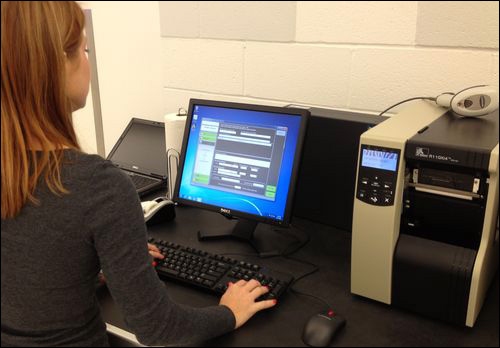
First, the tags are encoded on a Zebra Technologies R110Xi4 printer-encoder, at what the team has dubbed an association station. Each tag’s unique ID number is linked to details regarding the product to which it is attached, including the lot number, manufacturer and expiration date. The system also stores that item’s location within the storage room—specifically, the location’s rack and shelf numbers. The product data is saved in the Terso software and is forwarded to the Oracle system, after which the products are then placed within the storage room according to their assigned locations.
Upon entering the storage room to procure an item, a researcher must provide a fingerprint at the checkout station in order to access the system and gain authorization, and then scroll through products to indicate the specific items being sought. The software directs that individual to the proper rack and shelf, and he or she can then peruse the goods on the shelf, compare prices and make selections. The user then takes the items to the checkout station and places them on the counter, under which is installed a Motorola Solutions FX9500 RFID reader. That device captures the product tags’ unique ID numbers and supplies that information to the software, which displays a list of items on the touch screen for the user. Once the researcher selects the grant to which the goods are to be billed, and approves the items being removed, the software forwards the list, pricing and billing recipient to the Oracle system, which sends out the invoice.
Once this is done, the user can take the items and walk out the door, where two more Motorola FX9500 RFID readers are installed on the ceiling. The individual can choose to turn left or right while exiting the storage area, in each case passing a set of two reader antennas on either side of the wall. If the reader captures a tag ID that was not among the items purchased, the software triggers a light stack to illuminate a red light, warning the individual that he or she is removing something that has not been purchased. Simultaneously, the software sends an e-mail alerting management of the error.
The storage room contains not only goods placed on metal shelving, but also some temperature-sensitive items within approximately 13 refrigerators and freezers, as well as a storage unit for flammable materials.
The technology provides several benefits over the locked-cabinet solution, says Laura Perin, the Stowers Institute’s head of contracting and procurement. Not only does it reduce shrinkage that previously resulted from items being removed, often mistakenly, from cabinets without being purchased, but it also enables the facility to increase merchandise diversity for the scientists. Perin says she can purchase goods in higher quantities, thereby receiving better price discounts, and the solution can provide several product options that scientists can compare while making purchases. The system alerts the institute’s management when inventory drops below a specified level, and when expiration dates are approaching, thus helping the institute ensure that its inventory is reordered on time, and that goods are used prior to expiration.
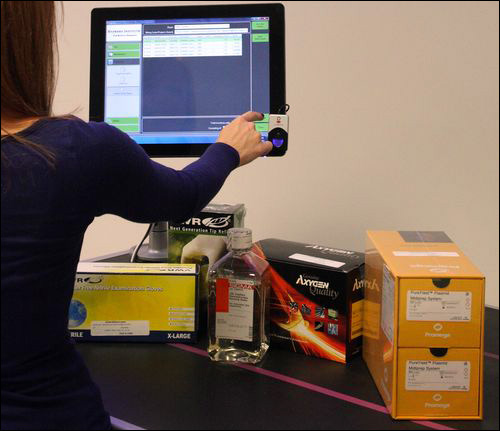
However, Witt notes, the primary benefit to date has been the improved convenience for researchers. “They love it,” she says. “Checkout time is faster.”
According to Hoffman, Terso Solutions will offer the system commercially, including to some of its existing customers, as well as to those of its parent company, Promega.