Johnson & Johnson Supply Chain (JJSC) has built a real-time data-capture solution across its supply chain for orthopedic surgical loaner sets in Japan, using passive UHF RFID technology. JJSC, which has been selected as a finalist for the 2020 RFID Journal Awards, conducted a pilot of the system it has now implemented, and found that it has provided an 80 percent reduction in labor time (in comparison to manual barcode and visual scanning), while exception handling is now 70 percent faster. The company opted to build the solution using GS1-standard, serialized RFID tags that were read on first pass with 99.96 percent accuracy.
The technology solution that JJSC piloted has accomplished more than just a reduction of labor, says Blair Korman, JJSC’s senior project manager, who leads compliance efforts and an RFID initiative to standardize tagging operations. It proves that a standards-based approach can be used across our supply chain, Korman explains, as well as across other businesses in the healthcare industry, including with the company’s customers and suppliers.
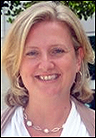
Blair Korman
The result is a standardized rollout of RFID solutions for healthcare products and pharmaceuticals. The pilot and subsequent deployment have taken place at four sites in JJSC Global Orthopedics distribution centers in Japan, and the firm is now gaining support from other companies in the Japanese medical device industry to pilot or deploy similar solutions.
JJSC includes three Johnson & Johnson supply chains: consumer health, medical devices and pharmaceuticals. By the time it launched the pilot, the firm had already completed numerous RFID projects in the past years using the technology to manage inventory in certain supply chains. When JJSC received a request from a hospital for RFID-tagged orthopedic loaner sets, Korman says, “We launched this latest pilot at our Japanese distribution centers. But we did so by leveraging the GS1 EPC UHF Gen 2 air-interface protocol, keeping an eye on the long-term future.”
By implementing GS1 standardization, Korman notes, the solution could provide benefits for the hospital customer requesting it, as well as for other members of the supply chain, with a potential solution that it could scale to multiple customers or to the industry as a whole. Basically, she says, “We created a technology framework to use in future RFID projects.”
Healthcare product supply chains are becoming increasingly complex, JJSC has found, and its goal for any RFID solution is to ensure that drugs and medical devices can be traced back to their original source, while reducing packing times and providing 100 percent inventory accuracy. By providing a unique ID number for each item, the system can confirm the authenticity of products for those who use them, thereby preventing counterfeit goods from entering the supply stream.
With regard to the pilot at its Japanese Global Orthopedics DCs, the company wanted to learn if RFID could properly track a loaner set, along with the hundreds of sterile packaged items inside it, as they were shipped to hospitals and then returned after a procedure if they were not used. Typically, when an orthopedic procedure is scheduled, surgeons cannot know exactly which parts they need until the operation is underway, so they employ a set containing hundreds of tools and implants that might be used during surgery, such as a knee replacement.
In a single set, some items may be used, while others may be returned for use in another procedure. At the DC, as the sets are returned from hospitals, as well as after they are packed for loaning again, they are carefully inspected by JJSC’s staff members. This process, which the company calls “packing manual checks,” is traditionally performed manually and visually. A worker opens a kit, views all items within, ensures that they are still properly enclosed in sterile packaging and then counts those items to reconcile the numbers against the hospital’s report of what has been used.
With RFID, that process becomes automatic, although a manual visual check for the condition of the packaging still takes place. When products are received at the point of import, JJSC personnel encode and print standard GS1 UHF RFID tags, which they then attach to the packaging of each item packed in a loaner set for use in orthopedic procedures at area hospitals. A tag is also attached to the exterior of the set itself. The tag ID and information about the products contained within is stored in JJSC’s software.
Every tag includes the serialized Global Trade Item Number (SGTIN) within the EPC memory bank, as guided by the GS1 Tag Data Standard (TDS). JJSC leverages SAP’s Advanced Track & Trace for Pharmaceuticals to manage the serial numbers specific to JJSC. To meet the standardization demand, the company did not use any specific tag or vendor. However, some customization was required for the tag design to suit the form-factor requirements on device packaging.
The tagged products are moved through an RFID tunnel reader that captures tag reads of all the items within a set, linked to the set’s tag ID. JJSC integrated the new software, designed to accommodate the encoding process, with its existing loaner set software to view each item’s status as it is read. The loaner set replenishment area of the DC was integrated with the RFID equipment.
Each time a loaner set is received or shipped to a hospital, the set is moved through the tunnel reader, with data updated in the system to confirm what has been received and what has been shipped. The company’s employees still visually confirm each item inside the set is properly sealed inside its sterile packaging.
Korman says the pilot found that the RFID technology overcame any challenges related to the speed of tag reads or background noise that could interfere with transmission. The team was able to deliver the required accuracy and meet performance parameters, she reports. The pilot was completed after six months, and the permanent deployment was in place 18 months later, in mid-2019.
Because the system adheres to GS1’s standards, Korman says, it can be easily deployed across other supply chains. In the past, she states, “One of the obstacles we found with adopting RFID was that there was no readily available standard solution that could work in the end-to-end supply chain.” The new deployment can serve as a template for other systems, she says.
Since JJSC created a GS1-guided standardized tag, Korman says, “We are passionate about sharing the benefits of RFID labeling use with our customers.” The future, she adds, includes end-to-end supply chain utilization. JJSC now has other projects around the world using the same GS1 global standard.
All JJSC distribution centers in Japan are now live with RFID for their process of loaning orthopedic sets to area hospitals. According to Korman, additional sites throughout the world are now adopting the model, with some pilots completed and with full go-lives scheduled for later this year. With the technology for monitoring orthopedic loaner sets, inventory will be packed and processed more quickly and without errors.
While hospitals receiving the sets from the Japanese DCs are not yet using the RFID tags for their own purposes, Korman says, with the adoption of the GS1 standard approach to RFID, she expects the end-to-end supply chain to more readily adopt the technology. That, she predicts, will provide wins for patients resulting from reduced costs, improved visibility and improved product security.