For decades, drilling companies have experimented with various technologies to control tools that are part of oil and gas wells, employed thousands of meters beneath the surface. Many of these technologies, however, fail to work reliably considering the high pressure, corrosive environment and high temperatures within the wells.
Now, a Scottish company known as Petrowell has designed and patented a system that uses radio frequency identification to communicate wirelessly with valves and other downhole oil well tools. The system can help oil companies extract the maximum amount of oil and gas from fields, the company reports, by depleting the resources in a strategic way.
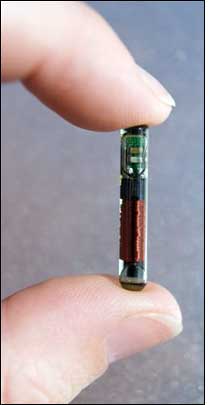
Typically, thanks to what is called directional drilling, an oil well can have both vertical and horizontal sections. A company bores down vertically, then turns its drill bit 90 degrees and digs horizontally from the lowest vertical point. A well may reach 3 to 4 kilometers (1.9 to 2.9 miles) in depth and 10 kilometers (6.2 miles) in length. Fluids flow out of the well, but despite that outward and upward flow, businesses can also introduce fluids and small objects into a well’s depths from the surface. Well operators often need to send acid down the hole to bore through rock, for instance. The construction of a well and the flow of fluids allow this to occur.
This directional drilling is cost-effective, given the lack of large, untapped reserves remaining worldwide. With wells that extend horizontally, companies can link up small, unconnected patches of oil or gas, and avoid drilling new wells. In other words, the firms can link up six to 10 pockets of oil in a single well, instead of having to drill six to 10 different holes from the surface to reach those patches.
If all of the oil or gas is depleted from the patches located along the vertical area of the well before those along the horizontal section, the company may not be able to extract the maximum amount of oil or gas from the horizontal part, according to Daniel Purkis, a Petrowell design engineer. During the past five years, the company has been developing and recently began selling RFID-based downhole tools that can be operated from the surface to address this particular problem.
According to Purkis, oil and gas flows first from a well’s heel—the vertical portion, and the point at which the bit turns 90 degrees. If oil from the heel becomes depleted, the well will begin producing water, thereby choking off reserves from the toe—a well’s horizontal section.
“It costs 50 to 100 million pounds [$72 million to $143 million] to drill a well in Angola,” Purkis says. “If, after a month, the well produces only water, it’s a big problem.”
By controlling the valves along a well’s vertical and horizontal sections, companies can first deplete reserves at the farthest horizontal point first, then work back toward the vertical portion, thus keeping water from blocking oil flow. If tools cannot be controlled reliably from the surface, this sort of timed and strategic depletion is not an option.
Some systems do exist for controlling tools in the hole, but Purkis says the industry considers them unreliable. Hydraulic lines are one common means of controlling tools.
“It’s like operating brakes on a car,” Purkis states, adding that the hydraulic lines may need to be up to 20,000 feet long, and that such lines are expensive and prone to damage. In addition, if a well has six tools that need to be controlled, then six hydraulic lines are required—one for each tool.
Another option features electrical cables, also up to 20,000 feet in length. These cables are expensive, Purkis says, because they must be able to survive the corrosive environment and high temperatures found in the well, and are prone to failure.
Additionally, both hydraulic and electrical cables attached to downhole tools require control boxes and generators at the surface. “On an oil rig,” Purkis states, “floor space is at a premium.”
Petrowell, on the other hand, has devised a system that employs downhole valves and other tools outfitted with RFID interrogators. Operators introduce passive RFID tags into a well’s downward fluid flow, and the tags pass through the readers, providing the appropriate tool instructions.
In Europe and North America, Petrowell carried out multiple tests with Marathon Oil Co., which helped develop some of the technology and is a partner on several of the patents. During those tests, Petrowell mounted a battery-operated RFID reader onto a single valve. Operators placed handfuls of loose, glass-encapsulated RFID tags into the well, which flowed down vertically and out horizontally, communicating with the interrogator as they passed through the valve.
“By controlling valves,” Purkis explains, “the system equalizes the flow of oil across the reservoir so that we get more oil—and get it quicker.” The tags deliver command code messages to specific tools in the hole, and the codes instruct specific valves to take no action, or to take action, such as opening or closing a particular amount. “The message to tool number six may be ‘shut’ or ‘open’ or ‘close 10 percent,'” he says.
According to Purkis, the system is designed in a redundant fashion—multiple tags encoded with the same instructions are thrown down the hole—in case some of the tiny RFID tags are unreadable, or break once inside the hole. In addition, checks are built into the system so that once a tag passes through a valve, it cannot pass back up through that same valve and cause unwanted reactions from the tools.
“The worst thing that could happen,” Purkis says, “is a rogue RFID tag makes its way through the system and activates a tool it shouldn’t, or at the wrong time. This could cause a blowout condition, and then a fire.” To keep this from occurring, and to gain the necessary security permits, users encode time and sequence stamps onto the RFID tags before they are dropped into the hole. In this way, the tags’ commands expire after a specified period of time, and the interrogators react only to new tags. Once the tags reach the end of the well, they become lost there, or else embedded in the rock.
The tags measure either 4 millimeters (0.2 inch) in diameter and 24 millimeters (0.9 inch) long, or 2 millimeters (0.1 inch) in diameter and 8 millimeters (0.3 inch) long, and are purchased from Texas Instruments and modified by Petrowell. They are inserted into the well by hand, though the company is currently designing a tag injector that would put them in automatically.
Read rates are determined by how fast tags travel down the hole, Purkis notes, and by the amount of flow turbulence. The read rate averages approximately 60 to 70 percent for a single tag, but operators can insert 10 identical tags simultaneously to raise the rate to nearly 100 percent. For instance, operators send down 10 tags containing an instruction to “close valve six by 5 percent.” The change in valve settings, he says, is obvious in the flow at the top of the well.
During the commissioning phase of an oil well, when systems are being set up and tested, Purkis expects operators to drop swarms of RFID tags three to four times a day, in order to adjust settings. Later, when wells are in production, tags may be sent down the hole once each month, or only as needed, for valve adjustment.
Prototypes of the system are currently in operation, Purkis says, though he declines to reveal which companies tested them besides Marathon Oil. He does indicate, however, that the RFID system was recently shipped to a firm in Canada, as well as to integrated international petroleum company Saudi Aramco.
What’s more, Purkis adds, one major company is presently considering implementing a system to communicate in the other direction—from downhole tools to operators at the top of wells. That firm wants to monitor heat and pressure within the wells, as well how fast fluids flow.
The basic concept is that tools loaded with a large number of RFID tags would be placed into the wells. The battery-operated tools would also be equipped with pressure, temperature and flow sensors. The tools would encode a tag with data recorded by the sensors, then release the tag into the upward flow. At the surface, the tag would pass another interrogator, which would read the information encoded on the tag.
With several such devices in the hole, operators could analyze the amount of oil coming from each section, and how fast it flows. That information, the company indicates, would help operators drill more precisely the next time the same well was tapped.
“We are using RFID in a unique way,” Purkis states. “Our partners say it will change the way oil wells are drilled and produced in the future.”