At the container terminal operated by Total Terminal International Algeciras (TTI Algeciras) at a Spanish seaport on the Strait of Gibraltar, radio frequency identification and real-time location system (RTLS) technologies provided by Identec Solutions are employed to track the locations of shuttles that drivers use to carry containers to and from vessels, thereby ensuring that the vehicles place the containers in the proper location, and that they are not at risk of colliding with other equipment. Both functions are critical, because some of the equipment that helps move the containers into and out of the terminal’s transfer site is unmanned. In fact, the shuttle drivers are some of the few people on site.
TTI Algeciras describes its facility as semi-automatic—in other words, software controls which containers go to which location, using a combination of technology. While drivers operate the shuttles, they follow instructions from software that also controls the movements of the unmanned moving cranes, known as rail-mounted gantries (RMGs).
The company utilizes terminal operating system (TOS) software provided by Cyberlogitec to track the locations of 20 terminal shuttles as containers are unloaded from vessels, then are staged and reloaded onto other vessels or trucks. The Cyberlogitec software uses location data derived from RFID and Differential Global Positioning System (DGPS) technologies. In addition, the software uses DGPS data to locate the RMGs, and subsequently the containers they carry.
The TOS software also utilizes DPGS data to help the terminal operator track each vehicle’s location. However, DPGS units do not function under every condition. The large steel cranes and RMGs can obstruct satellite transmissions, making RFID technology necessary in order to ensure a shuttle never falls out of view of the software.
TTI Algeciras, owned by South Korean firm Hanjin Group, was built at the 81-acre Port of Algeciras in late 2009, with the company’s RFID-based Transfer Point Management (TPM) system going live in May of this year. It took a mere five months from planning to full implementation, the company reports.
When a vessel is unloaded, a fixed crane fitted with a DGPS unit removes each 40- or 20-foot container, and a camera photographs the ID number printed on its side. Global control system (GCS) software, provided by Hi-Tech Solutions Europe, uses optical character recognition (OCR) to identify that container’s ID number, and utilizes DGPS data to determine its location. GCS then forwards that information to the Cyberlogitec software, residing on TTI Algeciras’ back-end server.
The terminal operating system then transmits directions for a pick-up by a manned shuttle vehicle. Each shuttle’s roof is fitted with a DGPS unit, and the vehicle is also equipped with a computer, on which the driver can view a list of containers that need to be picked up, as well as where they are located. The onboard computer receives data from its on-board DGPS unit, and sends that information to the GCS software in real time. When poised to pick up a specific container, the shuttle is positioned under a fixed crane that can block the DGPS signal. For this reason, the vehicle also has an active i-Q350 RTLS tag, provided by Identec Solutions, attached to its top. Each of eight fixed cranes has four Identec iSAT RTLS readers mounted at its base—one at each of its supporting legs—and each shuttle’s tag transmits a unique ID number at 868 MHz to the iSAT readers, using a proprietary RF interface.
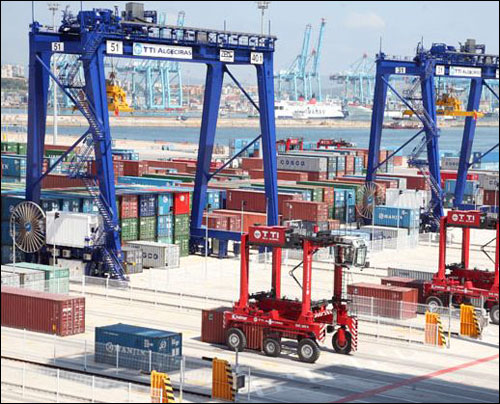
The readers forward that information, along with time of flight (signal rate) data, to Identec’s RTLS position engine software, via cabled connections. The software calculates the shuttle’s location, and that position data is sent to the Cyberlogitec software, which compares the shuttle’s location with that of the container already stored in the software, then confirms that the vehicle is retrieving the appropriate container, and issues approval to engage the spreader mechanism on the shuttle picking up the container.
The shuttle driver then delivers the container to a transfer area, consisting of lanes in which containers are stacked up to three or four high, with RMGs picking up containers that were deposited by shuttles, and placing them in locations assigned by the software system. In addition to the RFID tag on its roof, each shuttle also has four separate active Identec i-Q350 RFID tags—four are used for the sake of redundancy—fixed with bolts to its undercarriage at each corner. These tags are used to help locate the shuttle at the transfer area within a matter of a few feet. While carrying the container toward the transfer area, the shuttle passes over a series of Identec loop antennas, installed in manholes in the ground. Each loop (there are approximately 400, located in and around the transfer area) transmits a 125 kHz signal that excites all four tags, instructing each tag to transmit its information. Each loop antenna also transmits its own ID number. The shuttle’s four tags then transmit their own unique IDs, as well as the ID encoded to the signal transmitted by the loop, to any of the 40 Identec readers within a read range of about 500 meters (1,640 feet).
In this way, the loop ID number linked to the shuttle’s ID provides the vehicle’s location as it moves in the vicinity of the transfer area. It is critical to know each shuttle’s location in real time while it is in the transfer area, since RMGs are at work at that site, lifting containers and placing them in stacks to await shipment. Not only must the TOS know exactly where the shuttle placed the container—in order to ensure that the correct container is picked up and stacked in the assigned location by the RMG—but it must also ensure there are no collisions between the RMGs and the shuttles.
The Cyberlogitec software compares the shuttle’s identity with that of the container it should be transporting, as well as that container’s intended location data. If the vehicle is determined to be entering the correct area, a green signal flashes on the driver’s on-board computer screen, and the shuttle driver can then proceed. If a red signal is flashed, however, the driver knows he is attempting to enter the wrong area, or that the potential for a collision exists. When the driver then places the container in its assigned block, the RTLS data and the DGPS information from the shuttle are compared with the container’s planned location, and if that location is correct, the spreader is engaged to release it. While leaving the area, the shuttle again passes over a series of loop antennas, and its tags transmit their data to an interrogator, thereby enabling the system to know that the vehicle has left the transfer area.
The terminal can move 32 containers onto or off of a vessel per hour, says Oscar Pernia, TTI Algeciras’ processes, systems and innovation team leader, thereby keeping the expense of moving and storing the containers to a minimum. “This system combines productivity and reliability with manpower optimization,” he states.
The TOS software also plans the best location for each container, based on the particular vessel or truck in which it will need to be loaded.
In the future, the company intends to expand the system to include trucks that transport those containers inland. In that case, Pernia says, a driver entering the port would first sign in with his or her ID number, and would then be given an RFID-enabled ID card to carry in the terminal, linked in the software to that individual’s identity. The system would thus know where the vehicle is located, when it has been loaded and when it leaves. In addition, the company is expanding the terminal itself, adding 91 acres of port service area to the existing terminal, which will also include the automated system.