Tudespensa.com (Your Pantry), a Spanish online supermarket, delivers food, household cleaning supplies, toiletries and other products to customers throughout Spain, from its central warehouse located in Madrid. To ensure that the high volume of goods are delivered quickly, and at the scheduled time and place, its warehouse employs radio frequency identification to help it load ordered goods into the proper delivery vehicle and in the correct sequence, according to Jose Vicente Caballero, the logistics manager of DLR, a provider of controlled temperature-storage and order-picking services. The solution, supplied by RFID Dipole, includes passive EPC Gen 2 ultrahigh-frequency (UHF) tags affixed to reusable totes that travel to customers, as well as to suppliers, that are tracked via readers at the dock doors. Dipole’s RFID software suite collects and stores read data on Tudespensa’s database, and shares that information with the company’s Microsoft Navision enterprise resource planning (ERP) system.
Spanish customers who lack the time or transportation to shop can order goods online. Tudespensa will then deliver the ordered items in cooled vans within 24 hours, if so requested by a customer.
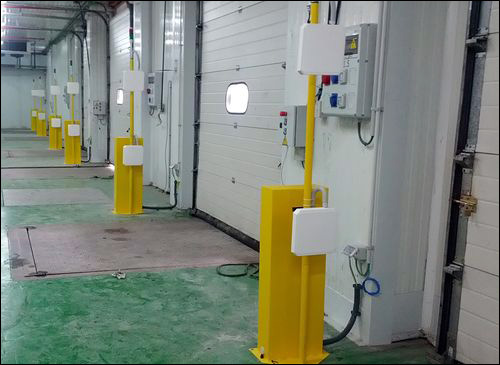
Tudespensa’s warehouse manages two types of orders: normal flow and tense flow. Normal flow consists of groceries, as well as beauty and cleaning products, stored within the company’s warehouse. Tense flow products include fresh goods—such as fruit, meat, fish and vegetables—that are received by the warehouse on a daily basis and are very quickly loaded directly into customers’ orders. The products arrive from suppliers in Tudespensa’s plastic totes, which are typically unpacked, and are then repacked with goods for customer orders, after which the reloaded tote is transported to the customer’s door and back to Tudespensa.
Customers place their shopping orders on Tudespensa’s Web site, choosing a delivery time for the order within the 24-hour period. The firm’s dispatching staff categorizes the orders according to delivery time and geographic location, and then assigns them to delivery vans, to be loaded in a specific sequence that follows the delivery route. In this way, drivers can simply remove each order from the back of the vehicle, rather than having to search for the correct goods at every delivery point.
When an order is placed, the company orders its “tense” items, such as fresh fruit or meats, while automated equipment begins picking goods already stocked (normal flow items) and placing them in plastic totes on dollies, in an automatic process known as “dolletyzing.” The entire process takes place under controlled temperature, Caballero explains.
When Tudespensa receives tense flow goods, they are dispersed to the proper orders via voice-guided devices, and are also placed into totes and stored in a cooled staging area until all of a delivery van’s orders are completed. From that point on, they can be dispatched and loaded into vans, ready for delivery.
At the customer’s home, the goods are removed from the totes, after which the empty totes are returned to Tudespensa.
To ensure that mistakes are not made during this automated process, RFID tags on each tote help the company to track which order has been filled and when each tote is loaded onto which vehicle. The company attaches Smartrac Frog 3D tags to the plastic totes in which goods are delivered, which are then returned to Tudespensa and also can be sent to its product suppliers. The company has installed Impinj Speedway Revolution R420 readers at dock doors, in order to read those tags as the totes are shipped out and again as they return.
“We started working with Tudespensa in September 2011, and the project was finished in May or June 2012,” says Santiago Depares Aguilar, RFID Dipole’s commercial director.
RFID Dipole created a solution able to ensure that all orders were loaded onto the correct vehicles, and to then track when those goods were delivered. A Frog 3D RFID tag was encoded with a unique ID number that was also printed in the form of a bar code on the front of the tag, which was then attached to the tote. That ID number is stored in the RFID Dipole software. When the automated picking equipment fills an order (whether from the normal or tense supply), the tote’s bar code is scanned automatically as the goods are placed into it, thereby linking the tote’s RFID number with that specific order.
Once the tote is shipped to a supplier, it passes through an RFID reader portal at the dock door, with a single interrogator connected to a total of four Impinj far-field antennas—with two antennas mounted on a pole on each side of the dock door. The device forwards the ID number to Dipole’s Middleware RFID Data Suite, which translates the read data and uploads it to ERP software on an SQL database, thus indicating through which door the tote is passing, in which direction it is moving and onto which vehicle it is being loaded, based on data stored in the company’s ERP software. The software also stores such information as in which sequence the totes should be loaded into the vehicle. In the event that goods are being loaded in the incorrect sequence, the system sounds an audible alert and a light flashes a warning for delivery truck drivers and warehouse management. The same process occurs if an unexpected tote, or dolly full of totes, is being loaded onto a vehicle, thereby allowing management to stop the process and correct any errors.
Members of the delivery staff carry bar-code scanners, with which they scan each tote’s bar code as the goods are delivered. When the tote returns to Tudespensa’s warehouse, the portal reader interrogates the tote’s tag once more, and the ID number’s status is changed to returned, indicating it is available for reuse. If a problem occurs, and if the tote had not been properly delivered (for example, if the customer is not home), the tote is separated, an exception is created in the software, and all totes related to that exception are passed through the RFID reader portal.
Once the empty tote is shipped to the supplier and is then returned loaded with goods, its ID is read again and the software is updated accordingly. This information helps the company track its returnable assets, thus ensuring that it receives its totes back, while also providing data regarding the number of totes on hand at any given time, as well as how many are at suppliers’ sites.
The solution consists of six gates that typically read data collected from 400 totes and dollies per hour. A total of 20,000 totes have been tagged to date. In the future, the company reports, the system is expected to be expanded to eight gates. “This system is providing not only the closed-loop control functionality required in reverse logistics,” Caballero states, “but the speed that allows us loading in tight time-windows to satisfy customer deliveries on time.”