Norsk Resirk, a nonprofit Norwegian company that processes discarded plastic bottles and aluminum cans, has completed the first phase of a plan to utilize passive ultrahigh-frequency (UHF) RFID tags and readers to improve its management of recyclable materials. Initially, the firm is reading RFID labels attached to plastic bags containing the recyclables at one of its plants. The long-term goal, however, is much more ambitious: to have the tags read by bottle- and can-collection sites at the point at which the bags are filled, interrogated again by truck drivers transporting those bags, and finally read a third time at all three of Norsk Resirk’s plants. In that way, the company will be able to know when and where empty bottles and cans are picked up and delivered, in addition to who may be responsible if the recyclables fail to reach their destination. Norsk Resirk launched the system at its Alnabru plant as a pilot project, and plans to install the same technology at two other plants, located in Trondheim and Bjerkvik.
When buying bottled or canned beverages, a customer pays a deposit on each container. Upon returning the empty containers to a retailer, the consumer receives a refund of that deposit. Annually, grocery retailers and kiosks collect enough of the bottles and cans to fill 200,000 plastic bags, each of which can hold an average of 250 units. The filled bags are sent to Norsk Resirk’s plants for processing, and the retailers receive reimbursement from Norsk Resirk, based on the amount of product provided. By reading RFID tags on those sacks as they arrive at the Alnabru plant, the firm saves thousands of dollars by better knowing how many bags were received, and from whom, and then paying users accordingly. The RFID-based solution is provided by ACT System Skandinavia.
Recycling has increased via the country’s deposit-refund recycling program—and, therefore, so has business at Norsk Resirk. The organization’s third-party logistics provider dispatches trucks to pick up the plastic sacks after they are filled, and Norsk Resirk sought a way to gain visibility into when the processing plant received those sacks. Bar-coded labels attached to sacks could be scanned when the recyclables were received, explains Martin Ludvigsen, Norsk Resirk’s logistics and operations controller, but this process was labor-intensive, and the company hoped to be able to save time.
The plant receives several hundred thousand recyclable cans and bottles daily from various deposit points (DPs)—stores or other sites where the empties are collected. Approximately 3,700 sacks filled with bottles and cans arrive from “reverse vending machines” at grocery stores, while another 2,500 sacks come from kiosks or gas stations. Bags filled with recyclables sometimes end up missing, or are delivered to the wrong plant, thereby making it difficult for Norsk Resirk to verify the amount invoiced by the DP sites.
With the ACT solution, Norsk Resirk registered each DP in its own software, and sent plastic bags and labels with embedded EPC Gen 2 UHF tags, in order to identify each bag. North Resirk is currently using MiniWeb tags provided by UPM RFID (now owned by Smartrac), with chips manufactured by NXP Semiconductors.
Whenever a DP requires additional sacks and RFID labels, it can contact Norsk Resirk by signing into Norsk Resirk’s deposit-reconciliation system via the Internet and entering the number of labels to be ordered. The company’s RFID software collects the information from the deposit-reconciliation system and prints out a two-part label. One part comprises an RFID label encoded with a unique ID number and printed with a bar-coded version of that same ID, while the second consists of a receipt for that DP. Norsk Resirk then ships the plastic sacks and encoded RFID labels to that specific location.
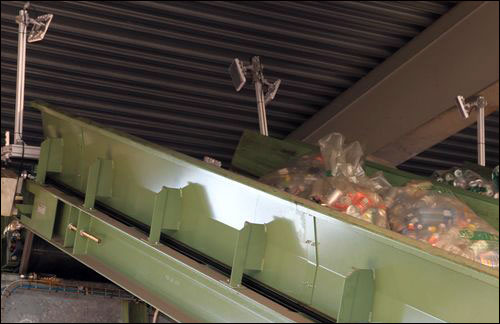
The deposit point’s operator fills the bags, attaches an RFID label to the surface of each bag—or to the plastic tie used to cinch it—and places a request for pickup. Upon picking up the bags, the third-party carrier’s truck driver manually notates, on his or her own paperwork, the number of bags being transported. The DP operator tears off the receipt half of each bag’s RFID label and keeps it for his or her records. Because the RFID tags were printed at Norsk Resirk to meet that DP’s order request, Norsk Resirk’s software knows how many bags it expects to receive, and from which location.
Once the truck arrives at the Alnabru plant, the sacks are unloaded and moved through a portal using an Intermec IF2 fixed RFID reader. The portal reads each tag’s ID number, and that data is forwarded to ACT System’s middleware and, ultimately, to Norsk Resirk’s back-end software.
“We give incentives towards the carrier to keep track of what they receive from a DP, and what they deliver to our plant,” Ludvigsen states. “If a bag is missing, we know right away if it has been delivered to us or not. In other words, the RFID system relieves us from time-consuming investigations.”
In the future, Ludvigsen says, when Norsk Resirk installs RFID readers at all three plants, more data will be available to identify instances of incorrect goods deliveries. “This is important,” he explains, “because when bags are delivered to the wrong channel, they go right into the production facilities, and the articles will not be counted, leaving the DP without a correct payment.”
Armed with this information, Norsk Resirk will also be able to conduct business analytics, such as comparing how bags of recyclable bottles and cans were received from which locations.
Ludvigsen predicts that the RFID solution—once it is installed at all three of its plants, as well as at the DPs—will save the company tens of millions of Norwegian kroner (about six kroner equals one U.S. dollar). “A single plant installation saves money in the chain of logistics regarding its area,” he notes, “but we need to install the solution at all plants and DPs to close any possibility of losing bags in any area.”