A European McDonald’s restaurant operator is one of several companies piloting an RFID-based solution designed to provide real-time temperature and location data regarding such items as fresh food, pharmaceuticals and other temperature-sensitive products, from the point of harvesting or manufacture to the consumer. The system, provided by Norwegian company TAG Sensors, features a data logger consisting of a Near Field Communication (NFC) high-frequency (HF) or EPC Gen 2 ultrahigh-frequency (UHF) passive RFID chip, as well as a temperature sensor, a clock, an antenna and a printed battery. The full solution also includes RFID readers and printers, cloud-based software and a smartphone app. Companies like the European McDonald’s restaurant operator can use TAG Sensors’ solution not only to identify where goods are located (by reading the tags throughout the supply chain), but also to learn the temperatures to which the tagged goods have been exposed, and when, in order to identify any discrepancies before a product reaches a consumer.
The European McDonald’s entity has been testing the technology since earlier this year, according to Knut Nygard, the company’s cofounder and CEO. Other European companies, including food producers and pharmaceutical firms, are also either testing or preparing to test the system.
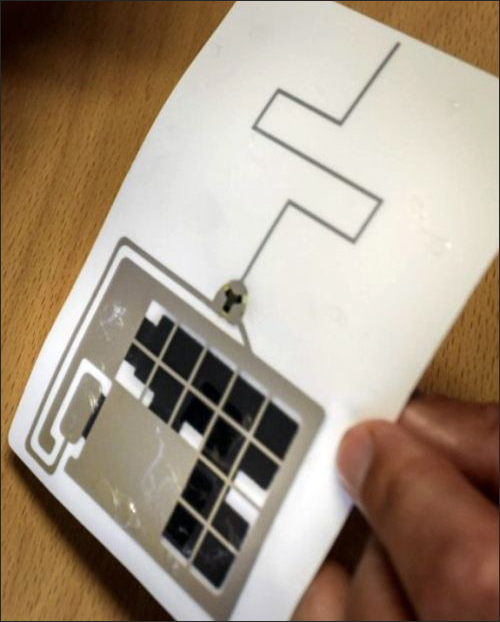
Traditionally, companies that must monitor the temperatures of goods face multiple challenges. Since products often change hands several times or more, traveling long distances geographically in the process, it can be difficult to obtain a full picture of those products’ temperature history. Even if a producer tracks the temperatures on its own site, and if retailers or distributors do the same, there are often black holes in which it is hard to know what is happening at any given time, such as when goods are standing on a dock door waiting to be loaded onto or off a truck or airplane, or at a train station or port. Data loggers are generally not designed to provide real-time data, and most passive RFID sensors can provide only the current temperature rather than historical temperature data.
Currently, few temperature-logger solutions are capable of following individual temperature-sensitive products from production to consumption, Nygard says, noting that what is available can be expensive. In fact, he adds, the lowest price on temperature loggers among competitors at present is approximately €15 to €20 ($17 to $22) per unit. “We are, therefore, developing a low-cost RFID temperature logger label,” he states.
With other data loggers on the market, Nygard says, users sometimes need to deploy a single fixed temperature logger in the production facilities, another for fixed temperature control within the transporting unit, a third fixed unit in the warehouse and a fourth in the distribution facilities. But these solutions do not provide what he calls a holistic solution—one that provides a full view into each item’s entire life cycle as it moves through the supply chain. “The weakest link,” he says, “is often in the transit between controlled facilities.”
TAG Sensors was launched in 2012—initially to provide UHF RFID technology for track-and-trace applications, Nygard says. The company’s founders came from the Visa and MasterCard credit-card industry, and were thus familiar with global RFID chip producers. They hoped to bring their knowledge of chips and security, and the encryption of data on those chips, to an RFID-based company.
To that end, they piloted their technology with a global salmon producer that has asked to remain unnamed. Quickly, Nygard says, they discovered that the salmon producer’s challenge involved tracking not just its products’ locations, but also their temperatures, from the point of production to the point of sale. TAG Sensors went about developing an affordable RFID-based temperature sensor system capable of tracking individual cartons via a disposable tag. Information regarding the manufacturing of the RFID chips, readers and printers used for the TAG Sensors solution is confidential, Nygard notes, and he, therefore, declines to describe any details.
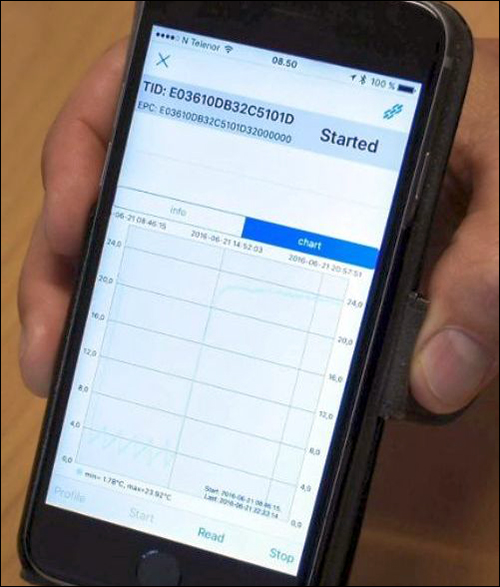
TAG Sensors provides the necessary printers, readers, software, app and data-logger labels, while its partner, CodeIT, provides the installation. CodeIT supplies such services as modifying the reader and printer software to ensure that it can capture sensor data from the label, as well as integrating TAG Sensors’ software with customers’ databases.
The TAG Sensors system typically works this way: A user would print and encode the data-logging labels on an RFID printer with not only a unique RFID number, but also instructions indicating how often the data logger should awaken, perform a temperature reading, store that data and go back to sleep. It would then use the power from an interrogator to transmit its ID number, along with the stored temperature data. NFC technology has a read distance up to 5 centimeters (2 inches), while UHF RFID offers a read-write distance of 0.5 to 10 meters (1.6 to 33 feet), depending on the label’s antenna design.
Tag Sensors’ label measures 54 millimeters by 85.6 millimeters (2.13 inches by 3.37 inches) and about 1.5 millimeters (0.06 inch) in thickness. Sometime next year, Nygard says, the company expects to offer a version of the label with an ecological printed antenna. The chip currently comes with a built-in temperature sensor, while future versions could accommodate other sensors, such as those that measure shock and humidity.
The data-logging label could also be printed with a user’s company logo, and its RFID chip contains sufficient memory that other data could be written to it as well. Its battery has enough power to store up to 841 temperature readings throughout the course of up to 18 months. The labels are designed to be low enough in cost that they could be disposed of at the end of a product’s transportation to the store and customer. However, Nygard adds, they could be reused.
Tag Sensors’ label comes with an adhesive back and can be affixed to a box’s interior or exterior. It could then be interrogated by a handheld reader with a Bluetooth connection to a smartphone; by a handheld that transmits data via a Wi-Fi, cellular or USB connection; or by fixed readers in portals or on desktops. The NFC version of Tag Sensors’ label could also be read using an NFC-enabled smartphone running the TAG Sensors app. Each time a reader captures the label’s temperature history, Nygard explains, that data is forwarded to TAG Sensors’ Tag Management System (TMS) cloud-based software, where it is stored securely. The information cannot be changed by any outside party, he notes, thus ensuring the authenticity of any data that supply chain members or customers view there.
Moreover, the software can issue alerts to authorized parties, such as a quality-assurance manager or a driver transporting a product, so that he or she can address the problem quickly.
The TAG Sensors app, available for iOS or Android devices, can display data for users as well. For instance, if an individual is reading a tag when receiving goods at a warehouse, using a Bluetooth-enabled handheld reader in conjunction with a smartphone, he or she can view the temperature results immediately in the form of a graph, and thereby take corrective action if necessary. The phone’s location data at the time that the tag is read will also be stored with the temperature data, creating a record of where the tags were interrogated, and thus where the tagged box may have been when an acceptable temperature level was exceeded, for example, as well as who was responsible for the problem.
“Our next step is to go global,” Nygard states. The company is currently in discussions with several companies beyond Europe that may begin piloting the technology for tracking food, pharmaceuticals or vaccines. In addition, TAG Sensors is working with partners to offer its solution in Asia for frozen fish and seafood. The solution, known as TR49: 2016 Cold Chain Management of Frozen Fish and Seafood, collects and manages data related to the temperatures and locations of raw and minimally processed frozen seafood.
Users can either buy the solution outright, or lease the hardware and use the software as a service, paying a monthly or annual fee. They would need to purchase the data-logging labels themselves, and the price would vary according to volume and the rest of the infrastructure they require.