Kerry Logistics, a Hong Kong-based third-party logistics company providing international freight-forwarding and supply chain services, has begun trialing an RFID system at one of its facilities, to track the kitting and shipping of Canon cameras and their components prior to their shipment to retailers. If the RFID system operates as hoped, it will provide the firm with greater visibility into the kitting of each product (which includes adding accessories and warranties to every item prior to packing it in a carton for shipment), as well as assurance that only the correct products are packed and shipped. In the future, the system will also provide a method for matching paper warranty documents with actual products.
Kerry Logistics provides freight-forwarding services for customers worldwide, and in some instances, the firm also offers value-added services (VAS) that may involve some level of packing or kitting of the products before shipment. The company operates 12 warehouses in Hong Kong, totaling six million square feet of warehouse space.
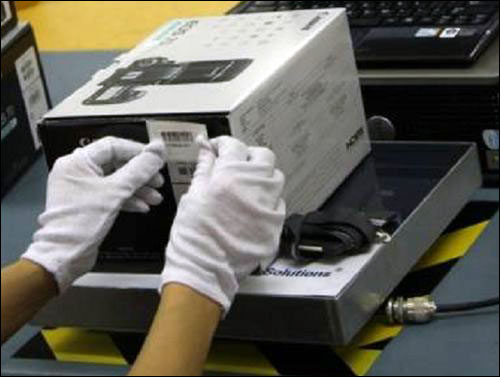
The RFID system was deployed at a Kerry Logistics facility through which Canon ships its camera products to retailers. When a retailer places an order, Kerry Logistics’ staff gathers the requested pre-packaged cameras and lenses for that particular order, adds the necessary accessories and warranty documents to the individual cardboard box in which each item was pre-packaged, and then packs the boxes in cartons to be shipped. Shipment accuracy, says Wilson Lee, Kerry Logistics’ director of information technology, “is very, very important.”
Until the RFID system was launched monthin mid-2010, verifying that an order was filled correctly required employees to look up each product’s serial number and associated stock-keeping unit (SKU) number, in order to confirm that the items being packed matched the order, and to then scan the bar-coded number printed on the packaging and corresponding to the product’s serial number. While workers rarely make mistakes, Lee says, the process is slow. RFID, he notes, should reduce the time spent ensuring the proper items are being packed.
With the new system, once an order is placed, the necessary products are gathered and moved to the kitting assembly line, where accessories and warranty documents will be inserted into each camera’s cardboard packaging. The order number and details for that order, including the ordered products’ SKUs, are stored in Kerry Logistics’ management system, and are displayed on a screen at the assembly line. An RFID printer at the beginning of the packing line encodes a unique ID number to an ultrahigh-frequency (UHF) EPC Gen 2 RFID label from Avery Dennison, which is applied to the cardboard packaging of each camera or lens as staff members scan the bar-coded number linked to the item’s serial number on the packaging. That RFID number is captured and then forwarded from the reader to the back-end system, via a cabled connection. RFID middleware provided by PCCW Solutions translates the data and sends it to Kerry Logistics’ warehouse-management software, where the bar-code number and the SKU data associated with it are linked to the RFID number and stored. At the same time, the staff prints a warranty card containing that item’s serial number, to accompany the product that has just been tagged.
As the cameras and lenses are packed in a carton according to the retailer’s order, a Convergence Systems Limited (CSL) CS461 fixed reader captures each item’s RFID number and links that information with the order number, thereby creating a permanent record of what has been packed. The staff then adds any necessary accessories, and also places the warranty card for each camera or lens inside its packaging before the carton is sealed. Typically, six to eight boxes of cameras or lenses are packed in each carton.
As a worker loads cartons onto a pallet, the system automatically reads the products’ RFID tags once more, and the ID numbers are compared against the order being filled, to ensure accuracy and also update the database regarding what is being shipped. If there is a discrepancy, such as incorrect or missing items, an alert can be displayed on a monitor in the packing area. The cartons are then shipped to retailer customers throughout Hong Kong.
By using the RFID system, Kerry Logistics maintains a record that its staff can access, indicating what was packed and shipped, and to whom. Initially, the company is employing 25,000 tags, to be attached to the cameras’ packaging as they are packed. When those tags are used up—which the two companies estimate will occur sometime toward the end of the first quarter of 2011—Kerry Logistics and Canon will review the system’s success in capturing and storing useful data about the shipments, and then plan the next phase of RFID implementation.
Assuming Phase 1 of the pilot is judged to be a success, Lee says, the two companies expect to launch Phase 2 by mid-2011. For the second phase, the items’ packaging would again be tagged, and drivers would employ handheld readers at the stores, where pallets loaded with products are delivered, for proof of delivery. Currently, drivers must disassemble each pallet, open every carton and scan the bar-code number on each item’s packaging to ensure the order is correct, and then leave the shipment for store employees to go through at another time. A typical pallet carries 20 cartons, which means the bar-code numbers of approximately 140 individual items must be scanned per pallet.
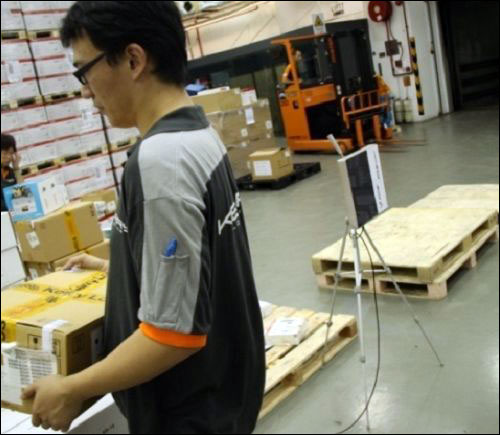
With the use of the RFID system, the driver will unload the cartons from the truck, use a handheld interrogator to read the ID numbers on all products packed within those cartons, and thus gain a list of every item delivered. He or she could also then print a manifest using a handheld reader, a Wi-Fi connection and a laptop computer, and present it to the store prior to leaving the facility—though, initially, that would not be part of the Phase 2 deployment. Once retailers trust this new, more automated system, Lee speculates, they will feel less of a need to require their staff to count the items themselves in order to verify delivery accuracy. The length of Phase 2 has yet to be decided.
Phase 3 would involve the use of RFID tags on warranty cards—a plan still under discussion with Canon. If the third phase were to be deployed, staff members would attach RFID tags to each warranty card, containing an ID number corresponding with the product’s serial number. RFID tags would not be attached to the packaging in that case, but only to the warranty cards.
When a customer purchases an item, the retailer would use a handheld or desktop interrogator to read the tag of that product’s warranty card and initiate the warranty-registration process. The tag could also be used if a product needed to be returned or serviced. In such a case, the card would be returned with the item and be read by an RFID reader at a Canon dealer or retailer (if that site is equipped with an interrogator), in order to confirm the item has been returned. The RFID-enabled warranty card would make warranty registration and processing easier in the store, according to the companies, and could also ensure the identification of counterfeit products, since a counterfeit item’s warranty card would presumably lack an RFID tag. For Canon, the benefit would be in gaining faster access to sales and warranty data (since warranty-related processes could be accomplished via an RFID reader at the store), as well as in the identification of customers in the event of product recalls.
“I would say, for Phase 1, the benefits of using RFID are not going to be so significant,” Lee states. “Our accuracy is already good. We have high-quality workers in Hong Kong, but we needed to do something to give the staff the experience of working with RFID. If we install Phase 2, this will speed the delivery process and save our drivers a lot of time.” He expects drivers to be able to deliver 30 percent more product each day thanks to the RFID system.