Manufacturers and other industrial companies are deploying Internet of Things (IoT) technology from Wilden, a PSG company, to monitor performance of the air-operated diaphragm pumps it manufactures, which are used to transfer fluids, sludges and solids under pressure. With a new wireless intelligence modification added to their Wilden pumps, known as Wilden SafeGuard, the companies are tracking when the devices leak and when they fail to pump properly.
In the event of a leak, this enables companies to detect or prevent damage to pumps, as well as the facility containing them and their products. The SafeGuard system, which has been piloted by several businesses for the past few years, was released commercially this spring, says Erik Solfelt, Wilden’s diaphragm pump product director. The system employs sub-GHz ISM bands RF transmission, along with cellular connectivity, to automatically send data to the cloud related to air-operated double diaphragm (AODD) pump performance. As a retrofit kit, the solution consists of an edge device and a leak-detection unit installed on the Wilden pump that can provide stroke counting to identify the speed at which the pump moves solids or fluids or to detect a leak.
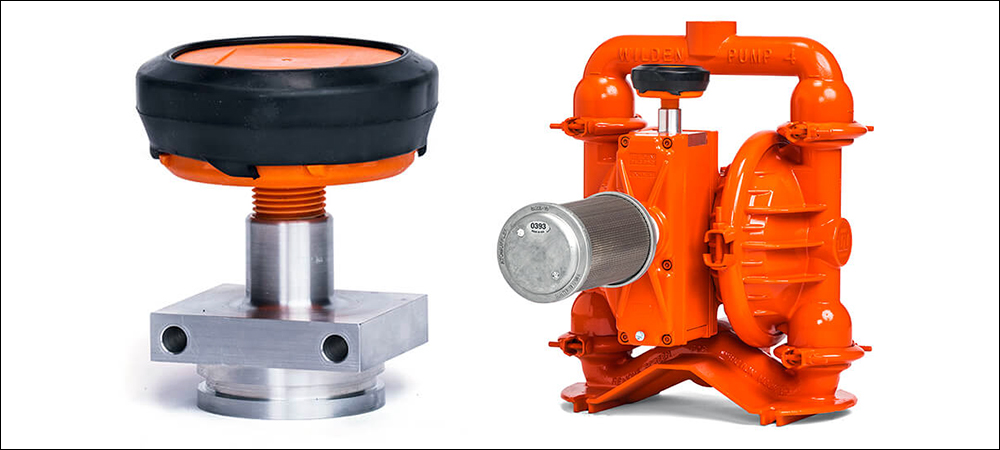
Wilden’s Safeguard system
The SafeGuard monitoring and alerting system was commercially released in April 2020. California-based Wilden is the largest manufacturer of diaphragm pumps. According to the company, its AODD pumps serve critical processes in the manufacturing of some goods. Diaphragm pumps move solids and fluids as part of the manufacturing process, and they are used to monitor products ranging from “blood to mud,” the company states, including products such as chicken fingers and explosive powders. Most commonly, the equipment is used to transfer paints and coatings, chemicals, water and wastewater, as well as products that are part of oil and gas production.
The pumps are relatively simple in design, the company reports. They require no power and instead leverage compressed air that is fed into and vented from air chambers on either side of the pump, thereby pushing matter through at varying speeds. The pumps come in many sizes, based on the inlet and discharge size; some smaller models manage five gallons a minute for small injections, while much larger pumps cant flow 50 to 300 gallons of liquid per minute. The larger devices are those that typically benefit from the SafeGuard system, the company notes.
The stroking process enabled by the compressed air pushes matter through the pump at a speed set by a user. If the stroke count drops, that can indicate a potential problem. Typically, Solfelt says, an AODD pump has several primary wear points: the diaphragms, balls and seats. For companies using the pumps, however, identifying problems with any of the devices’ parts can be challenging. Since they require no electrical connection, they are often deployed in places that are out of reach, such as in corners, behind other equipment or in a basement.
The pumps rarely come with any sensor-based functionality, in part because the products are relatively simple in design with no electricity. That means that tracking their condition and replacing or maintaining them at the appropriate time can be challenging as well. Traditionally, there have been two approaches to maintaining and replacing the pumps. Some companies simply run them until the diaphragm ruptures, then repair or replace the entire unit. Others establish preventative maintenance schedules to be more proactive and try to replace worn parts before a failure can occur.
The SafeGuard system consists of a battery-powered edge device with a vibration sensor that can detect cycle counts or ruptures. That data, along with the device’s unique ID number, is transmitted to a gateway via a 920 Hz RF transmission. Data can be transmitted at a distance of up to 150 feet in a typical industrial environment, using batteries to operate the sensor and send the information. The gateway, which is also battery-powered, transmits the data via cellular connectivity. Wilden’s cloud-based software then manages and displays all of the captured information. Up to 10 such devices can transmit a signal to a single gateway, and companies can deploy an unlimited number of gateways at a site.
The SafeGuard system comes in several versions, the company notes. Each version can detect the pump’s stroke rates, measuring the total number of strokes during a specified period of time, as well as when that rate changes. In that way, Solfelt says, a potential failure could be prevented even while the pump is still operating. Users can set the appropriate cycle rate for the pump they are operating in the software. If the users require help setting up the system, he adds, “We have a team dedicated to helping, too.” The solution can also capture data for analytics purposes. That information can be exported into a Microsoft Excel file or other software for users to gather and analyze.
A second version is intended for those looking to add leak detection to their stroke rate operating system. A leak-detection sensor built into the device identifies if fluid has been released into the air, which could indicate a rupture. The software can then forward an alert. In that way, the system can ensure that the pump is shut down by operators and does not continue to operate with the rupture, which could cause liquids to leak onto the floor or into machinery, resulting in clean-up costs and product loss.
In the future, the company reports, customers will be able to purchase pumps with the Safeguard system included, though most users to date have been purchasing a retrofit kit built for easy installation. “That was a main focus of ours as we were developing this,” Solfelt states. “We realize our pumps are used because of their ease of use. We understand that.” The solution, he says, “provides unprecedented access into real-time information about what is happening within a pump.” He adds, “Being able to reduce the cost of ownership by eliminating product loss is a major benefit.”
The system is designed to enable companies to create more accurate preventative maintenance plans, Solfelt says. Some companies might repair or replace all of their pumps simultaneously, though with information captured automatically, they could refine their plans to better schedule maintenance. That would save the cost of replacing a pump that still has operational life remaining, he explains. An average 1-inch pump costs approximately $1,000, whereas a 3-inch pump averages $2,500 to $5,000.
The gateways’ cellular communication comes encrypted, Solfelt says. “The focus is on creating good packaged data that’s secure,” he states. The company, which has designed and assembled its own products since 1955, was launched by Jim Wilden, an inventor of air-operated diaphragm pumps, who created and then sold the pumps out of his own garage and the back of his truck.