A year ago, AT&T, Cisco, General Electric, IBM and Intel formed the Industrial Internet Consortium (IIC). Their goal was to accelerate the deployment of networked sensor-based technology (the Internet of Things) in the industrial sector (or the Industrial Internet, as the firms framed it) by “identifying, assembling and promoting best practices.”
One way in which the IIC plans to do this is by evaluating and sharing standards-based open architectures through the creation of what it calls testbeds.
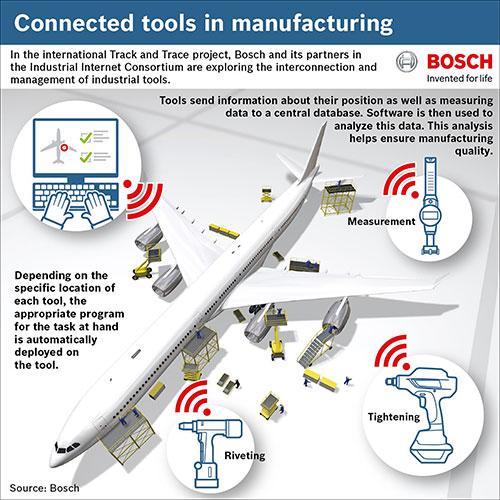
Michael Lee, who directs the IIC testbed program, says the Industrial Internet Consortium was created as an ecosystem of members. Those members are divided into two groups: those that focus on best practices, use cases and identifying areas of business opportunity, and those that concentrate on refining the technology, security and software architecture, as well as open standards required to deploy Industrial Internet applications.
“These two groups,” Lee says, “drive the testbeds forward.”
Last week, IIC member Bosch was the first company to publicly announce such an IIC program, known as the Track and Trace Testbed. It is partnering with Cisco, networking and IT consultancy Tech Mahindra and National Instruments (NI) to create the testbed, which will describe a standards-based framework for precisely tracking both the location and usage of automated hand tools within an industrial setting.
Bosch revealed the project last week at its ConnectedWorld conference in Stuttgart, Germany. Thus far, the collaborators have developed a process for wirelessly determining the position of a cordless nutrunner (used to tighten nuts) on an assembly plant’s floor. Based on this information, a wireless command can be transmitted to a communication module embedded in the tool, which will transmit the exact torque settings required for tightening nuts at that location within the assembly process.
The Track and Trace Testbed’s goal is to “define open interfaces for smart tools,” Lee explains, but these will be networking standards, such as Representational State Transfer (REST), a widely used software architecture, rather than protocol interfaces at the hardware or router level.
“They will be defining application interfaces that [end users] can use that are appropriate to smart tools,” Lee says.
In a press statement describing the project, Bosch wrote: “Open standards are set to enable the seamless integration of industrial power tools used to drill, tighten, measure and solder into an overall system of networked tools in the future. The potential applications of connected hand-held nutrunners, riveting tools, and measuring equipment include the construction and maintenance of engines and aircraft.”
Jamie Smith, National Instruments’ director of embedded systems product marketing, says the testbed was inspired by work that the firms have been doing with Airbus to develop what it calls the Factory of the Future. Bernard Duprieu, the head of manufacturing technologies for Airbus’ research and development arm, appeared on a panel discussing the Factory of the Future project shortly after the testbed was announced at the Bosch conference. The airplane manufacturer, however, is not an official testbed partner.
According to Smith, NI is helping to architect the means by which a given hand tool processes commands, which would change dynamically based on the tool’s location within the factory. Another architectural factor that might be evaluated as part of the testbed is whether those process controls would run on the tool itself or in a back-end server for best results.
The testbed is also evaluating which specific wireless technologies—such as ZigBee or some other type of radio frequency-based location protocol—are most effective for pinpointing tool location.
Lee notes that the physics within, say, a plane’s fuselage may impact the RF performance of various wireless systems in ways that would differ from, for instance, an automotive assembly plant. The testbed could make use-case recommendations for different technological approaches to location tracking, based on various physical environments within the larger manufacturing sector.
While the IIC helps to foster testbed activity and sometimes connects participating organizations with funding sources to develop the testbeds, Lee adds, it is up to those participants to decide how much documentation relating to the testbed they will share—unless the project receives public funding.
And while some of the specific functionality of the hardware and software may be proprietary, the testbed program’s goal is to encourage the use of open standards at the system architecture level. For manufacturing companies, this will make deploying Industrial Internet solutions more compelling, by not tying them to specific vendors.
Still, technology firms will always retain some level of product specialization. “Some large companies are participating in the IIC, but also simultaneously developing their own proprietary solutions. They’re hedging their bets, and that’s fine,” Lee states. “They’re not here for altruistic reasons; they’re here to make money and to grow the market for the Industrial Internet.”
The Track and Trace Testbed is the first of many that the Industrial Internet Consortium plans to release—all of which will describe a means of improving quality and efficiency in industrial manufacturing.