After three years of testing RFID solutions to food-safety challenges, the Hawaii Department of Agriculture is preparing to launch a new pilot intended to test whether temperature sensors in RFID tags, attached to reusable plastic pallets, would enable members of the produce supply chain to monitor the condition of products as they are shipped from one Hawaiian island to another. The pilot is an international effort, with data stored and shared on a server provided by GS1 Hong Kong, and involving reusable plastic pallets, RFID software and consulting provided by Asia Pallet Pooling (APP), a Taiwanese supply chain solutions firm that is also largely financing the project. If the four-month pilot goes well, John M. Ryan, the administrator of the Hawaii Department of Agriculture’s Quality Assurance Division, hopes it could be used outside of Hawaii to track produce shipped between the state and Asia, South America or North America.
Three years ago, the agricultural department was testing RFID to provide traceability for produce from local Hawaiian farms through the supply chain, all the way to retail stores (see Hawaii Plans Trace-Back Program for Fresh Food). The pilot, Ryan says—involving three Hawaiian farms that attached EPC Gen 2 passive ultrahigh-frequency (UHF) RFID tags to each carton of produce—proved that the technology works. However, he notes, the cost of software, tags and readers all made the solution too expensive for many small Hawaiian farmers.
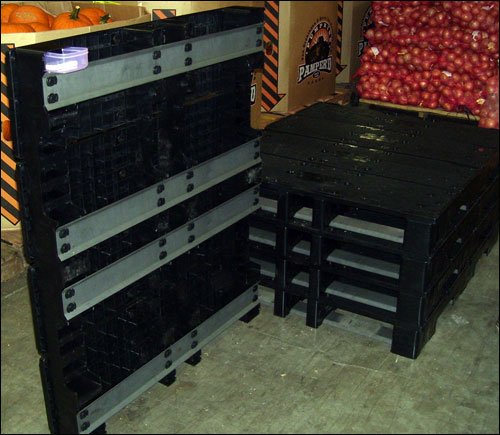
This new pilot, set to commence in the next few weeks, takes a different approach that Ryan predicts could prove to be a better, lower-costing solution, by using temperature-sensor RFID tags on pallets, and bar codes on cartons, as well as a data “cloud” solution from GS1 Hong Kong that would enable interested parties to access information via the Internet regarding a particular shipment.
Ryan says Asia Pallet Pooling contacted him in November 2009 to suggest the pilot. The company donated the pallets, as well as integration services, for the pilot, and assisted Intelleflex in modifying a Motorola 9090-G RFID handheld reader (so that it could accommodate the battery-assisted tags), and in developing software to run on that device. For several years, Ryan had been planning to conduct a pilot of temperature-sensing technology, but the cost of hardware, in addition to the lack of funding, had prevented it until now.
APP has designed a lightweight 48-inch by 40-inch plastic pallet fitted with a transparent plastic bracket that houses an RFID tag equipped with a temperature sensor. The company’s solution includes a portal in which data is stored on an application hosted by GS1 Hong Kong—a system known as ezTrack (see GS1 Hong Kong Launches Online Track-and-Trace Platform)—in which data from each temperature reading could be received and stored, and then be accessed by members of the supply chain.One participant in the pilot is Armstrong Produce, a Hawaiian distributor of fresh fruits and vegetables, which will use the RFID-enabled pallets to track its produce as it is shipped between three islands: Oahu, the Big Island of Hawaii and Maui. The project includes 100 APP plastic pallets, each fitted with Intelleflex battery-assisted passive (BAP) UHF Gen 2 tags equipped with temperature sensors. When produce arrives from a Hawaiian farm at any of the firm’s three distribution centers—one on each island—it will be placed on one of the reusable plastic pallets. The tag’s sensor will capture the temperature at preset intervals (the rate has yet to be determined), and store that information in the transponder’s 60 kilobits of memory.
In addition, members of Armstrong’s staff will read the tag four times throughout the pallets’ shipment from one island to another. The first read will take place when the product is loaded onto the pallet. An employee will use a modified Motorola 9090-G RFID handheld computer to read the pallet tag’s unique ID number, along with the temperature data. He or she will then use the handheld device’s bar-code scanner to read the bar-coded number printed on each carton stacked on the pallet. In that way, Armstrong can store the information on its own database, indicating such data as the type of product on each pallet, the name of the farm from which the produce originated, and the date on which it was picked.
The temperature data is also linked to the tag’s unique RFID number, and is uploaded to GS1 Hong Kong’s server. This will enable Armstrong to know exactly what is loaded onto each pallet, allowing the firm to marry temperature data (downloaded from the GS1 Hong Kong server) with historical (bar-code related) data saved on its own back-end system, such as where and when the goods were picked. The company’s DC staff can also input additional information—such as the pallet’s destination—into the handheld reader, and upload it to the GS1 Hong Kong server via a Wi-Fi Internet connection, or later transfer that data to a PC in one of Armstrong’s offices.
The pallet is then loaded onto a truck and transported to the airport. Once the pallet is removed from the vehicle, and prior to its being loaded onto an airplane, the tag on that pallet is read again by Armstrong’s staff, thereby capturing all temperature data stored since the last reading was taken at the DC. The plane transports the pallet to another island, where it is offloaded and the tag is again interrogated by Armstrong workers picking up the produce. It is then read for the fourth and final time once the pallet is received at the second distribution center.
Intelleflex software running on a handheld reader receives data from each read, interprets the temperature reads and links them to the tag’s unique ID number, then forwards that information to GS1 Hong Kong’s server. However, the device is also able to issue alerts if a temperature threshold has been exceeded, indicating that the produce became too warm, for example, on the plane, on the tarmac or on a truck. The Intelleflex software could then send that alert to an interested party’s e-mail address or cell phone.According to Ryan, the research team—which includes representatives from APP, GS1 Hong Kong, Armstrong and the agriculture department—also plans to test Intelleflex fixed interrogators to create portals at some locations. Currently, though, the team is employing only six modified Motorola 9090-G handheld readers, all of which will be operated by Armstrong’s staff, including truck drivers transporting the product to and from airports.
Ryan is currently in the process of building relationships with agriculture agencies in other countries interested in participating in an international pilot that would include utilizing the tagged APP pallets to ship produce from their nations to Hawaii, as well as reading the sensor tags on pallets of products being shipped from the state. Thus far, Ryan says, Mexico’s Department of Agriculture has expressed interest in testing the system.
To prepare for the upcoming Hawaiian pilot’s launch, Ryan says, the team tested the Intelleflex tags by placing them between cartons filled with tomatoes. There were no problems reading the tags, he notes, though the RF signals of the reader and the tag had to pass through a carton’s worth of produce.
Reflecting on the Hawaiian agricultural department’s 2007 pilot involving passive UHF tags on cartons from Hawaiian farms, Ryan says, “The technology is great, but it has to be cost-effective for everyone”—and at the time of the pilot, it was not. A 15-cent tag for each carton, he adds, is too expensive for small farmers. However, he hopes that if the current pilot proves RFID data can be effectively linked to bar-code data, a system could be developed in which a pallet tag would provide cold-chain tracking, with information about the produce transported on that pallet stored via a bar-code system. Printing bar-coded labels for cartons, he notes, would be an inexpensive solution for farmers, since most office printers can easily print a bar code.