Güdel Group manufactures high-precision machine components, automation systems and reusable transport items (RTIs) used by manufacturers in the automotive and tire industries. The Swiss-based company recently began offering an RFID-enabled solution to help companies automate tire manufacturing. The solution features trays fitted with RFID tags provided by Schreiner ProTech.
Prior to being vulcanized, tires are sticky and soft, and are called green. “The stickiness complicates the handling,” says Stefan Güdel, the company’s tire trays project manager. “Due to its softness, a green tire has to be handled very carefully to avoid any damages and avoid quality issues.”
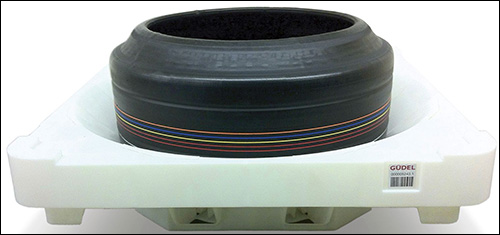
To address this problem, Güdel Group created the Green Tire Tray, an RTI built to transport tires during the production process. The tray, designed so that sticky, green tires can be easily extracted from the trays without damaging them, can accommodate a tire up to 900 millimeters (35.4 inches) in diameter and as heavy as 30 kilograms (66 pounds).
To enable the automation of the manufacturing process, the trays were also fitted with RFID tags. Readers capture each tag’s data and forward it to the manufacturer’s programmable logic controller (PLC). The PLC can then use this information to prevent damage to the tires, by controlling such variables as how long they can be stored and the amount of soiling they can sustain. Since the solution’s release, one of Güdel Group’s customers has been using approximately 2,000 of the trays for its production of ultra-high-performance tires. (That company has asked not to be named for this story.)
During the manufacturing process, each green tire is placed on a single tray, on which it then moves throughout the manufacturing process on a conveyor. Typically, a green tire is created out of rubber and textile and steel cords. As soon as all components are assembled together, this half-finished product is moved to the automatic storage and retrieval system (AS/RS)—which stores the green tire for a defined period of time before being cured under pressure and heat.
Each tire is unique to its product type as well, so that tires of certain styles and sizes must be treated differently than others during the manufacturing process. Due to the sensitive nature of green ties, manufacturers typically use manual processes to transport tires from the assembly line to the vulcanization process. Alternatively, Güdel says, they can utilize an automated system designed for increased cleaning and maintenance of the equipment used for handling the tires, though an automated system also increases the risk of damaging a tire or reducing its quality.
Affixed to each tray is a 13.56 MHz Schreiner ProTech high-frequency (HF) passive tag that measures 50 millimeters by 50 millimeters (2 inches by 2 inches) and complies with the ISO 15693 standard, says Frank Linti, Schreiner LogiData’s business-development manager for RFID. “The customer needed a label programmed with the project ID and the tray’s own unique identifier, and with very strong adhesion and long durability in very harsh conditions,” Linti says. The label needed to be resistant against dirt, washing processes and scratching throughout the tray’s entire lifetime.
In addition, Güdel Group required that a bar-coded serial number be printed at the top of the label for situations in which the use of RFID would not be possible. “We deliver preprinted and preprogrammed labels with bar codes and the Güdel logo in red,” Linti explains. “To protect the label in washing processes and against scratching, we provide the label with a clear coating [lamination].”
A tire factory is a uniquely challenging environment for RFID tags, due to the dirt and vapors that can be found around the tires. These pollutants would affect the ability to scan a bar code, Linti says. “In a dirty environment,” he states, “we also expect [RFID to provide] a more stable reading process over a long time, as the bar code might be contaminated over time with pollutants in the vapors from the curing process.”
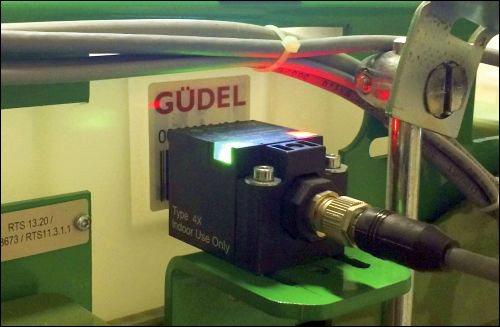
Güdel Group’s RFID-enabled solution—which includes Rockwell Automation readers to capture data encoded to the trays’ tags—interfaces with the PLC and the user’s own manufacturing and management software.
Readers are installed in two places, Güdel says: on the device running the AS/RS system—specifically on the Z-axis carriage close to a telescopic fork—and at the station where the tire is placed into the tray.
First, a new tire is associated with a tray’s tag ID number. The station’s Rockwell Automation reader interrogates the tag, and users can input any necessary data regarding that tire, including its product number, size and style. This information is then linked to a time and date stamp and written to the tray’s tag.
“Using RFID technology on the trays, each tire can be identified, including all needed production data,” Güdel says. So when the tire is moved through the manufacturing process and then to the AS/RS area, the tray passes the reader mounted at the curing area’s entrance, thereby cross-checking tire type and the conditions under which that tire has been stored.
The company can access that information for historical purposes, to confirm not only what processes the tire went through and when, but also the tray, thereby confirming each time it is used. That usage data can also enable the tire manufacturer to track how often the tray has been used and, therefore, when it may be due for replacement, cleaning or maintenance.