After nearly four years of using radio frequency identification at its own facility, NGF Europe (NGFE), a British manufacturer of specialized glass-fiber cord products, has begun writing data to its tags, so that its customers themselves can read them in order to learn more about the product.
At NGFE’s manufacturing plant and warehouse in St. Helens, England, the company has been employing 13.56 MHz passive RFID tags, complying with the ISO 15693 standard, to track the glass-fiber cord as it is manufactured, wound on spools, stored and then shipped to tier-one automotive companies, to be built into items such as timing belts. The use of RFID provides the firm with visibility into work-in-progress and inventory. But perhaps most important, it also ensures that the spools—which are wrapped in multiple layers of thin, black plastic before they are shipped—are, in fact, the product they are believed to be. By knowing exactly which product is on each spool, even after it is wrapped, the company, as well as its customers, can verify that no mistakes have been made.
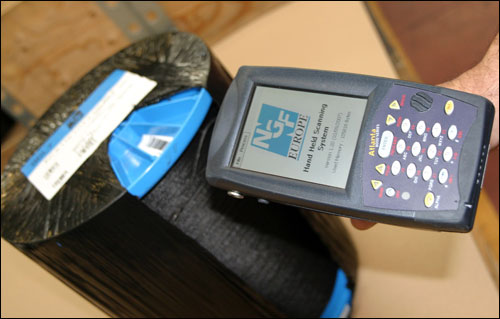
The glass fibers embedded in the cord act as a strengthener in certain rubber products, such as timing belts used in automotive engines. NGFE sells the cord to automotive-parts manufacturers, in long strands wrapped around spools. In the automotive industry, the use of the proper glass-fiber cord is critical. The cord is manufactured in a range of diameters, each with different degrees of twisting and materials, and every permutation provides the cord with distinct performance characteristics. When the cord is on a spool, it can be difficult to determine one type from another. Once incorporated into a product such as a timing belt, however, an incorrect glass fiber cord can cause that product to fail.
Prior to adopting an RFID solution four years ago, NGFE’s staff printed a bar-coded serial number onto a label attached to the spool itself. That label could then be scanned to verify the type of cord on that particular spool, until the point at which the spool must be wrapped with black plastic, a total of 15 times over, to ensure the cord is not damaged by ultraviolet light and humidity. With the package wrapped, however, the spool’s bar code was no longer visible, and thus could not be scanned.
When a spool of cord was prepared for shipping, explains Peter Lai, NGFE’s assistant production manager, its bar code was first read to confirm it was the correct type, after which the plastic was wrapped around it and a second printed bar-code label was attached to the plastic wrap’s exterior, indicating the type of cord on the spool. However, there was the potential for error. Labels on the wrap could often be damaged or lost, at which point, since the label on the spool itself was obscured by the black plastic wrap, the only way to verify the product on that spool was to remove the wrapping and read the underlying bar-coded label. In contrast, an RFID tag is readable directly through the wrap.
For the RFID system, NGFE created its own Windows-based software system to store information. Its workers use handheld readers from Belgravium to read ID numbers encoded to the 13.56 MHz tags. Operators first receive a production schedule listing the products that need to be manufactured. An operator utilizes a handheld interrogator to capture the ID number encoded to the RFID tag on his own staff ID card, thereby enabling the system to link that individual with the work he is about to perform.
The display on the handheld then asks the operator to scan the bar code on the work instruction sheet for the product that person intends to make, as well as the bar code of the input material selected to produce the product. At this point, the scanner validates that the correct products are being used. If an incorrect product was utilized during the process, the handheld displays an alert, thereby catching the mistake before the product is produced.
Once the cord is made, a Sato RFID printer encodes a unique ID number and a product number (used in-house to identify each product) to an Inotec Barcode Security RFID label, attached to the spool. NGFE can utilize the interrogator in the handheld to read the RFID tag, and NGFE software links the tag’s ID number with data related to that spool. This can include information about the machine, along with the time of the cord’s manufacture, thereby establishing a history of that spool.
Once that process is completed, the spools are brought to the warehouse, where they are weighed and then wrapped in black plastic, at which time they pass through a fixed RFID portal provided by Escort Memory Systems (EMS). The portal reads the ID and product numbers on the spool’s RFID tag, and transmits those numbers, along with a date and time stamp, to the software via a cabled connection. At that time, an adhesive label is printed with a bar-coded ID number and text, and is applied on the spool’s exterior.
If a spool of glass cord is found to require reworking at the time of packaging, the spool can be removed from the process and sent to another area to be rewound. With the RFID system, employees can simply read the spool’s tag, and indicate on the handheld reader that the spool is going to be rewound, thus ensuring that a record is maintained in the back-end system regarding that spool’s status.
The RFID system, which went live in December 2006, not only saves the staff hours of labor, but also improves accuracy. Thanks to the system, the company now knows a product’s entire history, from the point of manufacture to the moment it is shipped to a customer. This includes a record of which personnel produced that product, moved it into storage, and then packaged and shipped it.
Recently, the company decided to extend the RFID system to provide quality information to its customers. This month, the firm began writing additional data to the tag’s 1024 bits of memory, which its customers can then access. In this case, the company is encoding the tag with detailed specifications, such as weight (both in kilos and pounds, to accommodate customers on multiple continents) and materials used, as well as test results—all of which can then be read by the customers. “Previously, we sent test certification by paper to the customer,” Lai says. NGFE will continue to send the paper version, but customers with RFID readers can now also capture the test certification on the tag itself. Some customers, Lai indicates, have already acquired interrogators to read the labels.
“In the future,” Lai says, “we are looking to an online database for customers as well.” Those companies will then be able to use the interrogator to read a spool’s tag and then access a server hosted by NGFE, in order to learn more details about the product on that particular spool.
That system, Lai notes, could be available in mid-2011.”That’s our goal,” he states, adding that NGFE also intends to introduce a similar RFID system at the manufacturing plant of its Canadian subsidiary. The details of that deployment, however, have yet to be determined.