Monitoring hundreds of customized fire trucks throughout a large manufacturing site and yard can be a labor-intensive process. To make it easier to identify where its trucks are located as they are built, Morita Group has deployed a Bluetooth Low Energy (BLE) solution from Kokusai Kogyo Co. (KKC) using Quuppa Locator sensors and BLE tags on each vehicle.
The solution can identify each vehicle within about 1 meter (3.3 feet) at the 55,000-square-meter (592,000-square-foot) facility. The system has enabled the company to boost efficiency by understanding the work-in-progress status of each vehicle, and by reducing onsite manual search times. It next plans to track tools and parts as they are received from suppliers, as well as capture safety information related to the locations and health conditions of workers.
Morita, a global fire truck manufacturer, built Japan’s first fire pump with a gasoline engine in 1910 and has since been manufacturing and selling trucks in Asia, Europe and North America. The company makes the vehicles at its Sanda Factory in Sanda City, in Japan’s Hyogo Prefecture (north of Osaka), typically selling about 700 fire trucks every year. There may be as many as 300 trucks onsite at any given time in one of two building or in an outdoor yard. The vehicles are usually custom-made and are, therefore, not assembled on a typical automotive production line. Instead, the company builds the vehicles by moving them through stations in the terminal, and there are many fire trucks assigned to specific stations at any given time.
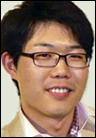
Hiroki Konno
The facility’s large size makes it challenging to locate a single truck as it is moving through production or is in storage awaiting shipping, explains Hiroki Konno, the group manager of Morita’s Sensing and Braking Unit (SBU)’s Location-Based Services Group. Sales personnel often contact the production team to learn the status of a specific project, but information about a particular vehicle’s status was not readily available. What’s more, manually searching for a single fire engine within the facility could take about two hours.
The company began seeking a solution in 2016. The first BLE solution, using received signal strength indicators (RSSIs) to identify location, did not provide the location accuracy the company required. That system could only identify generalized zones in which a tagged truck might be located. In October 2017, the firm approached KKC for an alternative.
KKC provides real-time location system (RTLS) solutions across numerous industries, including smart cities and urban development. The company provides ultra-wideband (UWB)- and BLE-based solutions. It selected BLE in this case, says Fabio Belloni, Quuppa’s cofounder and chief customer officer, in part because UWB has bandwidth restrictions in Japan, while Bluetooth can be used universally in Europe, Asia and North America. Quuppa’s technology, he says, was the only one that could deliver what Morita required according to specifications.
Not every system works well in this environment, Konno notes. There is a large amount of metal and moving parts that could block wireless transmissions. “We checked the coverage area, read accuracy and multipath resistance,” he states. The company then launched a single-day proof-of-concept (POC) with Quuppa Locators and BLE tags on vehicles in one area within the factory, followed by a week of analysis.
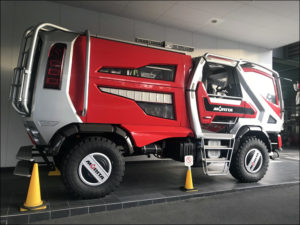
Based on that POC’s success, Konno says, the company opted to launch the system throughout the entire factory. Kokusai Kogyo’s solution generates real-time data that management can monitor, the company explains, in order to understand the flow of vehicles through assembly, identify any bottlenecks or delays, and locate vehicles in real time.
KKC installed 66 Quuppa Locators around the facility, suspended from the ceiling. Outdoors, the firm mounted the Locators on the sides of buildings, tilted to best capture transmissions from vehicles in the L-shaped lot. The company is now dedicating a BLE tag for each fire truck as assembly begins. The work starts with a chassis on which customer-specific trucks are built. Customers may provide the chassis, engine and cabin that will be used, and Morita builds the rest of the fire truck according to that customer’s specifications.
Instructions for each project were traditionally provided on paperwork that travels with each truck. With the BLE solution, a beacon is placed on the dashboard along with the paperwork. The unique ID number of the beacon’s tag is associated with that order. The software provided by KKC tracks the vehicle’s position inside two different enclosed factory areas, as well as in a storage yard outdoors.
The truck’s location, determined by Quuppa’s Locator technology, is then identified as it moves, indicating the workstation at which the vehicle is located. The software then manages that data and identifies the truck’s status, displaying a map of the facility with dots representing each vehicle. A blue, green or red light can indicate the stage at which any given fire truck is at, as well as when production is either delayed or ahead of schedule. Large screens are installed around the facility so assembly shift managers can identify each vehicle’s status in real time. The data is also available to managers via the software, which resides on a local server.
With the data, the company can find trucks in real time in order to update sales personnel and customers, as well as capture historical data to improve efficiency. If specific bottlenecks are identified, for instance, Morita can adjust scheduling and training. “They wanted to validate that everything was moving at the right pace at the right time,” Belloni says.
There were several challenges related to the facility’s environment, Belloni recalls. “One thing that is important is making sure location data is accurate,” he states, because each workstation is located very close to the next. That required extensive planning before installation of the antennas. Another challenge was to ensure that the tags could be read even if a truck cabin was open while engine-related work was under way, which causes the cockpit (and the dashboard within) to tilt down. “It’s just the matter of having a well-planned installation,” Belloni says, “so even if the cockpit is tilted, you have good position accuracy.”
The outdoor environment poses its own challenges, the company adds. Throughout the course of the year since the system was taken live, Belloni says, the Quuppa Locators have sustained 20 typhoons. One especially heavy wind broke a bracket supporting one gateway; however, the gateways were unaffected.
In the future, Morita Group plans to integrate position tracking data between its factories, as well as capturing and sharing such data from some suppliers. Konno adds that the system could be employed to identify the locations of workers wearing BLE badges, for safety purposes.