EchoRFID, a Colorado company founded by veterans of the oil and gas and radio frequency identification industries, is currently in discussions with potential clients to begin piloting an RFID and GPS solution, dubbed the EchoShield PipeTalker, that manages pipes and other equipment for oil and gas pipeline owners and operators. The solution has been five years in the making, according to the company, and was tested at a Colorado installation to determine whether tagged pipes could be located, and data related to those pipes accessed using a combination of RFID and GPS data.
With the solution, the company offers its own cloud-based server to host software tracking location and historical records for each tagged item. The solution also comes with EchoRFID’s its own patented reading devices that incorporate a GPS unit and an ultrahigh-frequency (UHF) reader to provide location data, as well as Omni-ID Dura 3000 and Dura 1500 on-metal passive EPC Gen 2 tags. The system includes ODIN Technologies software (ODIN partnered with EchoRFID to develop the solution) to manage the capture and interpretation of RFID data.
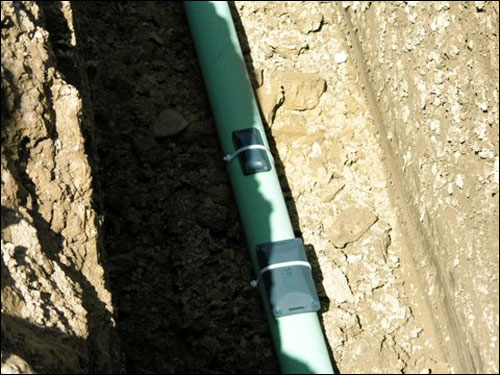
Tracking pipes before and after underground installation is a challenging task for the oil and gas companies, EchoRFID explains, as well as for distributors and companies that provide further services to the pipes, such as the application of coatings, and also transport and store the pipes prior to their installation at a work site.
Approximately five years ago, a team of individuals from the oil and gas industry began building a software-based solution that could provide employees with a list of steps to follow while installing or maintaining pipes. At a construction site, workers could open the software on a PDA and follow a menu of tasks, responding to each prompt to indicate that a specific step was completed. However, the company decided that it would be good if the solution were designed to automatically trigger the listing of tasks, in order to ensure that all necessary work was carried out. What evolved is the marriage of two technologies: RFID and GPS.
The challenge, according to Layne Tucker, EchoRFID’s CEO, is that once a tagged pipe is buried, the tag can no longer be read. As such, identifying the pipe’s location would be difficult for workers, equipped with a handheld reader, who are conducting inventory counts or seeking to locate a specific section of piping or equipment for maintenance purposes.
The solution to that challenge is a GPS unit installed in the EchoShield PipeTalker handheld device, which also includes an RFID reader—the EchoShield PipeTalker handheld is available with a variety of reader makes and models. EchoRFID’s sister company, ProStar (cofounded by Tucker), provides the GPS mapping software, known as Transparent Earth, used in the solution. By reading a tag and linking its ID number with the reader’s longitude and latitude coordinates, the PipeTalker software—which operates both on the cloud-based server and on the handheld device—can store the pipe’s location. Later on, workers can use the handheld’s GPS function to identify the location of a tagged piece of pipe and, if appropriate, automatically call up a list of steps or answer questions about the processes being undertaken. They could also load photographs, video or vocal recordings about the pipe’s location and installation. By identifying the tag—either via the handheld’s RFID reader or its GPS unit—the system would automatically instruct the employee what to do regarding that tag’s pipe, and solicit information about the actions he or she takes. “The tags provide a definitive trigger mechanism” for construction personnel, says Andre Cote, Omni-ID’s VP of business development, who worked closely with EchoRFID during the solution’s development.
Although there are different scenarios in which the PipeTalker solution could be used, it is designed to enable the tracking of a piece of equipment or pipe from “cradle to grave”—in other words, from the point of manufacture to the installation site. Such a solution would likely be driven by the oil company, that might request or require that its providers tag products at the time they are manufactured. Initially, however, EchoRFID expects the technology to be utilized by an oil company from the point at which it receives goods from a supplier, with the oil company or a third-party firm applying a tag to every item as it is received at a warehouse or construction site.
Ultimately, however, EchoRFID expects that the pipe manufacturer would attach an RFID tag to each piece of pipe and link that tag’s ID number in the software to two critical pieces of data: the date of manufacture and the heat number (which is typically stamped on a material plate after it is rolled at a steel mill). The tag could then be read during quality-assurance checks and shipping. Once the pipe is shipped to a coating company, staff members at the receiving location could read the tag as well; identifying the coating processing being performed, as well as when this occurred and with what material. The tag could also be read to track storage locations if a pipe waits within a warehouse, and when it is shipped to the user—an oil and gas company or utility firm. What’s more, the GPS data could be used to pinpoint the item’s location as it is processed or stored. If the object is being stored within a covered area, Tucker explains, an additional GPS unit could be deployed outside the building, in order to send its coordinates to the handheld reader.
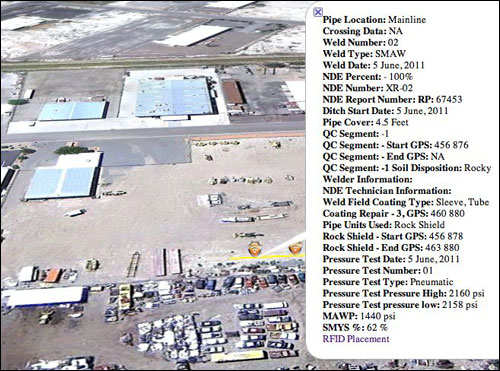
Once the pipe or other item is shipped to a work site, staff at that location could then use a handheld to capture all ID numbers at once (for example, there could be 100 pieces of equipment within a crate that could be interrogated simultaneously) and create a record of which goods had been received, along with their individual supply chain histories. When the pipe is being installed, workers would then read each piece’s ID number once more, and transmit that data back to the server via a GPRS connection, along with the GPS coordinates. Information can also be stored on the handheld device if there is no network connection, and then be uploaded to the software at the end of a worker’s shift.
When an inspector searches for pipes that may be installed underground, he can simply access the software via his handheld PipeTalker device, and identify the location of each RFID tagged item within his own area. Because each object’s exact GPS coordinates is linked to a specific RFID number, he can then know which pipe he is standing on or driving over, without having to read its RFID tag through the ground.
The solution also enables the tracking of personnel via EPC Gen 2 passive RFID badges. In this case, a user could read his own RFID badge while conducting the maintenance or installation of a piece of pipe. If that individual were not authorized to accomplish the task at hand—due to his not having the necessary training, for example—he would receive an alert on the handheld prohibiting him from proceeding with that action. Management could also receive an alert via e-mail or text message.
The technology has been trialed by EchoRFID at site owned by Petty Construction, a Grand Junction, Colo., company owned by Tom Petty, one of the EchoRFID’s founders. During the trial, Cote says, pieces of plastic and metal pipe were fitted with about a dozen RFID tags and placed in a trench dug into the ground, and each tag’s ID was read and linked to a GPS location, in order to create a record of that particular section of pipe. The trench was then filled in with dirt, and the tagged pipes are currently still in the ground. Some of them are under only a few feet of soil, Cote notes, and can be interrogated using a reader without being unburied. The tags may be removed and tested sometime in the future, he adds, but such plans have not yet been solidified.
EchoRFID’s goal is to create a single solution that would allow the tracking of a single item throughout its lifespan by multiple players, including manufacturers, distributors and owners of the construction site. In addition, if a property were sold to another business, the buying company could have an electronic record of exactly which pipes were installed at that location, where they were, and their inspection, maintenance and manufacturing record.
Although EchoRFID is using Dura 1500 and 3000 tags with the solution, Tucker says, due to their rugged form factor and read range on metal, other tags could be used if customers had their own tag provider, as the solution is technology-agnostic.
Once the technology is adopted, Tucker says, it could serve to make field operations at a construction site more transparent, by enabling management and field staff to access data regarding each piece and its history. It could reduce the risk of equipment being misplaced, and provide detailed electronic records about above- or belowground assets onsite when companies are negotiating land development or identifying a property’s sale price.
James Anspach—a claims consultant and utilities expert witness, as well as a senior fellow and the director of utility market and practice development at civil and environmental-engineering company Cardno TBE—notes that the new solution comes at a time at which demand is ramping up in the oil and gas industry. “There are 50,000 miles of pipe going into the ground in Pennsylvania alone every year,” he states, “with none of them being documented well.”
The tracking of underground pipe is a safety concern above all else, Anspach says. “The ability to utilize programmable geo-referenced RFID tags on pipes to assist in many aspects of pipeline integrity management is not only exciting, but of great public benefit,” he states. “In the many fracking locations of the USA and Canada, new gathering and distribution piping go unrecorded, leaving public safety compromised in the future. And the transmission facilities that carry this product to market are even more at risk.”