Bode Technology, one of the world’s largest DNA analysis firms, is piloting an RFID system it developed to manage DNA evidence as it passes through a supply chain, that includes storage and analysis in the laboratory. If the pilot—held at the company’s Virginia lab—goes well, Bode Technology plans to deploy the system for 50,000 or more pieces of evidence annually as they move through the company’s facility. To date, says Randy Nagy, Bode’s sales and marketing VP, the system is reducing the time spent manually recording information about the specimens and their movement through the site, and provides a better, more accurate record of where each specimen has been, and who has been handling it.
The company is marketing the system, known as Bode-RFID, to law-enforcement agencies, for use in tracking physical evidence such as weapons, as well as DNA evidence. This, Nagy says, is being done in order to create and maintain an electronic record of a sample’s movement from a crime scene through testing and storage, with data that could be used in a courtroom if the courts, for example, required proof of where the evidence had been, and when. The system is designed to be flexible (it can be set up to track evidence at specific locations chosen by a user, such as at a crime scene or storage area, or in off-site labs). What’s more, it can act as a module to the existing Laboratory Information Management (LIM) system Bode sells, which stores and manages data regarding evidence for municipal, state and federal agencies.
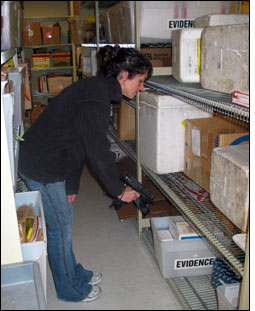
When evidence is gathered, it is typically placed in a paper bag, box or DNA kit, and a unique reference number is assigned to that specimen, either printed in the form of a bar code on an adhesive label attached to the bag, or manually written on the bag using a marker. Approximately 40 percent of law-enforcement agencies currently employ bar-coded labels, while the rest utilize the manual, handwritten method. Often, a law-enforcement official creates a paper manifest with the same reference number, along with details related to that specimen. That manifest then accompanies the specimen when it is shipped to a forensics company, such as Bode, or to an in-house laboratory. The law-enforcement official at the crime scene—and, afterward, the agency or lab staff members handling the evidence—typically put their initials on the paperwork to provide a trail documenting which personnel worked with those samples. Multiple pieces of evidence are often recorded on a manifest, in order to link specimens from the same crime scene, such as several articles of blood-stained clothing. This system is time-consuming, however, and in the case of handwritten reference numbers, there is always the risk that an agency employee creating the manifest could transpose the numbers or otherwise make mistakes.
Another shortcoming with the manual system, according to Andrew Singer, Bode Technology’s senior product manager, is that workers handling the sample may fail to add their initials to the evidence or paper manifest. Consequently, it is not always clear who has been handling a particular sample. In other cases, a piece of evidence can go unnoticed—in the trunk of a car, for instance—but if an RFID system were used at the time that evidence was collected, that type of error would be documented electronically, because a record would be stored in the back-end system indicating the date and time a specimen was gathered, along with any subsequent procedures that may have occurred, including receipt into storage or movement to a lab for testing.
Bode Technology watched RFID technology prices drop, and the demand for such a solution increase, until last year, when it determined that an RFID solution would be saleable. At that point, the firm developed Bode-RFID, which includes the company’s existing LIM system, as well as its RFID-based software (developed in partnership with RFID Global Solution), to interpret RFID numbers as they are read, along with the location and time of read events—all of which is then stored in the LIM system. Bode-RFID will also provide hardware such as tags, readers and printers, according to customers’ specific needs.
Bode Technology decided to first test the system at its own site in Virginia, in order to gather time-saving metrics. Last week, employees began tagging and tracking all new evidence coming from a handful of customers—government agencies that agreed to have their samples tagged and tracked while at the company’s facility. Initially, only Bode Technology will use the RFID read data for its own purposes—to automate the tracking of each specimen’s arrival, testing and storage, as well as who handled that evidence at any given time. However, that information could also be requested from the agencies in the event, for instance, that it is required for a trial.
When specimens arrive, they contain a printed reference number or a bar-coded ID number, along with information about the specimens printed as text on the paper bag or box in which they are contained. Bode’s staff have several options for storing that data in the back-end system. In some cases, an agency sends an electronic manifest to the company prior to the samples’ arrival. When that occurs, the electronic manifest provides Bode Technology with details regarding the sample, including the case number, a list of other pieces of evidence linked to that case, the agency that had sent it, and the specific testing required. Workers can then open the electronic manifest on the LIM system and enter information about the carrier (such as Federal Express) and the time and date of its arrival, or scan the carrier’s bar-coded label on the item’s packaging using a handheld Motorola MC9090 to create a record of that item being received.
In either case, an Avery Dennison ultrahigh-frequency (UHF) Gen 2 RFID tag is then printed and encoded with a unique ID number on a Zebra Technology printer, and attached to the paper envelope or box in which the specimen is stored, thereby linking the RFID number with the sample it is attached to. If no electronic manifest is sent to Bode Technology before the sample’s arrival, the company’s staff inputs all of the information printed on the packaging or paper manifest accompanying the specimen, again encodes an RFID label and affixes it to the specimen’s envelope or box. If the agency had used an RFID-enabled handheld device at the crime scene, attaching an RFID tag to a piece of evidence as it was gathered, and then reading the tag at the scene, Bode’s employees could simply read that tag when the specimen arrives at the facility. Bode-RFID software enables a user to read the RFID tag, view an electronic manifest of the evidence, and then follow instructions in a drop-down box to indicate the event that is occurring, such as receiving the specimen from the carrier.
The sample is then moved into the evidence room, where it is stored while not being tested. As it passes through the doorway into the evidence room, it passes through a portal built by Jamison Door and containing an Impinj RFID reader. The ID number is transmitted to the LIMS on Bode’s back-end server via a cabled connection, indicating it has arrived at the evidence room. LIMS can then determine the direction in which the tag is moving, based on its location and the data related to its last read. All information is automatically exchanged between the Bode-RFID software and the LIMS, Nagy says.
In addition, each employee wears an RFID-enabled badge, the ID number of which is also read, thereby indicating which employee brought a particular item into or out of the evidence room.
When an item is checked out by a DNA analyst, it again passes through the evidence room’s portal and is then taken to the laboratory, where a desktop or handheld reader is used by the staff each time the evidence changes hands. If there are multiple bags of evidence connected with a specific case number, information about the additional evidence related to a specific item is also stored in the LIMS. All of these pieces of evidence are tied together in both the RFID software and the LIMS.
If a DNA analyst goes home for the day before finishing with a particular piece of evidence, he or she can take it to the temporary evidence room within the laboratory, where another RFID reader portal captures the ID numbers of the specimen’s tag and the employee’s badge, indicating when it was moved into the storage area, and by whom. This security measure, Nagy explained, is intended to track which individuals had the evidence when it came and went, as well as track which personnel had access to specimens stored in the room while it was there. The sample can then be removed again the next morning for further testing.
If Bode’s staff require a specific piece of evidence, they can utilize the Motorola handheld reader that they carry into an evidence room or through the lab, and receive an audible alert when it comes within range of the ID number being sought, with the alerts getting louder and more frequent as the reader approaches the tag in question.
Prior to using the RFID system, Bode Technology’s staff would manually input data in order to create a record of each item’s arrival. The company maintained a written record of what occurred for such events as a lab worker analyzing the specimen, or an item being placed in the evidence room. Seeking specimens was more time-consuming, Nagy says, since they had to be searched for visually, without the aid of the handheld reader. “RFID will save a few seconds in completing each transfer,” he states, “and records will be more legible, including the records provided to our customers, which will look more professional.”
The electronic data stored for each specimen as it moves through Bode Technology’s facility, Nagy says, “will better show who had access to all evidence during the time that it was at Bode. The expectation is that this will help improve the already high level of trust our customers have in Bode, and how we handle their evidence.”
To date, Bode has incorporated the portal system only in its primary evidence room, as well as in the room within its lab used for temporary evidence storage. However, Singer says, other forensics companies or agencies could have the technology incorporated throughout their facilities, to track movement through the buildings and between departments.
Eventually, Nagy says, as the time-savings and improved accuracy are proven, Bode Technology hopes to begin tagging all evidence upon arrival, and then track each specimen as it moves through the evidence rooms and laboratory.
Although there are currently no agencies using this system, Nagy notes, Bode Technology is in discussions with many agencies about the prospect of doing so. This fall, as funding is granted to many agencies from the federal government to increase efficiency, Nagy hopes Bode will begin installing the solution with some of the company’s customers. The system is commercially available now, he says, and can be used to track not only evidence, but also case files related to that evidence.