A stream of trucks arrives at Florida mining company Palm Beach Aggregates to pick up one of approximately 20 different products, loaded in quantities specific to each vehicle’s weight limits, and destined for a variety of customers. On any given day, about 100 to 150 such trucks move through the facility and are loaded as ordered by the dispatcher. To help loader operators identify which product, and how much of it, should be placed on a particular vehicle, the company is employing Bluetooth Low Energy (BLE) beacon technology supplied by its management software provider, TACinsight.
Palm Beach Aggregates processes about 2 million tons of crushed limestone, sand and other materials for use in asphalt, cement and concrete products, and as base materials for building foundations, as well as for roads. The company’s products are often used for Florida Department of Transportation (FDOT) projects, which must meet specific material requirements. When a truck arrives at the facility, says Albert Moragues, Palm Beach Aggregates’ project manager, it is weighed and the dispatcher assigns that vehicle to a specific location, where it is loaded with a particular product to transport to a designated destination, such as a customer’s construction site. If a truck becomes overloaded and material needs to be taken off, that removed material can no longer be sold as FDOT-certified.
The trucks queue up at the loading area for the appropriate material and wait to receive it. Loaders then fill up the vehicle with that material (without an automated system, they previously used the weight limit printed on the side of the truck as a guide to indicate how much to load). The truck is then weighed again on its way out of the facility.
This process can lead to errors, the company reports, such as the wrong product, or too much or too little material, being loaded onto a truck. If the amount of material is excessive, the driver must proceed to a dumping area to discharge the surplus. Since that material often cannot be reused due to FDOT requirements, a single error can cost the company hundreds of dollars.
TACinsight offers software for quarry, mining and construction customers, according to Mike Mendiola, one of TACinsight’s co-founders. The firm has been providing RFID-based solutions for about 10 years—typically, active RFID tags with fixed readers. RFID readers are usually expensive and cumbersome to set up, Mendiola says. In the case of Palm Beach Aggregates, fixed units would need to be installed in individual loaders. “The RFID reader needs to be mounted, powered and cabled to the operator interface display,” he states. What’s more, the reader needs to be connected to the device on which the application is running.
The solution was Bluetooth Low Energy, says Steve Rasmussen, another TACinsight co-founder. “BLE was intriguing,” Mendiola adds, “because we could use an off-the-shelf phone or tablet as a reader, and in that way, integration becomes much more simple. We could then build an app to bring beacon information to the loader operator. The use of BLE through commonly available smartphones or tablets enabled us to eliminate a costly external component [an RFID reader] and greatly simplify the deployment.”
Each truck has a GeLo Bluetooth beacon attached to its windshield. Approximately 250 beacons have been distributed to truck drivers to date. The beacon, powered by AAA batteries, transmits an ID number about once per second. The beacons are set for the longest read range, Mendiola says, providing between 150 and 250 feet of range. The battery’s lifetime is expected to be two to three years.
Upon arrival at the quarry, a driver first reports to the scale house, where the truck is weighed. At that location, the dispatcher has an Android-based tablet running the TACinsight app. The tablet receives the ID transmitted by that vehicle’s beacon and makes what the company refers to as “a Web service call” (sends that ID to the cloud application’s “truck in yard” list). When the dispatcher enters the empty truck’s weight, as measured by the scale, and assigns the hauling order into TACinsight’s truck-scale ticketing software, the information is forwarded to the hosted cloud application and is also made available to the loading units in real time.
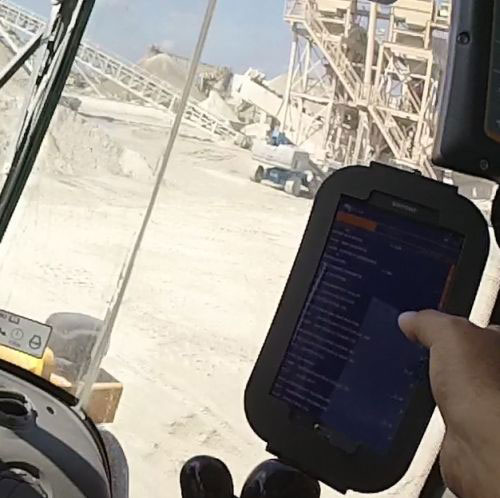
Upon receiving an assignment from the dispatcher, the driver proceeds to the loading area and parks in the appropriate location to await his turn for loading.
Installed inside the cabin of each of the site’s four loaders is an Android-based tablet, on which the TACinsight app is running. Each loader operator is responsible for several types of product, and must determine if the truck is parked in the proper location to receive one of his products, as well as which materials should be loaded. Once each truck’s beacon comes within range of the tablet, the app displays data related to that vehicle, including not only the name of the company and the truck’s serial number, but also the vehicle’s capacity and the product type that it needs.
The system lists each truck whose beacons are being identified, arranged in order according to read strength. Thus, the closest truck appears at the top of the list. The loader app polls the cloud-based software for all trucks currently in the yard, and also reads any BLE beacons in the loader’s range, along with the signal strength. The software uses the signal strength to determine which vehicles are closest to the loader, and then pushes those trucks to the top of the loader’s list.
While loading the truck, the operator follows prompts instructing him to indicate on the tablet the type of material he is loading into the vehicle. That data, along with the loader’s identity and a time and date stamp, are stored in the software.
If the loader operator notices a discrepancy between the order data on his tablet and the actual truck in front of him, he can place a phone call to alert the dispatcher to the problem.
Once loaded, the truck is moved to the scale to be weighed again, and that information is stored in the TACinsight software. The historical data can be used to better manage the loading operation, Moragues says. For instance, the company knows when trucks arrive, how long it takes for them to be loaded, when they have undergone the second weighing process before leaving, and who loaded each truck. With this data, the firm can identify bottlenecks, as well as which loader operators are working faster or slower than others.
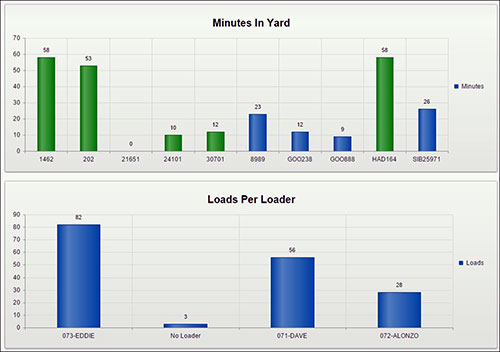
Moragues says most trucks move through the entire process of loading and weighing in about 15 minutes, though he would like to see that time shortened by improving efficiency, thereby ensuring that customers are served more quickly.
TACinsight chose the GeLo beacon because it was ruggedized enough for the construction environment. The company also liked the fact that the batteries were standard AAA and easily replaceable onsite. The GeLo beacons are designed to be rugged, says Al Juarez, GeLo’s sales and business-development director. When TACinsight approached GeLo, he says, “they were searching for a rugged, durable water- and dust-proof beacon with strong battery life. Given the hot, humid, dusty conditions and the jarring the beacons have to endure because they are mounted on gravel-hauling trucks, TACinsight concluded that GeLo beacons met their requirements.”
The solution was taken live in late February 2015, and is still transitioning to a full deployment as more trucks use the beacons. To date, Moragues reports, “everything is really working out well. I can say we’re seeing benefits.” One benefit, he notes, is a reduction in material-loading errors. He says his company’s dispatchers are receiving more calls from operators prior to loading, with questions about a specific load, and that each call represents a potential error that was prevented.