In today’s complex business environment, managing by crisis or firefighting to achieve a target is never the recommended method of managing production. Instead, the setting of clear objectives can help deliver a product to a customer on time, and in the proper quantity and quality. The better able a company is to achieve 100 percent on-time delivery (OTD), the more likely it will satisfy its customer and thereby retain and expand its market share. In the light of managing by objectives, real-time information regarding key performance indicators (KPIs) is pivotal for driving processes toward meeting a company’s production targets. Radio frequency identification can play a critical role in providing a firm with this real-time information.
Once a company has set organizational objectives, it can periodically compare them against individual performance, and determine if additional training and other measures are required for employees who have not yet fulfilled those objectives. Only by maximizing individual performance can any business achieve its strategic goals.
In February 2008, the production staff at a leading garment factory in Sri Lanka tested the use of RFID on a selected sewing line, in order to prove to the plant’s top management the value of real-time information in managing production by objectives in a real-world scenario. The project—initiated by my company, Sabre Technologies, as a free-of-charge pilot—had a great deal of support from me, as well as from Sabre’s technical staff, backed by a senior-management team.
The pilot was organized to track sewing operations at line-in (a point in the assembly line at which bundles of garment components are fed into the line) and at line-out (where finished goods are inspected for quality). Each point had its own RFID reader. A third RFID reader was installed after the line-out reader for the purpose of de-allocating RFID tags. Apart from the readers, there was a display board hung up at line-out to indicate real-time efficiency, each shift’s target, cumulative actual output and cumulative defective percentage, as well as alerts for open down time, lost time, overproduction, underproduction, work-in-progress (WIP), garment rejects, panel rejects and absenteeism. This helped supervisors and sewing-machine operators know, in real time, whether the above production KPIs were within tolerance during production.
Each sewing operator was provided with an RFID tag, which she scanned via the line-in reader before beginning to sew, to indicate that the employee had come to the production line to work, and enabling the system to calculate the important KPI of absenteeism. Upon finishing a shift, the workers tagged themselves out on the line-in reader. This helped calculate individual minutes worked, as well as the daily team-based incentive for the operators.
In garment manufacturing, one bundle includes all components required to complete a particular number of clothing items. For example, if the bundle size is 50, that means the bundle contains all of the components necessary to complete 50 garments. During the pilot, a tag was not physically attached to each individual piece of clothing, but was allocated to a particular bundle. The tag was tied to that bundle with a cord, and was transferred to the sewing line along with the bundle. The tag carried a pouch that held a piece of paper printed with all information pertaining to that bundle.
After tagging herself in, the operator at line-in fed the garment-component bundles into the production line, and scanned the respective bundle tags on the line-in reader in order to indicate WIP within that line. Upon receiving the finished garments, the line-out operator entered the number of defects and the quantity of defective garments into the system, and the clothing items were then sent back to the sewing operator to be reworked. The passable (defect-free) garments were “tagged out” by passing them by the line-out reader. Once the reworked garments were returned to the line-out point, the operator at that location tagged them out, if the defects had been rectified. After the garments were tagged out by the line-out reader, the cumulative actual output was indicated on the display board, while cumulative defective percentage was displayed every time the defective statistics were entered into the line-out reader.
Whenever a machine went down, a line supervisor scanned a “down-time” RFID tag on either the line-in or line-out reader, in order to indicate the machine’s status. The moment that the downtime tag was scanned, a mechanic was sent an e-mail alert, triggering that individual to come to the line as soon as possible and fix the machine. Upon arriving at the line, the mechanic scanned his RFID tag on either of the two readers, and then began mending the equipment. Once the machine was fixed, the mechanic tagged himself out, and the supervisor scanned the down-time tag back, thereby confirming that the machine was again functioning properly. All of the RFID tags used for the pilot were low-frequency (LF) non-washable passive tags, while the readers utilized were LF devices manufactured by Sabre Technologies.
During the pilot, hourly e-mail alerts regarding the following KPIs were sent to the production and management teams:
• Planned shift efficiency versus actual cumulative efficiency
• Target cumulative output versus actual cumulative output
• Planned lost time versus actual lost time
• Target quantity of defective pieces versus actual quantity of defective pieces
• Planned defective percentage versus actual defective percentage
The real-time information on production KPIs for the selected sewing line was made available to the operators, the team lead, members of the shop floor staff, shop floor executives, production managers and senior management, through an electronic display board mounted at the end of the sewing line, as well as via e-mail alerts. The display board displayed actual real-time line efficiency and defective percentage, as finished garments came out from the production line, while e-mail alerts were sent to production managers and senior management every 30 minutes, regarding actual efficiency versus target efficiency, as well as actual defective percentage versus planned defective percentage.
The operators and the line supervisor for the selected production line could view real-time efficiency and defective percentages on the display board, compared against set targets throughout the shift. This helped the staff know whether or not they were on par with the target efficiency and defective percentages, as well as whether they were lagging behind the target, thus enabling them to immediately rectify the root causes in order to get their performance back on track before it was too late.
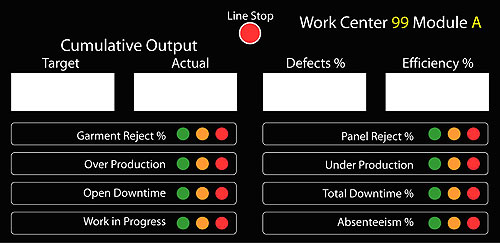
Moreover, e-mail alerts sent to production managers and senior management triggered operational-level decision-making at the right time, thereby ensuring that the selected production line was driven to not only reach the target, but go beyond it. This access to real-time information—which led to managing by objectives through effective decision making with the correct information at the proper time—increased the production line’s average efficiency to 53.18 percent, compared with an average efficiency of 32.26 percent for the previous month (when the staff lacked access to real-time information), while decreasing the average defective percentage to 2.45 percent, compared with 5.26 percent for the month prior.
Pilot findings concluded that real-time information made available through RFID technology immensely contributed to managing by objectives, through correct decision making with the right information at the proper time, as opposed to making decisions with the benefit of hindsight with not-so-reliable, manually summarized information
Amila Nandasekera is a senior RFID implementation consultant at Sabre Technologies, a division of MAS Holdings Ltd., in Sri Lanka.