Last week, I attended the sixth annual Augmented World Expo, a technology conference at which representatives from the augmented-reality (AR) and virtual-reality (VR) industries show off their wares and measure the in-roads that the technologies are making in the gaming industry, in enterprise applications and in many other areas.
In case you’re unclear on the difference, in augmented reality, text or video is projected onto the transparent lens of a pair of glasses or on the screen of a handheld device, such as a smartphone, enabling a user to see not only what is in front of her, but also the projected information. In virtual reality, the user wears opaque lenses in order to create an immersive view of information or imagery projected in 3D onto the glasses’ stereoscopic display.
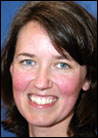
I had come largely to attend a session called “Internet of Things and AR,” but the session room was already overflowing when I arrived five minutes before start time, and I could not even shoulder my way in. It was a real bummer. But I reached out to the speakers and heard back from one: Simon Heinen, the founder and CTO of bitstars, who shared with me the slides and video from his presentation.
Bitstars, based in Aachen, Germany, offers an online photo-stitching tool known as Holobuilder, which can be used to create either virtual- or augmented-reality videos. The company also offers a service by which it will create an AR or VR app for mobile phones, smart glasses or smart watches. A customer provides bitstars with media for things like instructional, safety or operational manuals and maintenance checklists, and bitstars then uses Holobuilder to incorporate that content into the app.
Once an AR or VR video is generated, bitstars overlays graphics to illustrate information about the thing being viewed—for example, it might show an alert indicating that a part of a machine has overheated, based on a sensor reading that the smartphone, glasses, watch or VR viewer is receiving wirelessly. In other cases, instructions on how to interact with the item—how to remove and replace a part, for example—are displayed, with the user being able to scroll through, step-by-step. The IoT technology in these scenarios includes not not only sensors but also phones, glasses or other devices, through which the AR or VR information is conveyed.
It’s pretty snazzy stuff, and a number of other companies that presented at various sessions offer similar and, in some cases, far more elaborate solutions. This type of technology shows a great deal of promise, in terms of reducing workplace errors and improving operational efficiency.
Paul Davies, who works in the Research and Technology Group at Boeing, shared results from a pilot program that the company conducted along with researchers from Iowa State University, in which individuals were asked to assemble a mock airplane part, with 30 parts and 50 assembly steps. One group used text-based instructions displayed on a computer monitor a few steps from the assembly table; a second group utilized the same document on a tablet computer right next to them on the assembly table; and a third group employed a prototype AR view, using a tablet that they could hover over the parts to visualize each assembly step.
Each person was asked to assemble the part twice. The group using the instructions displayed on the computer monitor made an average of eight errors on the first try and four on the second. The group using the AR instructions? It made just one error, on average, on the first try and zero on the second. If Boeing moves beyond this kind of rudimentary AR test, it seems likely it would use the technology with hands-free devices, such as glasses. Earlier this year, the company posted a video describing how employees are trying out Google Glasses to guide them through the steps for assembling a wire harness. This lets them rely on voice commands and visual instructions displayed through the glasses, rather than on their existing paper-based directions.
“The 787 is the most complicated plane we’ve ever built,” Davies said. “But [assembly] instructions are still conveyed in 2D.”
A single assembly error can cost Boeing hundreds of thousands of dollars to rectify, he said, “so if you scale [AR] out, we’re talking about a huge value for us.”
The potential is very exciting, but Bob Meads, the CEO of a company called iQagent—which designs AR displays and interfaces for factory maintenance workers—provided a little dose of reality when it comes to the basic wireless networking required to support AR systems that leverage sensor networks and data-rich video streams. Some of the companies that he works with still have archaic rules, he said, such as not allowing cameras to be carried onto the factory floor (due to concerns regarding the protection of intellectual property), while others have yet to even install wireless networks within their facilities.
So for all the talk and hype about the Industrial Internet and Industry 4.0, it was a reminder that manufacturing companies are not all on the same page.
Mary Catherine O’Connor is the editor of Internet of Things Journal and a former staff reporter for RFID Journal. She also writes about technology, as it relates to business and the environment, for a range of consumer magazines and newspapers.