Last week, The New York Times reported that the National Football League (NFL) was putting radio frequency identification transponders in footballs, not only to automate the tracking of how many times a quarterback throws a ball, but also to monitor the ball’s speed, the height of the throw and perhaps whether or not the ball crosses the goal line (see N.F.L. Expands Use of Chips in Footballs, Promising Data Trove).
RFID Journal reported a year ago that tagged footballs were being tested (see The NFL RFID-Tags Its Footballs). The decision was made to tag the balls follows the NFL’s introduction of ultra-wideband (UWB) active RFID transponders on players’ shoulder pads in 2014 to track them during games, and to provide statistical information that wasn’t previously available (see RFID Drafted to Track NFL Players’ Every Move During Games and The NFL’s Next-Generation Statistics).
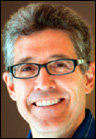
Does the use of RFID transponders to track players and balls have any relevance to companies that don’t run sporting franchises? I believe it does. Airbus has used similar tags on people in at least one of its aircraft assembly facilities in Europe to conduct a highly detailed and precise time-and-motion study. One insight the company gained was that workers were spending a lot of time walking back and forth to a tool crib to check tools in and out. The crib was thus moved to a location closer to the line.
Active UWB technology provides very precise location accuracy, often down to within 10 centimeters (3.9 inches), which means companies can get detailed information on how items move through a facility. This can be used in many different ways. Boeing, in fact, decided to deploy the same system from Zebra Technologies that the NFL uses after learning about the player-tracking solution.
Boeing’s concern was for the safety of its workers painting new aircraft. Employees painting airplanes stand on platforms that move up and down and around each plane. They are required to wear harnesses, and spotters ensure that workers don’t accidentally interfere with each other. But the system was not foolproof, so Boeing adopted the UWB RFID system to ensure that workers have their harnesses on and are not in danger of interference (see Zebra’s Painter Protection System Helps Prevent Falls at Boeing).
Companies that operate factories with multiple lines could use a similar system not just to track parts bins, vehicles, large tools and individuals, but also to monitor subassemblies and work-in-process through each line, in order to determine how much time a product being assembled should take at each station. If a product takes longer to get through one station, the company could provide additional training for workers at that station, or replace someone with a more qualified employee.
RFID technology’s ability to provide visibility into the movements of objects can be utilized in a variety of ways to optimize operations. Companies that add new technologies to their playbook just might have a better chance of running up the score.
Mark Roberti is the founder and editor of RFID Journal. If you would like to comment on this article, click on the link below. To read more of Mark’s opinions, visit the RFID Journal Blog, the Editor’s Note archive or RFID Connect.