At RFID Journal events held a few years back, there was often a lot of discussion regarding how to get radio frequency identification technology to work properly. Companies talked about how they overcame issues of water and metal in their environment or the inability of an active real-time location system to accurately locate tagged assets. Last week, we held RFID Journal LIVE! Europe, our 11th annual event in the region, and there was almost no discussion about the technology. The focus was on people and process.
Dr. Bill Hardgrave, dean of the Harbert College of Business and founder of the Auburn University RFID Lab, brought up these issues during his keynote address. He told the audience that whenever a company visits the lab and says it has conducted a proof-of-concept or a pilot that has failed, his team will dig into the reasons for that failure. “And in almost every instance,” he reported, it is due to human error.”
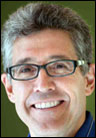
One example Hardgrave offered is a retailer relying on store associates to count inventory using handheld readers but their failing to do it properly, either when or how they are supposed to. “That’s not the technology’s fault,” he said. “That’s human error.”
Another problem, Hardgrave said, is that companies sometimes overlay RFID on top of existing bar-code practices. That approach does not maximize the benefits that can be obtained from using RFID—and, in fact, it probably minimizes them. Worse, Hardgrave said, that approach “can enhance any process issues that you have.” He suggested companies look at RFID as a way to improve existing processes.
Hardgrave described an audit the lab conducted for one retailer that had only a 75 percent accurate rate from RFID, which is extremely low (95 percent or better is common). The audit found that 2.5 percent of the time, an item was not detected because it had no inlay. In a small number of cases, the reason was that a customer had returned a product without its tag, but mainly it was because the supplier hadn’t tagged the item.
In roughly 1 percent of the cases, there was no tag or bar code. In 0.3 percent of the cases, there was an issue with how the tag was encoded. The biggest problem was that 21 percent of the items had two tags, due to employees not being aware that the supplier had tagged an item, and thus putting on a second RFID tag. There were actually no dead tags found, and only 0.5 percent of the tags were not read during a cycle count. If the retailer were able to get suppliers to tag properly and eliminate the double tagging, accuracy would jump to that 95-percent-or-above level.
Other speakers also addressed these issues. Some retailers said they were considering switching from handheld readers to a more fixed infrastructure due to the challenges with ensuring cycle counts are conducted properly and in a timely way. Retailers, for example, often display women’s ensembles in four or five different areas of the store, as opposed to one area for sweaters, one for jeans, one for dresses and so on. One challenge is making sure that when store associates take inventory of, say, women’s sweaters—or “jumpers,” as they say in England—they count all of the items in all areas of the store.
RFID almost always involves process change. That means employees need to be trained to use the technology and to follow the new process. Controls should be put in place to check that workers are following that process. This is not a huge challenge. In most cases, employees like RFID because it makes their job simpler and easier, and they can concentrate more on serving customers. But companies that don’t do the training will likely have problems.
The point of this column is not to say RFID is perfect or to shift the blame for issues onto the users. Not at all. It is simply to point out that RFID is a very powerful tool, but for it to work properly, people have to be trained to use the tool and to follow the processes that make it effective.
Mark Roberti is the founder and editor of RFID Journal. If you would like to comment on this article, click on the link below. To read more of Mark’s opinions, visit the RFID Journal Blog, the Editor’s Note archive or RFID Connect.