I have been covering radio frequency identification technology every day for the past 18 years. This week, I will be hosting RFID Journal’s 17th annual RFID Journal LIVE! conference and exhibition. I look forward to this week each year, because I get to interact with our readership, as well as solution providers. But most of all, I enjoy the opportunity to learn about RFID technology.
You might think, with my having sat through hundreds of RFID presentations and case studies throughout the past 17 years, that there isn’t much I haven’t heard before. It’s certainly true that there are a lot of similar characteristics among deployments and RFID products. But I always end up feeling, after the conclusion of our annual event, that I learned a bunch of new things and viewed a lot of new products.
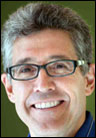
Sometimes, what I learn is highly technical, such as that an antenna has a theoretical invisible state, or the dielectric constant of water is 78 but the dielectric constant of ice is about 3, which is why you can read tags on frozen foods more easily than on fresh foods. (Dielectric constant, I learned a few years ago, is the ability of a substance to store electrical energy in an electric field. A high dielectric constant means the material has a greater ability to conduct electricity and, therefore, detune an RFID tag or direct energy away from the tag antenna.)
More often, what I learn relates to companies deploying RFID and finding ways to make the technology work for them, or doing things that maximize the chances of having a successful deployment. One hospital that deployed an active RFID-based real-time location system (RTLS) to track assets had heard that other medical centers had low usage rates. Nurses didn’t learn how to use the system, so they didn’t take advantage of it. Thus, the hospital had the company that deployed the solution sit at each nurses’ station for several shifts to show the staff how to find equipment by logging into a secure portal with the RTLS data.
I often find products that I didn’t know existed. A few years ago, the team at RFMicron showed me a very low-cost passive RFID moisture sensor. Users could take tags made with RFMicron’s chip, embed them in walls and read the tags to know if there was an excessive amount of moisture inside those walls. That might not sound dramatic, but when you first see how they can measure moisture with a passive tag, it’s pretty incredible.
One of my favorite “wow” moments was at LIVE! a few years ago. I visited the booth of a company called Phase IV Engineering, which has since been acquired. I was shown an RFID transponder that was strapped to a piece of rebar. When I turned a wrench and cranked up the tension on the rebar, the passive sensor measured the strain and communicated it to the reader. This means that someday, all buildings within earthquake zones could be built with low-costs sensors. In the event of damage, a drone could be sent into a building with a reader to collect data regarding the amount of strain on the structure and determine if it is safe.
I know that many attendees have a similar experience when they see something they didn’t know existed and find it will work perfectly for an application, or hear something and realize they need to change the way they think about a deployment. These are not things you would see or hear on the Internet, which is why I am glad I get to go to LIVE! each year.
Mark Roberti is the founder and editor of RFID Journal.