The Internet of Things has been receiving a bit of a beat-down lately. In July 2015, market research firm Gartner released its latest Hype Cycle assessment for IoT technologies, which shows about a dozen subsets of the IoT ecosystem on the rise. These include IoT-enabled enterprise resource-planning (ERP) systems and operational intelligence platforms, as well as another dozen sitting at what Gartner calls the peak of inflated expectations. Among these are quantified self (Fitbit, et al.) and Bluetooth beacons. However (cue the ominous background music), machine-to-machine communication services and automobile IP nodes for connected cars are among the eight subsets of the IoT that Garner says are sliding into the trough of disillusionment.
Yet, no one I’ve spoken with in recent weeks is surprised that the IoT is going through some bumpy air; that is what one expects after a technology has been lavished with praise and possibilities while it is still relatively immature.
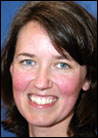
Gartner named just one subset that has already moved through the trough and is climbing up the slope of enlightenment: enterprise manufacturing intelligence.
As it happens, I just spoke with Jennifer Bennett, the general manager of manufacturing software at General Electric (GE), about how the $150 billion goliath for which she works is pushing the 400 diverse manufacturing facilities that it operates to become, in GE parlance, “brilliant factories.” They’re doing this by instrumenting these factories with sensors and analyzing the data they generate in order to improve efficiencies and, eventually, evolve from factories that respond when things or processes break, into predictive operations that prevent downtime by knowing when a system is about to fail.
Bennett made clear, however, that reaching that level of brilliance is not an overnight process, nor is it a cheap one. But she cites two elements that are helping GE inch internal operations closer to that goal.
One of these is Predix, GE’s data analytics software platform, which it developed to use both internally and as part of the consultation services that it provides to its customers. Late last year, GE also began selling the Predix platform by making it commercially available and forming partnerships with Cisco and Intel, through which the Predix software is pre-loaded onto edge devices, such as networking equipment and gateways, used for industrial IoT applications.
Early last month, GE announced that the Predix platform is now available as a cloud-computing service. This means that customers no longer need to host the software on their own servers.
The second element that is helping GE bring its own manufacturing facilities into the industrial IoT, Bennett says, is the use of sensors.
“Think of what Fitbit did for the idea of health and awareness in the consumer space,” Bennett told me. “Before Fitbit, if I wanted to understand my fitness, I’d maybe go to a doctor; I might hire a trainer. With Fitbit, the ability to get some basic health information was suddenly a $60 click away. You put it on your wrist and got basic information [the number of steps taken each day, for example, or sleep patterns] really easily. There was no configuration—I got a dashboard with how many steps I’d taken, and I’d done very little to get that information. And that visibility gets you started on a journey that makes you want to know more.”
Likewise, Bennett said, GE sometimes starts a factory on the path to the much ballyhooed brilliant status by installing a small set of sensors, tracking variables such as vibration or temperature, and using the Predix software to obtain quick access to some very basic but actionable information.
In most cases, that information is really just a teaser; it is not enough to make significant improvements across a facility, but it can pique the operations team’s interest. Gaining visibility into one sliver of a larger manufacturing operation, Bennett explains—which the company did not have before, or could not easily access—makes an impact.
I countered that consumers are fickle and bore easily, and that there are countless Fitbits and other fitness trackers sitting in dresser drawers across the United States right now, because their owners grew disinterested in trying to gleam clues to a healthier life by counting steps and charting sleep patterns. So taking the Fitbit analogy to the factory floor, what is to keep these facilities interested in this slice of visibility?
A bigger investment, Bennett explained: “We’re not trying to go in and optimize [these factories] immediately. We’re trying to get access to some critical information” that the plants can use to tweak a machine or system and see an immediate improvement. But then, they have to do more and invest more.
Those next steps, which allow a factory to move from one-off improvements to systematic changes and eventually to predictive maintenance, takes money and commitment, just like moving from tracking footsteps to improving cardiovascular health takes time and commitment. In either case, Bennett believes, the value is not just in the end results, but in the process of learning and optimizing needed to achieve those results.
So what’s more important? Is it the journey of deploying technology and collecting data to constantly improve a system? Or is the final, optimized result what matters?
The answer, it seems, is that both are the most important—as long as you don’t ditch the technology in a drawer once you’ve grown bored with it.
Mary Catherine O’Connor is the editor of Internet of Things Journal and a former staff reporter for RFID Journal. She also writes about technology, as it relates to business and the environment, for a range of consumer magazines and newspapers.