Nabors Canada, a land-drilling product and services provider, is employing RFID technology to help it maintain and manage the equipment on its drill rigs, located at oil and gas wells across Canada. With the system, provided by TrigPoint Solutions, Nabors Canada’s management can know where its assets are at any particular time, as well as whether they have been maintained and inspected, and when.
The system resolves a labor-intensive problem of tracking the locations, conditions and histories of hundreds of assets at remote sites. Most items, such as generators, pumps and motors installed on oil-drilling rigs, are tracked through paperwork filled out by crews at the drilling site, then manually transferred into Nabors’ database at its office. Management is typically then provided with weekly or daily reports regarding the assets, based on the paper-based records. “What we wanted was a paperless system,” says Joe Bruce, Nabors’ COO. That system, he envisioned, would give his company electronic records pertaining to the location, inspection and certification history of each piece of equipment, in real time.
A typical oil rig has an average of a hundred items that need to be maintained. Tracking all of those assets on each of 86 different drilling rigs across Canada is a cumbersome task for Nabors. Assets can be moved from rig to rig, from a rig to a different part of the drill yard, or from one drill yard to another. These assets often end up missing, a result of their being misplaced or stolen, and are eventually written off and replaced. In addition, the equipment often needs to be inspected, and sometimes certified, by Nabors’ staff or third-party companies, and Nabors must maintain records of those actions.
So in 2008, Nabors Canada piloted the TrigPoint PROMPTT system for six months in the vicinity of Edmonton, Alberta, applying passive 13.56 MHz tags, complying with the ISO 15693 standard, to assets for two drilling rigs, then scanning them with handheld interrogators on-site at the drilling field. The pilot’s success has led to a full-scale deployment that the company is installing now, Bruce says, by tagging approximately 100 assets per oil rig, and 86 rigs altogether. He expects the system to be fully deployed by the end of this year. Once that is done, he notes, the company expects to begin tagging equipment for its well-servicing rigs, used to reinforce the drill hole before oil or gas is removed. Tagging of those components is expected to be completed at the end of 2010.
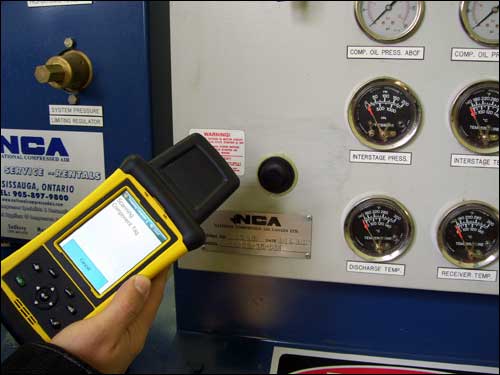
The tags are embedded in a polycarbonate encapsulation created by TrigPoint for drilling rig operations, explains Greg Slater, TrigPoint’s VP of business development. Each tag is encoded with a unique ID number that is linked to information about the asset being tagged. The tag ID number and asset data are stored in software residing on a Web-based site, hosted by TrigPoint. Nabors Canada pays for access to the information, and although Slater declines to define the specifics of the payment process, he indicates it is based on the “pay-as-you-go model.”
Once data is stored in the system, pieces can also be linked to each other in the back-end system, such as a pump that is installed in a specific oil rig also identified by means of its own RFID tag.
At the drilling sites, Nabors’ field workers use handheld interrogators to read the tags. The handheld readers have a wireless satellite communications connection to the back-end server, Slater says, so they can exchange data with the TrigPoint PROMPTT system in near-real time. (TrigPoint supplies all of the RFID hardware, but Slater would not name the manufacturer of those tags or readers.)
Nabors’ field workers scan each RFID tag on a regular basis to provide updated data as to each asset’s location. If an asset needs to be inspected or certified, the handheld unit will send an alert at the time that item’s tag is being interrogated, by indicating the specific service it requires. When a staff member needs to carry out an equipment inspection on-site, he can use the prompts on the handheld device to instruct him regarding how he should proceed.
The system can also be utilized to verify that the equipment meets original equipment manufacturer (OEM) and regulatory requirements—a process that consists of testing the equipment under specific perimeters, then printing a certification indicating the component has passed those tests.
In the future, the company plans to begin using the system for maintenance tracking. If for instance, a component needs to be shipped off-site for maintenance or repair, the tag is scanned, after which data is input indicating where it will be delivered, and for which services. When the component is returned, the tag is scanned once more to indicate when it came back.
TrigPoint is providing the initial configuration of the Web-based site for use by Nabors, which can later modify that configuration as needed. “We configure the entire system—the fully integrated Web-based and handheld application—and then hand [it] over to the client for ongoing configuration,” Slater says. “Our system stores all data associated with tagged assets, what tasks—such as tracking, maintenance, certification or safety—need to be performed, when it needs to be performed and by whom.”
According to Bruce, Nabors Canada has been searching for an RFID solution for some time. After completing the TrigPoint pilot, he says, the company determined that “the system was excellent. Everything we wanted the program to do for us, it did.” TrigPoint provided support in tag placement, he adds, as well as use of the software.