During the past decade, the University of California at San Francisco, dedicated to the health sciences, has transformed the Mission Bay district along the city’s eastern shore. The 57-acre campus has grown into a biotechnology hub for academia and industry. The university’s current project, the UCSF Medical Center at Mission Bay, broke ground in 2010 and is scheduled to open in 2015. The complex will include three hospitals—children’s, women’s and cancer—and is designed to be energy efficient, meet the state’s seismic regulations and provide an urban oasis for the public.
To manage the project, the university took an innovative and collaborative approach to the design and construction of the new medical center. Called integrated project delivery, it involves architects, contractors, engineers and others working as a team to manage processes and production. In this case, 23 firms are working together at the construction site.
That means on any given day, as many as a thousand workers enter and exit the 900,000-square-foot site daily. To help keep all those people safe and secure at the work site, DPR Construction, the project contractor, worked with Trimble‘s ThingMagic division to implement a passive ultrahigh-frequency RFID-based access-control system. DPR installed RFID reader turnstiles at the site’s entrances and exits. The contractor divided the construction site into 19 zones, with RFID fixed readers at the entrance to each zone.
Personnel from the different companies are issued RFID-enabled identification badges that allow them to enter only the work areas they are authorized to access. The security solution also prevents unauthorized personnel from entering the site. In addition, it lets DPR monitor in real time each person’s location, by zone, in the event of an emergency that could require an evacuation or a search-and-rescue operation.
DPR says the RFID solution has bolstered security while reducing related costs. At other job sites, the contractor has to hire security guards and supervisors to manually track workers, a time-consuming process. What’s more, the solution has improved worker logistics. By knowing how many people are deployed onsite daily, and where work has been performed, subcontractors can plan their schedules more efficiently and ensure they are not overstaffing or understaffing the project.
Indeed, securing construction sites has emerged as one of the key drivers of RFID in the construction industry. Some construction firms are also beginning to employ RFID to track equipment and materials to improve job-site operations.
But while these applications deliver substantial benefits, the construction industry is historically slow to embrace new technologies, says Todd Sutton, a business unit manager with San Antonio-based Zachry Construction, which provides construction, maintenance and program management for large-scale projects in the public and private sectors. Sutton believes the only way construction companies are likely to deploy RFID on a large scale is if the technology proves to be effective in fighting counterfeiting, a problem that plagues the industry. He and other industry experts are trying to convince stakeholders, including supply-chain partners, contractors and building managers, that embedding RFID tags in construction materials at the point of manufacture can thwart counterfeiting and enable other benefits, resulting in a return on investment.
Monitoring Construction Sites
There’s a general consensus among those involved that using RFID to control access to construction sites, which tend to be busy, noisy and often chaotic environments, can improve safety and security. But finding the most appropriate tags and readers requires balancing cost and performance. DPR opted to use a passive UHF access-control system. Turner Construction plans to monitor workers at six construction sites, in San Antonio, Tex., with a passive UHF solution from ADR Software (see RFID News Roundup: ADR’s RFID-Enabled Workforce Monitoring Service Keeps Tabs on San Antonio Construction).
Consolidated Contractors Co. (CCC), a $5 billion construction company that employs a workforce of 100,000 individuals for projects worldwide, is testing both passive RFID tags and more expensive, active tags for automating attendance tracking. With an average of 5,000 workers needed over the course of a large construction project, the firm wants to speed up the process of accounting for all personnel, which involves checking each worker’s ID at the beginning and end of each day and when workers leave the premises for lunch.
CCC conducted a pilot project in Abu Dhabi this year that revealed UHF passive RFID tags attached to employee badges could not be read consistently. They found similar results with battery-assisted passive tags. There was simply too much interference from the environment and the workers’ bodies.
CCC then deployed an active RFID access- control system to monitor 500 workers at a job site outside Abu Dhabi. The readers used to collect the data, which are mounted near entrance and exit gates securing the site, are solar-powered. The system also lets CCC verify each worker’s time sheet and show its client the labor budget is being spent properly. The active system provides superior performance, and it saved the firm $6,500 per month by eliminating manual checks of each employee badge, says Firas Hijazi, a manager of information systems at CCC. But, he adds, the high cost of active tags remains a hurdle.
The Abu Dhabi site will require 4,000 workers, so CCC plans to issue lower-cost passive RFID tags, attached to each employee’s hard hat, with passive UHF readers mounted near entrance and exit gates. Meanwhile, the firm continues to test various tags, as it searches for the most reliable and cost-effective solution, Hijazi says.
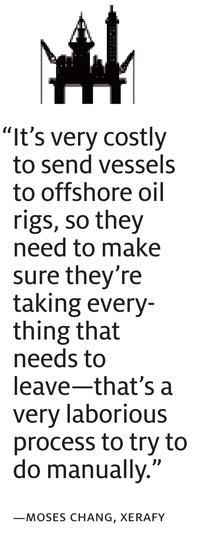
WorleyParsonsCord, a general construction contractor, has been providing equipment and services to the booming oil-sands industry in Edmonton, Canada. To keep 1,000 workers safe at one of its assembly yards, the company worked with John Rustenburg, owner of CJR Backup Safety Solutions, to deploy a Scan-Link system designed to prevent accidents. Employees wear RFID-tagged hard hats and safety vests that communicate with RFID readers mounted inside forklifts and other heavy-duty vehicles. The active RFID technology improves on incumbent sensor-based safety systems used in more than half the heavy-duty vehicles on most sites to give drivers audio alerts when they sense obstructions behind the vehicles, Rustenburg says.
“Those systems alert drivers even when a bird or another vehicle is detected,” Rustenburg says. “The drivers become complacent, and they start to hear it as noise pollution.” Scan-Link alerts drivers only when another employee, wearing a Scan-Link tag, is behind the truck and therefore obscured from the driver’s view. “No one wants to back up a forklift and hit a parked truck, but you can replace that,” he says. “But no one wants to go to an employee’s spouse and say, ‘he is coming home with a leg missing’ or ‘he’s not coming home at all.'”
Managing Construction Equipment and Materials
RFID is also helping construction companies complete projects on time and within budget by ensuring supplies, tools and equipment are located at the right place when workers need them. Atlas RFID Solutions, for example, recently introduced its Jovix system designed to track assets through the supply chain to construction sites. The materials-management solution lets multiple parties—from project owners to engineering firms, contractors and suppliers—access a database to locate assets quickly. The company reports that the solution enabled one of its customers to cut staff at a lay-down yard by nearly 80 percent (see RFID Tracks Assts at Canada’s Oil Sands).
Some large structures are built with prefabricated pieces scheduled to be delivered to the construction site shortly before installation. Typically, these modules are tracked manually with paper invoices, an error-prone process that often leads to costly delays when either the wrong modules are delivered or the items don’t arrive on time.
Gammon Construction has been using an RFID solution from Tecton to tag and track the structural steel components it manufactures and sells for government and private projects in Hong Kong, such as the Opus Hong Kong, a luxury Frank Gehry-designed apartment building. The company reads the Xerafy tags, designed for optimal use on or near metal, at the point of manufacture and again at the job site, to track proof of delivery. The solution can also help contractors comply with recent requirements issued by the Hong Kong government to track building components.
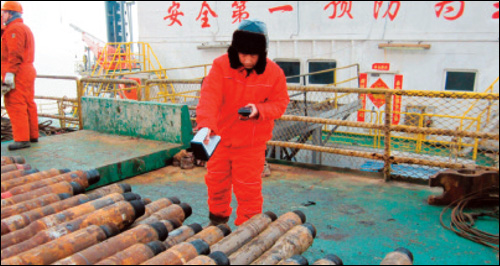
Construction’s Killer App
More contractors might begin tracking assets on job sites if they received tagged supplies from manufacturers. And monitoring tagged products as they move through a long, complex supply chain could help verify the quality and authenticity of construction materials, which is a universal concern. Take, for example, the defective drywall that sickened thousands of U.S. homeowners from 2001 to 2008 and caused many to have to move out of their newly constructed homes. The drywall was branded as a U.S. product, but it had originated in China and contained a filler material that hosted bacteria that caused the products to release hydrogen sulfide gas, which led to sicknesses ranging from nosebleeds to respiratory illness.
In 2011, the Construction Industry Institute (CII), a global consortium of more than 100 leading owner, engineering-contractor and supplier firms from both the public and private arenas, surveyed its members and found that 76 percent of respondents have been affected by counterfeiting. What’s more, of all the counterfeit items discovered within respondents’ supply chains, more than 80 percent came from “approved vendors.”
RFID-tagging construction materials at the point of manufacture would enable companies to authenticate their products, says Zachry Construction’s Sutton. He and Reg Hunter, senior project manager at Fiatech, a consortium of engineering and construction industry leaders, are actively meeting with manufacturers to show them how embedding RFID tags in their products would provide a means to authenticate product, as well as gain a competitive advantage through the value the tags represent to contractors and building owners.
They are trying to reverse the perception that there is an unclear return on investment from deploying the technology. That was one of the findings from a 2011 survey of nearly 150 construction industry stakeholders conducted by David Grau, an assistant professor at the College of Engineering at the University of Alabama, to gauge the state of adoption of RFID and other auto-identification technologies. The survey found that while academic reports have long been singing the praises of these technologies for boosting efficiencies and savings costs in the construction industry, there is a significant gap between research and reality. “We set out to find the barriers and opportunities to accelerate deployment of RFID technologies,” Grau says. In addition to concerns about ROI, he notes, there is a lack of support for the technology among the various parties leading a given construction project.
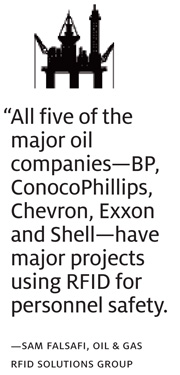
In 2010, RFID Journal reported that Newmans Valves, a Texas-based company, was RFID-tagging valves produced at its factory in Yangchen, China, to assure customers they were buying authentic products and not counterfeits (see RFID Cements Its Place in the Construction Industry). Sutton and Hunter want to see this practice spread to all manufacturers that make valves, as well as the other most commonly counterfeited construction items, including steel, fasteners, pipes and circuits. They say the industry already has an electronic data-sharing infrastructure that can be leveraged for sharing the unique identifier that would be encoded to each tag, providing a means for all parties in the supply chain and end users to verify its authenticity.
“One of my goals, and one reason I work with Fiatech, is to promote the integration of RFID sooner rather than later,” Sutton says. The bigger goal, he adds, is to get all stakeholders, from manufacturers to project owners, to understand the value RFID provides. While Sutton has experience with active RFID technology, he believes standardized passive UHF tags are the only solution, because of their lower cost and long life. (Several years ago, Zachry Construction participated in a pilot with Fiatech, in which they used active tags to track assets inside a lay-down yard at a job site.) Plus, a standard approach will keep costs down for each party that wants to track materials. “At a job site, I once saw a fabricator attaching active tags to material that was already carrying passive tags,” he says, “but because they did not have passive readers, they could not utilize the tags.”
Despite slow adoption rates, Sutton is encouraged by how much he has seen passive RFID systems mature. “A lot of people perceive passive RFID tags as no different from bar codes, which is not true,” he says. “The read range on UHF tags is far greater than it was five to 10 years ago. Now, we can get 60- or 100-foot reads from passive tags.” But, he adds, “end users do still find active tags superior for some applications, based on RF interference or other factors.”
Interest in leveraging RFID for improving traceability throughout a building’s life cycle is growing in Hong Kong and throughout the developing world, says Evelyn Ong-Halboth, Xerafy’s sales director. “More governments should [require vendors to] use RFID, because it helps them know who to hold accountable for using low-quality materials,” she says.
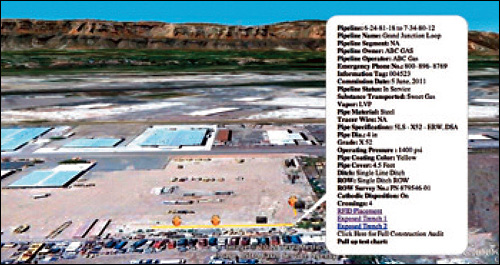
DPR, CCC and other construction companies are convinced RFID can improve employee security and safety, which is no surprise to Fiatech’s Hunter. “In the capital projects industry, if you can improve safety, you almost automatically get a hall pass and the technology gets adopted,” Hunter says. Convincing manufacturers and building owners they can use RFID to fight counterfeiting and improve construction and building maintenance, he says, will take more work.
Hong Kong Housing Authority Issues RFID Mandate
In 2007, the Hong Kong Housing Authority, which implements the region’s public housing projects, began studying how it might use RFID to control the quality of important building materials, track the building process and make building maintenance systems more efficient. It initiated a pilot program to examine the effectiveness of embedding passive RFID tags in precast concrete façades used in its residential buildings. Today, the agency requires all its contractors to attach an RFID tag to each precast concrete façade, as well as to every wooden door, aluminum window and metal security gate they install.
The RFID mandate was issued in early 2012, says Vincent Chau, senior structural engineer on the agency’s Components and Materials team. The first residential apartment block to be constructed with all RFID-tagged components is due to open in mid-2014. With approximately 1,600 flats, the housing block will contain roughly 18,000 RFID tags.
Contractors are required to use passive tags encoded with a unique identifier compliant with the GS1 EPC GIAI-96 standard. They are free to select the RFID supplier and component manufacturers, but the tags must be mounted at designated locations on or in specific components. Contractors also must collect logistics and manufacturing information, and keep it associated with each unique tag ID, along with the date and time each component was delivered to the site (by reading the tag upon receipt of the component) and the date and time the component was installed in the building (again, by reading the tag).
Contractors must then deliver these electronic records to the Housing Authority through a Web-based interface, to enable the agency to track the components through the supply chain and into service in the building. “Whenever there are latent defects or major quality issues, the [RFID] data enables us to quickly retrieve essential background information,” Chau says.
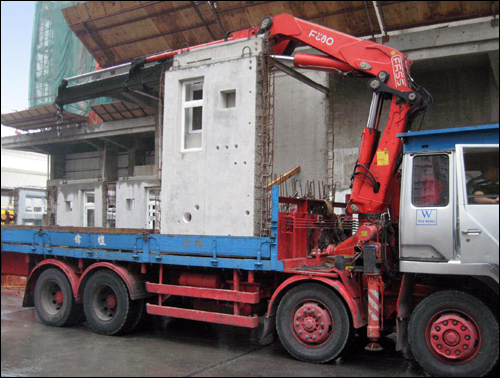
Tracking building components is not the Housing Authority’s first foray into RFID. In 2010, the agency’s Estate Management Division began attaching RFID tags to important safety and security devices, such as water pumps, fire alarms, electricity generators and closed-circuit television cameras. The Housing Authority’s maintenance contractor has already attached tens of thousands of passive tags to these assets in existing housing blocks, and adds them to the devices in new blocks as they are constructed. Contractor employees carry handheld RFID readers to collect tag data from these devices during regularly scheduled inspections as well as repairs. The tag data is stored, along with the maintenance and repair logs, on a central server the Housing
Authority can access to confirm the devices’ proper functionality or to research their repair history in the event of an accident or security failure. In addition, as new housing blocks are constructed, the Housing Authority is using RFID tags mounted on trucks to track the removal and disposal of demolition materials and other waste.